Bend Titanium: A Comprehensive Guide
Updated : Mar. 17, 2025Titanium metal is widely used in aerospace, medical, chemical and other fields due to its excellent strength, low density and excellent corrosion resistance. Bending is one of the commonly used forming processes in titanium metal processing.
Through bending, titanium materials can be processed into various complex shapes to meet the needs of different application fields.
Learn about bending types
Titanium alloy bending processing methods mainly include cold bending and hot bending.
Cold bending titanium
Cold bending is the process of bending titanium alloys at room temperature, suitable for thin-walled materials with high precision and good surface quality.
Common methods: CNC bending, press bending, roll bending.
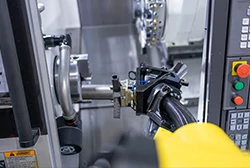

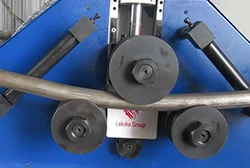
Application & limitations: Ideal for thin-walled titanium alloys but requires careful springback control due to low elastic modulus. Poor ductility may cause fractures with small bending radii.
Key factors: Bending radius, angle, thickness, and springback. Proper parameter selection and annealing help prevent fractures and reduce defects.
Hot bending titanium
Hot bending involves heating titanium alloys to improve plasticity, reduce stress, and enhance formability.
Common methods: Rotary bending, hydraulic bending.
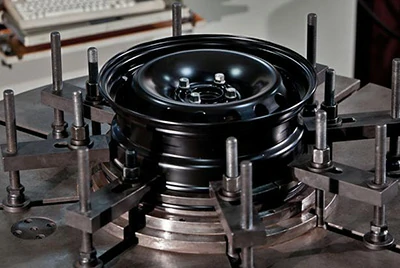
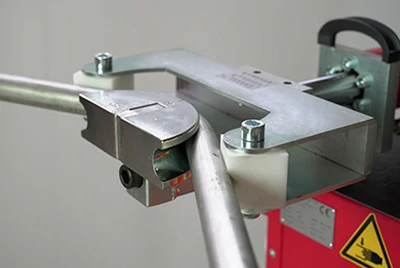
Necessity & advantages: Titanium alloys have poor plasticity at room temperature. Hot bending improves plasticity, lowers stress, reduces cracking and wrinkling risks, and enables smaller bending radii for complex shapes.
The process of hot bending includes:
Heating method: Common heating methods include furnace heating and high-frequency induction heating. High-frequency induction heating can achieve local heating and reduce energy consumption.
Temperature control: The thermal deformation temperature range of titanium alloy is narrow, and the heating temperature needs to be precisely controlled. Generally between 700℃ and 900℃.
Insulation time: After heating, a certain insulation time needs to be maintained to ensure uniform heating of the material. Too long insulation time may cause coarse grains and affect material properties..
Cooling and post-processing after hot bending: The cooling method after hot bending has an important impact on material properties. Generally, air cooling or water cooling is used, and the specific method is determined according to the material and process requirements. In addition, stress relief annealing may be required after hot bending to eliminate internal stress and improve material properties.
Preparation before bending
Understanding material properties
Different grades of titanium alloys have their own characteristics that affect their bending performance.
Grade 2 titanium: Industrial pure titanium, has high ductility and is easy to bend.
Grade 5 titanium alloy: Ti-6Al-4V has higher strength, but lower ductility and requires special attention when bending.
Understanding the characteristics of the titanium alloy used will help choose the appropriate processing method and parameters.
Surface inspection and cleaning
Titanium alloys are sensitive to surface defects that may lead to cracks or material failure.
Inspection: Carefully inspect the surface of the material to ensure there are no scratches, nicks or other defects.
Cleaning: Use a non-halogenated solvent such as isopropyl alcohol or acetone to remove oil, dirt or grease. After cleaning, wear clean cotton gloves when handling titanium alloys to prevent re-contamination.
Thorough cleaning helps avoid contamination of the material during the bending process and ensures processing quality.
Device selection and setup
Use the proper tools and equipment, and set them up correctly, to achieve precise bends.
Fixing: Use clamps or vises to secure the titanium to prevent slipping during the bend.
Tools: Choose the right bending tool, such as an axle press or press brake, and make sure it is set up correctly.
Heating: When needed, use a heating tool, such as a propane torch or induction heater, to evenly heat the titanium to reduce the risk of cracking.
Proper equipment setup and operation can help improve bend accuracy and reduce defects.
Determine the bend radius
Titanium alloys have low elongation, so the choice of bend radius is critical.
Radius selection: A larger bend radius helps prevent cracking or deformation. The specific radius depends on the thickness and type of titanium alloy.
Ensure that the bend geometry meets the requirements, especially in applications that require high precision.
Simulation testing and calibration
Before the actual bending, simulated tests are performed on scrap of the same titanium alloy to optimize the process parameters.
Testing: Evaluate the material's behavior under pressure or heat to identify the "springback" phenomenon.
Adjustment: Based on the test results, adjust the equipment settings to compensate for the springback and ensure that the final bend reaches the desired angle.
Choose different bending methods
Rotary Draw Bending
Rotary bending is a method of precisely controlling the bending radius and angle by rotating the die and mandrel, which is suitable for high-precision bending of titanium alloy pipes.
Advantages: It can achieve high-precision bending and is suitable for processing complex shapes.
