Comprehensive Welding Guide for Ti-6Al-4V Grade 5 Titanium Alloy
Updated : Feb. 7, 2025Ti-6Al-4V (Grade 5) titanium alloy, as one of the most widely used alloys in the titanium industry, accounts for more than half of global titanium alloy consumption. Its exceptional strength-to-weight ratio, corrosion resistance, heat treatability, excellent weldability, and machinability make it the material of choice across various industries, including aerospace, medical devices, marine engineering, and automotive manufacturing.
However, the diverse applications of Ti-6Al-4V (Grade 5) bring increased demand for material connection methods, particularly welding. Without a deep understanding of welding process details, issues such as weld joint embrittlement and equipment damage may arise, compromising project quality and service life. Key challenges include:
- What factors contribute to joint embrittlement?
- How to ensure weld joint quality in high-temperature or corrosive environments?
- What welding methods are suitable for Ti-6Al-4V (Grade 5)?
This article provides an in-depth analysis of welding methods for Ti-6Al-4V (Grade 5) titanium alloy. By examining its physical and chemical properties and heat treatment characteristics, it offers insights into designing effective welding processes, improving weld joint quality, and extending equipment service life. Whether you are a welding expert or a titanium alloy user, this guide will serve as a valuable reference for addressing these challenges.
Weldability of ti-6al-4v grade 5: understanding material characteristics
To achieve high-quality welding of Ti-6Al-4V Grade 5 (AMS4911) titanium alloy, it is essential to first analyze its physical and chemical properties, particularly its behavior at high temperatures and interactions with gas elements such as hydrogen, oxygen, and nitrogen.
Weld zone embrittlement: gas absorption and its impact at high temperatures
At room temperature, Ti-6Al-4V Grade 5 exhibits excellent stability and corrosion resistance due to its natural oxide protective layer. However, at elevated temperatures, especially in molten states, AMS4911 Grade 5 becomes highly reactive with gases such as oxygen (O₂), nitrogen (N₂), and hydrogen (H₂). These gases can infiltrate the weld zone, leading to embrittlement and compromising the weld's ductility and toughness.
Gas Activity at Elevated Temperatures
- Above 300°C: Starts absorbing hydrogen (H₂) without protection.
- Above 600°C: Accelerated absorption of oxygen (O₂).
- Above 700°C: Significant nitrogen (N₂) absorption begins.
Once these gases are absorbed by titanium, brittle phases form in the weld joint area, causing lattice distortion, reduced plasticity, and toughness, which in severe cases can lead to joint fractures.
Effects of various elements on weld joint embrittlement
1.Oxygen and Nitrogen
Oxygen (O) and nitrogen (N) readily form interstitial solid solutions with titanium at high temperatures, causing severe lattice distortion. While this distortion increases the strength and hardness of the material, it significantly reduces its plasticity and toughness.
*Interstitial solid solution: Foreign elements (such as O, N, H) occupy lattice interstices in titanium, forming a solid solution.
Nitrogen (N) has a more pronounced effect than oxygen. The solid solution of nitrogen and titanium causes more severe lattice distortion, further enhancing strength and hardness but drastically reducing material plasticity.
2.Hydrogen
Hydrogen (H) has the most significant impact on mechanical properties among gaseous impurities. Hydrogen reacts with titanium to form titanium hydrides (TiH₂, γ phase), typically appearing as fine lamellar or needle-like structures with very low fracture strength. These hydrides act as microcrack initiators, significantly reducing the plasticity and toughness of the weld joint.
3.Carbon
At room temperature, the solubility of carbon in α-titanium is 0.13%. When carbon content exceeds this solubility, brittle TiC precipitates form and tend to distribute in a network pattern. As carbon content increases, the amount of TiC rises, rapidly decreasing weld plasticity and making cracks more likely under welding stress.
4.Other Elements
Adding alloying elements such as Al, Ni, Si, Nb, Cr, Mn, V, and Mo to the weld metal can enhance the strength, oxidation resistance, and corrosion resistance of Ti-6Al-4V Grade5 titanium alloy. These alloying elements improve overall performance by forming strengthening phases or refining grain structures.
Common welding defects and their countermeasures
To provide a systematic understanding of the primary risks associated with welding Ti-6Al-4V Grade 5, this section addresses common issues such as "welding cracks," "welding porosity," and "welding deformation," along with suggested countermeasures or recommendations.
