Titanium vs Aluminum Comparison: Comprehensive Guide to Selecting the Best Material
Updated : Feb. 7, 2025In modern manufacturing, titanium (Ti) and aluminum (Al) stand out as two of the most popular lightweight metals. Their applications span across industries such as aerospace, automotive, medical devices, and consumer electronics. Whether your goal is extreme weight reduction or superior strength and corrosion resistance, each material offers unique advantages. However, striking the optimal balance between performance, cost, and machinability remains a key challenge for engineers and designers.
This article delves into the critical aspects of "titanium vs aluminum," including weight, strength and hardness, corrosion resistance, thermal conductivity, machinability, weldability, and cost. By analyzing detailed data and real-world applications, we aim to equip you with the insights needed to make informed decisions for your project materials.
Titanium (Ti)
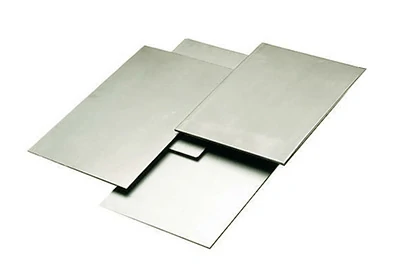
Key characteristics
High Strength-to-Weight Ratio
Titanium exhibits an exceptional strength-to-weight ratio, surpassing most steels at the same weight. This is attributed to its hexagonal close-packed (HCP) crystal structure, which maintains high strength and toughness even at low temperatures.
Outstanding Corrosion Resistance
Titanium naturally forms a stable and dense titanium dioxide (TiO₂) oxide layer, providing long-term protection against saltwater, chloride ions, and chemical exposure.
Biocompatibility
Titanium’s excellent biocompatibility makes it ideal for medical implants and high-end medical devices, such as artificial joints and dental implants, ensuring safe and long-term integration with human tissue.
Superior High-Temperature Performance
With a melting point of 1668°C, titanium alloys retain strength under high-temperature conditions, making them suitable for aerospace engines and rocket components.
Alloying Versatility
Combining titanium with elements like aluminum and vanadium enhances its mechanical properties. For instance, Ti-6Al-4V offers excellent strength and machinability, making it a preferred choice in high-performance industries.
Applications
Aerospace: Engine components, structural supports, and high-strength parts for lightweight and reliable performance.
Medical: Implants and surgical instruments due to their biocompatibility and durability.
High-End Sports Equipment: Bicycle frames, golf clubs, and other performance gear.
Additive Manufacturing (3D Printing): Ideal for complex, high-performance components in aerospace and medical sectors.
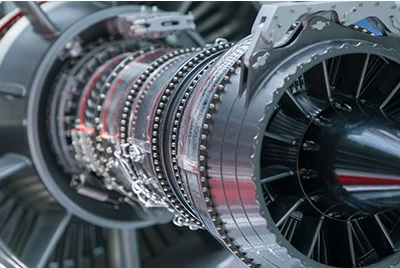
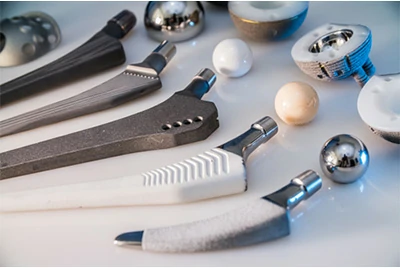
Aluminum (Al)
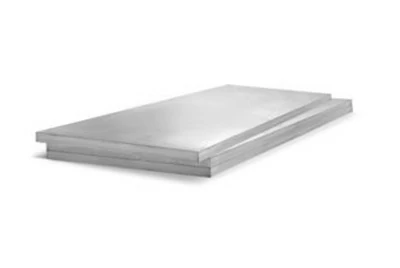
Key characteristics
Lightweight
Aluminum is only about one-third the density of steel, making it an excellent choice for applications requiring weight reduction, such as in aerospace and transportation.
Exceptional Thermal and Electrical Conductivity
With a thermal conductivity of 205–235 W/m·K, aluminum is ideal for heat exchangers, electronics housings, and kitchenware. Its electrical conductivity (~62% of copper) makes it suitable for wires and cables.
Cost-Effectiveness and Easy Machinability
Abundant and relatively inexpensive, aluminum is easy to machine, making it suitable for mass production and rapid prototyping.
High-Strength Aluminum Alloys
Pure aluminum has low strength, but through alloying (e.g., 7075, 6061) and heat treatment, aluminum alloys can achieve excellent strength-to-weight ratios.