Applicable products: Mainly used for bending of titanium alloy thin-walled pipes.
CNC Bending
CNC bending uses CNC technology to achieve automated control to ensure bending accuracy and consistency. It is suitable for complex shapes and small batch production to achieve automated control to ensure bending accuracy and consistency.
Advantages: high precision, high efficiency, suitable for complex shapes and small batch production.
Applicable products: suitable for bending processing of titanium alloy plates, thin-walled pipes, etc.
Hydraulic bending
Hydraulic bending is powered by a hydraulic system and is suitable for bending large-size and thick-walled materials.
Advantages: Able to handle thicker titanium alloy materials and suitable for mass production.
Applicable products: Mainly used for bending titanium alloy plates and thick-walled pipes.
Roll bending
Roll bending realizes continuous bending of titanium alloy plates through the rotation of rollers, and is suitable for large radius bending processing.
Advantages: Suitable for large radius bending, and can continuously process long-sized workpieces.
Applicable products: Suitable for thin-walled titanium alloy plates.
Press brake bending
Using the upper and lower molds of the bending machine, the bending of titanium alloy plates is achieved through pressure, which is suitable for small and medium batch production.
Advantages: Suitable for small and medium batch production, and can achieve high-precision bending.
Applicable products: Mainly used for bending processing of titanium alloy plates.
Precautions for bending titanium
Springback control: Titanium alloy has a large elastic modulus and is prone to springback after bending. It is necessary to reserve an appropriate amount of springback before bending to ensure the dimensional accuracy of the final product.
Temperature control: During hot bending, the plasticity of titanium alloy increases with increasing temperature. However, too high a temperature may cause the oxide film to be damaged and affect the material properties. Therefore, it is necessary to accurately control the heating temperature and time.
Lubrication and cooling: During the bending process, proper lubrication can reduce friction, reduce tool wear, and improve surface quality. For hot bending, the cooling rate also needs to be controlled to avoid internal stress.
Post-processing: After bending, stress relief annealing may be required to eliminate internal stress and improve material properties. In addition, the surface may need to be cleaned and polished to remove the oxide layer and improve the surface quality.
Common problems in the bending process
Cracking and fatigue
Cause: Titanium alloys have high strength and low ductility, which can easily lead to cracking and fatigue.
Solution:
- Avoid excessive bending: Apply constant pressure to avoid exceeding the material limit to prevent cracking.
- Pre-bending heat treatment: Improve the ductility of titanium alloys through annealing treatment and reduce the risk of cracking.
- Surface inspection and cleaning: Thoroughly inspect the material surface before bending to remove defects and contaminants.
- Post-bending inspection: Use non-destructive testing methods, such as dye penetrant testing, to check for cracks after bending.
Rebound
Cause: Titanium alloy has a tendency to return to its original shape after bending, i.e. springback.
Solution:
- Overbending: Moderate overbending to compensate for springback.
- Heating control: Maintain uniform heating temperature to reduce springback.
- Stress relief annealing: Stress relief annealing is performed after bending to reduce residual stress and reduce springback.
Surface damage and wear
Cause: Friction between titanium and bending tools can cause surface damage.
Solution:
- Lubrication: Use a lubricant compatible with titanium, such as molybdenum disulfide, to reduce friction.
- Tool selection: Use smooth, well-maintained tools to avoid scratches caused by rough or sharp tools.
Inaccurate bending
Cause: Lack of precise control during the bending process, resulting in inaccurate bends.
Solution:
- Tool calibration: Ensure all bending tools and machines are properly calibrated, using digital controls and measuring equipment for increased accuracy.
- Dummy tests: Perform mock tests using scrap material to fine-tune settings and determine the correct bend angle.
- Continuous pressure: Apply steady, even pressure throughout the bending process to avoid sudden or uneven forces that can cause inaccurate bends.
Heating problems
Cause: Improper heating can cause oxidation, embrittlement, and uneven bending.
Solution:
- Temperature monitoring: Use a thermal crayon or infrared thermometer to monitor the temperature of the titanium alloy to avoid overheating.
- Uniform heating: Heat the titanium alloy evenly in the bending area to prevent warping and inconsistent bending.
- Cooling control: Allow the titanium alloy to cool gradually after bending to avoid stress and deformation caused by rapid cooling.
FAQ
How do you bend titanium without damaging it?
Use a tube bender or arbor press, apply lubricant, maintain temperature between 540°C and 730°C, and avoid overheating.
What tools are needed to bend titanium?
Propane or oxy-fuel blowtorches, axial presses, hydraulic tube bender, vises, clamps.
Which heating method is best for bending titanium?
Propane or oxy-fuel torches heat to 540°C to 730°C, avoid overheating, and use argon to prevent oxidation.
How do you achieve precise bending of titanium?
Use a dedicated tube bender and mandrel, control pressure and speed, and lubricate to reduce friction.
What is the difference between bending thin titanium and bending thick titanium?
Difference between bending thin titanium and thick titanium: Thin titanium uses cold forming, thick titanium needs hot forming, and thick titanium has higher rigidity.
How do you prevent titanium from springing back after bending?
Overbending: Set the bend angle to 87° or 88° to compensate for springback.
Heating: Heat the titanium to a dark red color, especially for larger bends.
Equipment: Use a press brake or three-roller bender to ensure the titanium is firmly fixed.
Accurate calculation: Calculate and adjust the amount of springback during the bending process to ensure precise control.