Welding cracks: high-temperature dwell time and grain growth
The high melting point and poor thermal conductivity of Ti-6Al-4V Grade 5 result in higher molten pool temperatures and longer liquid phase dwell times during welding. This promotes grain growth, reduces joint ductility, and increases the likelihood of welding cracks. For titanium alloy welding, it is recommended to use energy-concentrated heat sources (such as TIG or laser welding). Additionally, controlling the welding current, increasing welding speed, and minimizing high-temperature dwell times can help reduce the risk of welding cracks.
Welding porosity: hydrogen as the primary culprit
During AMS4911 Grade 5 welding, impurities such as C, N, H₂, CO₂, and H₂O in shielding gas, base material, or filler wires can cause welding porosity. Hydrogen porosity is particularly common, often distributed in the weld center and near the fusion line. It is advised to strictly control material purity and shielding gas quality (≥99.99% Ar). Preheating and dehumidifying treatments before welding may be necessary. Regular inspections of filler wire and base material surface cleanliness are also recommended.
Welding Deformation: More Pronounced Than Stainless steel
Due to its low elastic modulus, AMS4911 Grade 5 exhibits welding deformation that can be up to double that of stainless steel. Using backing plates and clamps to secure the workpiece can help reduce deformation. Additionally, improving the workpiece's heat dissipation capability and minimizing high-temperature dwell times can reduce weld oxidation and deformation.
Welding methods and material selection: TIG welding as the preferred process
Welding methods
Ti-6Al-4V (Grade 5) titanium alloy is highly sensitive to gas elements such as oxygen (O₂), nitrogen (N₂), and hydrogen (H₂). Traditional welding methods such as stick arc welding, gas welding, and CO₂ gas-shielded welding are generally unsuitable, as they can introduce undesirable gases at high temperatures, leading to defects like embrittlement and cracking. Therefore, selecting the right welding process is critical. Common welding methods include:
- TIG Welding (Tungsten Inert Gas Welding): TIG welding is widely used for Ti-6Al-4V Grade 5 titanium alloy due to its concentrated energy and controllable welding quality.
- Plasma Arc Welding, Electron Beam Welding, Laser Welding, and Diffusion Welding: These high-precision methods are suitable for specific thicknesses and conditions, such as welding aerospace engine components and medical implants.
Welding material selection: ERTi-5 filler wire
The choice of welding materials directly affects the quality and performance of the welded joint. For Ti-6Al-4V Grade 5 titanium alloy, ERTi-5 filler wire is recommended, with the following specifications:
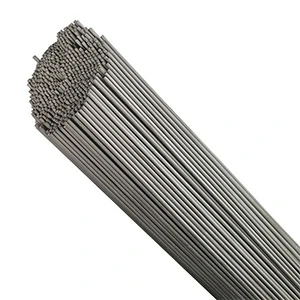
ERTi-5 Solid Filler Wire
Standards Compliance: Complies with AWS A5.16 and ASME SFA-5.16 standards for titanium and titanium alloy welding wires and filler materials.
Chemical Composition: Closely matches the base material to ensure chemical and mechanical consistency between the weld and the base material, enhancing joint reliability and service life.
Name | Al | V | C | O | N | H | Fe | Ti |
---|---|---|---|---|---|---|---|---|
ERTi-5 | 5.5~6.75 | 3.5~4.5 | ≤0.05 | 0.12~0.20 | ≤0.03 | ≤0.015 | ≤0.22 | Re |
TIG welding process and trials: key steps to ensure quality welds
To ensure the weld quality of Ti-6Al-4V Grade 5 titanium alloy, every step of the welding process must be strictly controlled. Below is a detailed step-by-step guide, from groove preparation to stress relief:
Welding process: from groove to stress relief
- Groove Preparation: Use double-sided weld grooves whenever possible, processed with mechanical grinding wheels or carbide wheels to avoid contamination from residual abrasive particles.
- Pre-Welding Cleaning: Use a 5%–10% sodium hydroxide solution or industrial acetone to remove grease and dirt. Clean a 25 mm area around the weld edges with a stainless steel wire brush to eliminate impurities.
- Welding Environment: Ensure proper indoor ventilation, dust-proofing, and wind-proofing. Maintain relative humidity below 80% and avoid excessively low temperatures. The welding area should be separated from other material operations.
- Tack Welding: Use the same parameters as the main welding process. Misalignment and tack weld quality must be strictly controlled.
- Gas Protection in Welding Zone: Use 99.99% pure argon as shielding gas, tail gas, and backing gas. Start gas flow before welding and stop it only after the weld cools to a silver-white color to prevent oxidation.
- Arc Striking: Use pulse or high-frequency arc initiation.