Recyclability
Aluminum is highly recyclable, with minimal loss in quality. This makes it an environmentally friendly and economically sustainable choice.
Applications
Aerospace: Aircraft structures and engine parts for weight reduction and fuel efficiency.
Transportation: Automotive body panels, railway cars, and high-speed trains for better fuel economy.
Construction: Structural components, curtain walls, and decorative panels for their durability and aesthetic appeal.
Electronics: Laptop casings, smartphone bodies, and heat sinks for their lightweight and thermal management properties.
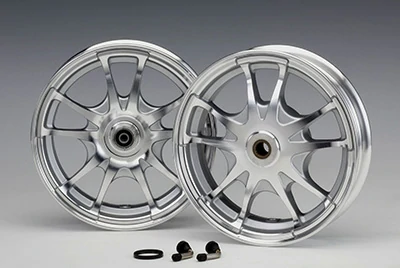

Color differences: distinguishing titanium vs aluminum
In material selection, color serves as an intuitive and essential factor for differentiating Titanium and Aluminum. Accurate identification of the material's color helps prevent errors in projects, ensuring both product consistency and aesthetic appeal.
Aluminum
Basic Color
Aluminum typically exhibits a bright silver-white color with a noticeable metallic luster.
Depending on surface treatments, the color can range from silver to dark gray.
Effect of Surface Treatments
Anodizing: Anodized aluminum surfaces can be colored to achieve a diverse appearance while enhancing corrosion resistance.
Brushed or Polished Finish: Brushing or polishing adds a sleek, satin or reflective finish, enhancing aluminum’s modern aesthetic.
Smooth Surfaces
Smooth aluminum surfaces often appear brighter and shinier, reflecting light to create a clean and polished look.
Titanium
Basic Color
Titanium also displays a silver-white appearance, but its tone is darker and less reflective compared to aluminum.
Its natural finish gives a subtle, subdued sheen, imparting a more premium and robust visual effect.
Effect of Surface Treatments
Natural Oxidation: Titanium naturally forms a dense oxide layer, which deepens its tone to a gray or dark silver hue.
Anodizing: Oxidized titanium can achieve a wide range of rich colors, including rust-like tones, while enhancing corrosion resistance.
Visual Feel
Titanium's surface tends to have a matte or soft satin finish, exuding an understated elegance and a more professional-grade appearance.
Titanium vs Aluminum: core performance comparison
To offer a clearer picture of "aluminum vs titanium", the following table summarizes the key metrics, allowing for a quick comparison of weight, strength, hardness, corrosion resistance, thermal conductivity, and cost.
Characteristics | Titanium | Aluminum |
---|---|---|
Density (g/cm³) | About 4.5 g/cm³ | About 2.7 g/cm³ |
Melting point (℃) | 1668 | 660 |
Tensile strength (MPa) | 230–1400 (variable depending on alloy/heat treatment) | 90–690 (can be improved by alloying and heat treatment) |
Thermal conductivity (W/m·K) | About 17–22 (low thermal conductivity) | 205–235 (high thermal conductivity) |
Electrical conductivity (copper=100%) | About 3.1% | About 62% |
Corrosion resistance | Excellent, especially in marine, high-salt, chemical environments | Good, can be improved by surface treatment such as anodizing |
Processing difficulty | High, requires impact-resistant tools, reduced-speed cutting, etc.; welding requires professional protection | Low, easy to cut and weld; high process maturity |
Price/cost | Relatively expensive; both raw material and processing costs are high | Low; suitable for large-scale industrial production |
Weight comparison: is titanium lighter than aluminum?
"Is titanium lighter than aluminum?” is often asked because many people have heard that "titanium is stronger than steel but lighter than steel.” However, compared with aluminum, this is not the case.
Density comparison
Titanium’s density is approximately 4.5 g/cm³, whereas aluminum is only 2.7 g/cm³.
This makes titanium 66% denser than aluminum when measured by volume.
Strength-to-weight ratio
Despite its higher density, titanium has a superior strength-to-weight ratio (187 kN·m/kg) compared to aluminum (158 kN·m/kg).
Titanium can provide greater strength with less material, making it ideal for weight-critical applications requiring maximum structural integrity.
Aluminum’s low density gives it an edge in applications prioritizing lightweight construction without extreme strength requirements.
Material selection strategy
For Maximum Weight Reduction
When the primary goal is minimizing weight and strength requirements are moderate, aluminum is the more practical choice due to its lower density.
For High-Strength Applications
In scenarios where strength and durability are crucial, titanium enables engineers to use less material while achieving equal or greater performance, often resulting in comparable or lower final part weight.
In general, in terms of absolute density, the answer to the question "which is lighter aluminum or titanium?” is: "aluminum is lighter”.
However, if strength and volume reduction are considered comprehensively, titanium also shows its "lightweight” side, especially in complex application scenarios that require high strength and lightness, the advantages of titanium are more obvious.
Strength and hardness: aluminum vs titanium strength
Tensile strength (UTS)
Titanium: Typically ranges from 230–1400 MPa, depending on alloy type and heat treatment. For example, Ti-6Al-4V (one of the most common titanium alloys) easily exceeds 900 MPa.
Aluminum: Generally ranges from 90–690 MPa, depending on alloy type and heat treatment. For example, 7075-T6 aluminum alloy has a tensile strength above 600 MPa.
Yield strength (YS)
Titanium: Ranges from 170–1100 MPa, depending on alloy type.
Commercially pure titanium typically has lower yield strength, around 170–480 MPa.
Aluminum: Ranges from 7 MPa to 600 MPa, depending on alloy type.
Yield strength is significantly higher in aluminum alloys compared to pure aluminum, particularly in high-strength grades such as 7075 or 6082.
Hardness
Items | Titanium | Aluminum |
---|---|---|
Tensile strength | 230 MPa - 1400 MPa | 90 MPa - 690 MPa |
Yield strength | 170 MPa - 1100 MPa | 7 MPa - 600 MPa |
Brinell hardness Flexibility | 70 HB | 15 HB (pure aluminum) |
150 HB+ (alloyed aluminum) | ||
Ductility | Low | High |
Impact resistance | Low | High |
Fatigue strength | Varies by alloy | Depending on the alloy, can be quite high |
Items | Generally excellent, especially at high temperatures | Good |
In general, titanium is generally superior to aluminum in terms of tensile strength and hardness, especially in applications with high-end titanium alloys such as Ti-6Al-4V. However, aluminum alloys can also achieve comparable strength and hardness through alloying and heat treatment, and have higher flexibility and ductility. Which material to choose depends on your project needs:
Choose Titanium:
- When high tensile strength, superior hardness, and excellent corrosion resistance are critical.
- Suitable for high-performance applications such as aerospace, medical implants, and extreme environments.
- When the budget allows, as titanium is generally more expensive.
Choose Aluminum:
- When cost-efficiency, good strength, and higher machinability are required.
- Ideal for automotive, electronics, and applications prioritizing lightweight materials with moderate strength.
- For projects needing greater flexibility and ductility, aluminum is often the better choice.
By weighing factors like strength, hardness, weight, and cost, you can make the most appropriate material choice for your project, ensuring optimal performance and efficiency.
Corrosion resistance and durability: aluminum vs titanium - who performs better in complex environments?
Corrosion resistance
Titanium
- Stable Oxide Layer: Titanium naturally forms a dense, stable TiO₂ oxide layer, providing exceptional resistance to seawater, chloride ions, and acidic environments.
- Biocompatibility: Widely used in medical applications, titanium maintains long-term compatibility with bodily fluids without causing adverse reactions.
- Marine Engineering Applications: In demanding environments such as deep-sea pipelines or offshore drilling platforms, titanium maintains its smooth surface for decades, minimizing maintenance requirements.
Aluminum
- Natural Oxide Layer: Aluminum also forms a protective oxide layer in air. However, compared to titanium, the thickness and stability of this layer are inferior.
- High-Corrosion Environments: Without additional treatments, aluminum is prone to pitting or crevice corrosion in high-salt or acidic environments.
- Surface Treatments: Processes such as anodizing or specialized coatings significantly enhance aluminum's corrosion resistance, making it suitable for a broader range of environments.
Durability
Titanium
Low maintenance and highly suited for extreme environments.
Titanium's service life often spans decades or longer, even in severe marine or chemical conditions.
Aluminum
Highly durable in moderate conditions, but in marine or chemical industries, frequent maintenance or use of high-grade aluminum alloys is necessary for longevity.
Aluminum’s cost-effectiveness and lightweight properties make it sufficient for projects in less aggressive environments.
In high-salt or chemically aggressive environments, titanium emerges as the superior choice for corrosion resistance and durability, providing unparalleled performance at a higher cost. For projects requiring cost-efficiency and good corrosion resistance in moderate environments, aluminum remains a highly versatile and viable material.