- Welding Parameters: Select the appropriate tungsten electrode diameter and welding current based on the thickness of the base material. Maintain low heat input for optimal weld quality.
Typical parameters are shown in the table below:
Base material thickness mm | Tungsten electrode diameter mm | Welding current A | Nozzle diameter mm | Shielding gas | Exhaust gas | Back shielding gas | Interpass temperature ℃ | Welding speed m/h |
---|---|---|---|---|---|---|---|---|
0.5~2 | 1.5 | 30~100 | 8~12 | Ar; 8~20L/min | Ar; 10~20L/min | Ar; 15~25L/min | ≤100 | 6~15 |
>2~10 | >2~3 | 100~180 | 10~20 | Ar;10~20L/min | ||||
>10 | >3~4 | 120~200 | 12~20 |
- Inter-layer Cleaning: For multi-layer welding, remove oxidation colors (light yellow or pale blue) before proceeding to the next layer.
- Weld Dimensions: Weld reinforcement should be controlled within 0–3 mm. Fillet welds should transition smoothly into the base material to avoid abrupt changes.
- Stress Relief: If necessary, employ methods such as peening, ultrasonic impact treatment, vibration aging, or annealing heat treatment (480–650°C, holding for 60–360 minutes) to reduce residual stress.
Process trials: small-batch test welding to verify feasibility
To validate the feasibility of the welding process and ensure weld quality, Chalco conducted a series of trials. For example, a 3 mm thick Ti-6Al-4V Grade 5 titanium alloy plate was subjected to the above TIG welding process, yielding the following results:
- Visual Inspection: The weld was smooth, with no cracks or lack of fusion. The surface exhibited a silver-white or light golden color, indicating excellent atmospheric control during welding.
- Non-Destructive Testing: Penetration testing and radiographic inspection revealed no internal defects such as porosity or inclusions.
- Mechanical Properties: Tensile strength, yield strength, and bend properties met or exceeded standard requirements, demonstrating excellent weld toughness.
- Bend Properties: A 180° bend test of the welded joint showed no defects, indicating superior bending performance.
Item | Width mm | Thickness mm | Area mm2 | Ultimate total load N | Tensile strength MPa | Yield strength MPa | Elongation after fracture % | Fracturing properties and location |
---|---|---|---|---|---|---|---|---|
1 | 18.99 | 2.94 | 55.83 | 54881 | 983 | 894 | 18.3 | Tough fracture; weld |
2 | 18.99 | 3.01 | 57.16 | 56017 | 980 | 891 | 21.6 | Tough fracture; weld |
In this article, we thoroughly examined the welding processes and critical techniques for Ti-6Al-4V Grade 5 titanium alloy. Understanding these welding methods not only enhances weld quality but also ensures the long-term stable operation of equipment. Improving weld quality directly impacts the practical applications of Ti-6Al-4V Grade 5 across industries.
Next, we will delve into the broad applications of this titanium alloy across various sectors and explore how Chalco delivers high-quality product solutions for these applications.
Applications of Ti-6Al-4V grade 5
Thanks to its high strength, corrosion resistance, and excellent high-temperature performance, Ti-6Al-4V Grade 5 titanium alloy is widely used in aerospace, petrochemical, marine engineering, high-end automotive manufacturing, electronics, and electrical power sectors.
Aerospace
In aerospace, Ti-6Al-4V Grade 5 is extensively used in aircraft structural components, engine parts, and spacecraft shells. Its high strength-to-weight ratio and heat resistance meet the stringent requirements for lightweight and high-performance materials, significantly improving fuel efficiency and payload capacity.
Examples: Structural components of Boeing 787 Dreamliner and engine parts of Airbus A380.
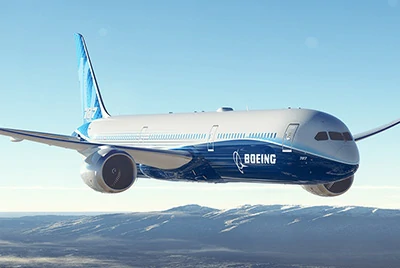
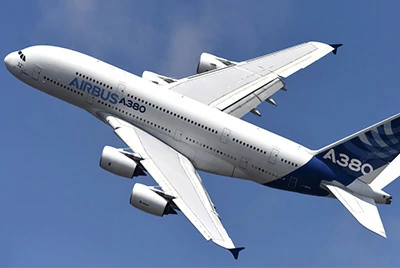
Medical industry
In the medical field, Ti-6Al-4V Grade 5 is valued for its exceptional biocompatibility and strength, making it ideal for surgical instruments and medical implants.