Thermal conductivity and heat resistance: titanium vs aluminum heat dissipation
In material selection, thermal conductivity and heat resistance play crucial roles in determining the suitability of titanium and aluminum for specific applications. Understanding how these metals perform in terms of heat transfer and high-temperature stability can help you make the best choice for applications requiring effective heat dissipation or high-temperature operation.
Thermal conductivity
Thermal conductivity measures a material's ability to transfer heat, which is critical for applications like heat sinks, heat exchangers, and cookware, where efficient heat transfer is essential.
Aluminum
- Thermal conductivity: ~210 W/m·K.
- Aluminum's high thermal conductivity makes it a preferred choice for heat dissipation applications, such as heat sinks, radiators, and cookware.
Titanium
- Thermal conductivity: ~17 W/m·K.
- Titanium's low thermal conductivity limits its use in heat dissipation-intensive applications. However, its high-temperature stability enables it to remain effective in certain high-heat environments despite its lower heat transfer capability.
Heat resistance
Heat resistance refers to a material's ability to retain its mechanical properties and structural integrity under high-temperature conditions. This is crucial for components operating in extreme heat, such as engine parts and high-temperature industrial equipment.
Titanium: Excellent heat resistance.
Titanium alloys maintain strength and integrity at temperatures between 450–500°C, making them ideal for aerospace engines, rocket components, and other high-temperature applications.
While titanium's low thermal conductivity limits its use in heat dissipation, its superior high-temperature stability compensates, making it a critical choice for environments requiring both strength and heat resistance.
Aluminum: Poor heat resistance.
Aluminum softens at high temperatures, leading to decreased strength and mechanical performance. It is unsuitable for prolonged exposure to high-temperature environments.
In manufacturing, aluminum may suffer from mold sticking and surface defects when processed at elevated temperatures, impacting product quality.
Item | Titanium | Aluminum |
---|---|---|
Thermal conductivity | 17 W/m·K | 210 W/m·K |
Melting point (℃) | 1668°C | 660°C |
Specific heat capacity | 0.52 J/g·K | 0.90 J/g·K |
Coefficient of thermal expansion | 8.6 µm/m·K | 23.1 µm/m·K |
When to choose aluminum or titanium?
Choose Aluminum
For projects where efficient heat dissipation is critical, such as heat sinks, heat exchangers, or cookware.
When high-temperature performance is not a primary concern.
Choose Titanium
For applications requiring materials to maintain strength and stability at high temperatures, such as aerospace engines or industrial equipment.
When heat dissipation needs can be optimized through design or supplemented by other materials.
In terms of thermal conductivity, aluminum outperforms titanium, making it ideal for applications requiring efficient heat transfer. However, titanium’s high-temperature resistance makes it indispensable for environments demanding mechanical stability at elevated temperatures.
By evaluating your project's specific needs—whether for heat dissipation or high-temperature operation—you can make an informed decision between titanium and aluminum to ensure the best performance and functionality for your application.
Electrical conductivity: titanium vs aluminum electrical performance
Electrical conductivity refers to a material's ability to allow the flow of electrons when subjected to a potential difference, making it a key parameter in evaluating a material's suitability for electrical and electronic applications. Below is a detailed comparison of titanium and aluminum based on their electrical conductivity.
Titanium
Electrical conductivity: ~3.1% (relative to copper’s 100%).
Titanium's low electrical conductivity makes it unsuitable for applications requiring high conductivity, such as power cables or electrical wiring.
Despite its poor electrical performance, titanium’s high resistance to corrosion and its mechanical strength provide significant advantages in specialized applications, such as:
- Resistors or components requiring high resistance.
- Environments requiring durable materials resistant to chemical degradation.
Aluminum
Electrical conductivity: ~60% (relative to copper’s 100%).
Aluminum is widely used in electrical and electronic components due to its high conductivity and cost-effectiveness, making it ideal for:
Electrical wiring, where weight reduction is critical (e.g., aircraft and automotive industries).
- Power cables, due to its lightweight and excellent conductivity.
- Electrical connectors and busbars in power distribution systems.
Surface treatment impact:
Aluminum's anodized layer (formed via anodization) is non-conductive, enhancing corrosion resistance and surface hardness for applications requiring both conductivity and durability.