- Joint replacements (knee and hip)
- Spinal fusion devices
- Dental implants
- Cardiac stents
- Prosthetics and orthotics


Petrochemical industry
Ti-6Al-4V Grade 5 is commonly used in reactors, piping systems, and storage tanks in the petrochemical sector. Its outstanding resistance to corrosion, particularly against chlorides and sulfides, ensures long-term stability in harsh chemical environments.
Examples: Piping systems on offshore oil platforms and highly corrosive reactors in chemical plants.
Marine engineering
In marine engineering, Ti-6Al-4V Grade 5 is employed in subsea pipelines, offshore platforms, desalination plants, and submersible devices. Its superior seawater corrosion resistance and high strength-to-weight ratio provide excellent structural stability and anti-corrosion performance in marine environments.
Examples: Subsea oil and gas pipelines, offshore wind turbine platform components, and key parts of submersibles.
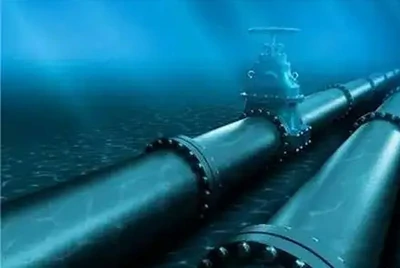
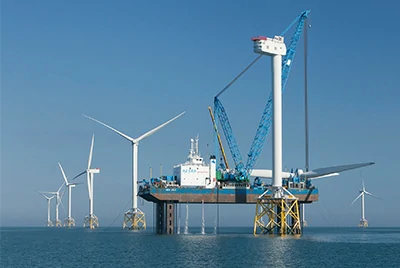
High-End automotive manufacturing
Ti-6Al-4V Grade 5 is used in high-performance automotive applications, including engine components, body structures, and exhaust systems. Its lightweight and high-strength characteristics enhance vehicle performance, fuel efficiency, safety, and durability.
Examples: Engine blocks in high-performance sports cars and structural components in race cars.
Electronics and electrical power
Ti-6Al-4V Grade 5 is utilized in high-performance electronic components, precision instruments, and critical parts of electrical equipment. Its stable physical properties and excellent corrosion resistance ensure long-term reliability in high-temperature and high-humidity environments.
Examples: Casings for high-frequency electronic devices and critical components in power transformers.
Ti-6Al-4V grade 5 products supplied by Chalco
To meet the diverse needs of various industries and applications, Chalco is committed to delivering high-quality Ti-6Al-4V Grade 5 titanium alloy products globally. We also offer tailored specifications and dimensions based on customer requirements. Below are our main product categories:
-
Ti-6Al-4V Grade 5 Titanium Plates
High strength-to-weight ratio: Ideal for supporting critical structural loads.
Excellent corrosion resistance: Suitable for harsh environments.
Good formability: Adaptable to various manufacturing processes.
-
Ti-6Al-4V Grade 5 Titanium Bars
Exceptional mechanical properties: Suitable for components requiring high strength and wear resistance.
Good machinability: Ideal for cutting, drilling, turning, and other machining processes.
-
Ti-6Al-4V Grade 5 Titanium Tubes
Superior corrosion resistances: Suitable for transporting corrosive media.
High-temperature stability: Maintains structural integrity under extreme conditions.
-
Ti-6Al-4V Grade 5 Titanium Wire
High ductility: Suitable for applications requiring fine precision processing.
Stable diameter precision: Ensures product consistency and quality.
-
ERTi-5 Titanium Welding Wire
High-purity material: Ensures optimal mechanical performance and corrosion resistance at the weld joints.
Consistent chemical composition: Meets AWS A5.16 and ASME SFA-5.16 standards, ensuring weld quality.
-
Ti-6Al-4V Grade 5 Titanium Forgings
High strength and toughness: Ideal for components subject to high stress and impact.
Precision forging: Ensures the quality of complex shapes with tight tolerances.
-
Ti-6Al-4V Grade 5 Titanium Castings
High-precision casting: Accommodates complex shapes and stringent tolerance requirements.
Outstanding internal quality: Advanced casting processes minimize internal defects.
-
Custom Solutions
Development and production of titanium alloy products with special specifications or performance based on customer requirements.
One-stop service: From design to production, tailored to meet unique project needs.
If you have specific requirements or questions regarding Ti-6Al-4V Grade 5 titanium alloy products, such as special sizes, shapes, surface treatments, or technical support, feel free to contact Chalco. We are committed to providing professional technical solutions and exceptional customer service to support the success of your projects.