Project | Titanium | Aluminum |
---|---|---|
Conductivity | 3.1% (relative to 100% copper) | 37% (relative to 100% copper) |
Anodic oxidation effect | Uncommon, titanium itself is corrosion resistant | Anodized to form a colorless oxide film, enhancing corrosion resistance |
Applicable areas | Resistors, special electrical applications | Wires, cables, electronic components, radiators, etc. |
Cost | High, requires special equipment and training | Relatively low, but requires precise control of heat input |
Welding difficulty | High, requires strict control of welding environment and parameters | Medium, requires effective heat management to avoid defects |
Machining titanium vs aluminum: workability and formability comparison
In material selection, machinability and formability are critical factors that determine the feasibility and efficiency of using titanium (Ti) or aluminum (Al) in various industries. Understanding their differences in manufacturing processes can help you make more informed material choices for your projects.
Machinability: titanium vs aluminum
Machinability refers to a material's adaptability to machining processes, affecting surface quality, production cost, and efficiency. Titanium and aluminum exhibit significant differences in this regard.
Machining processes
Titanium
- Requires specialized equipment and techniques, including high-rigidity machining systems and effective cooling solutions.
- CNC turning and milling are commonly used but demand precise control to maintain machining accuracy and surface quality.
Aluminum
- Can be machined using standard CNC turning and milling equipment, making it easier to handle.
- Aluminum’s ease of machining enables faster production of high-quality parts, making it ideal for large-scale manufacturing.
Tool wear
Titanium
Its high hardness and strength lead to faster tool wear, requiring impact-resistant cutting tools.
Slower cutting speeds and optimized cutting parameters are necessary to minimize tool wear and extend tool life.
Aluminum
Softer material properties result in slower tool wear, improving tool longevity.
This makes aluminum machining more cost-effective and suitable for mass production.
Surface quality
Titanium
May require additional surface treatments to meet high smoothness and finish requirements.
Aluminum
Naturally achieves better surface finishes due to its lower hardness, reducing friction and improving part quality during machining.
Chip formation
Titanium
Produces short chips that are easier to handle but encounters higher cutting resistance.
Requires low cutting speeds and moderate feed rates to ensure efficient chip management and reduced tool wear.
Aluminum
Generates long, fine chips, enabling efficient heat dissipation and faster cutting speeds.
Allows higher cutting speeds and feed rates, improving machining efficiency.
Formability: titanium vs aluminum
Formability indicates a material's ability to undergo plastic deformation without failure, which is crucial for stamping, bending, drawing, and other forming processes.
Titanium
- Low Ductility:Despite its toughness, titanium’s poor plasticity makes forming processes more challenging.
- Forming Challenges:Requires higher pressure and precise temperature control, limiting the forming of complex geometries.
- Specialized Process Requirements:Often demands specialized equipment and techniques, increasing manufacturing complexity and cost.
Aluminum
- High Ductility:Exhibits excellent ductility, allowing for easy forming of complex shapes.
- Versatile Forming Methods:Supports various processes like stamping, bending, drawing, and extrusion, demonstrating high adaptability.
- Surface Treatment:Can be cut using saws, lasers, plasma, or water jets, enabling high-precision and complex geometries.
- Processing Flexibility:Easy to control during mechanical processing, offering cost-effective and quick forming, particularly suitable for rapid prototyping.
Project | Titanium | Aluminum |
---|---|---|
Formability | Low (poor plasticity, difficult to form) | High (good ductility, easy to form) |
Forming method | Requires high pressure and precise control | Various forming methods such as stamping, bending, stretching, extrusion, etc. |
Surface treatment | Requires professional equipment for surface treatment | Various cutting and surface treatment processes, easy to control |
Processing complexity | Requires professional technology and equipment | Easy to process, suitable for rapid and mass production |
Cost effectiveness | High forming cost, suitable for high precision and high strength applications | Low forming cost, suitable for economical and efficient production and rapid manufacturing |
In general, aluminum excels in machinability and formability, and is suitable for applications that require high efficiency, low cost, and complex forming. Although titanium is more difficult and costly to process, its advantages in high strength and durability make it an ideal choice for high-end applications. According to project requirements, choosing the most suitable material will help optimize the manufacturing process and improve product performance and cost-effectiveness.
Titanium vs Aluminum weldability: a detailed comparison
Weldability refers to a material's ability to be joined through welding while forming high-quality weld seams. Titanium and aluminum exhibit distinct differences in this aspect, which impacts their suitability for various applications.
Aluminum
High weldability: Aluminum has high weldability and can be joined by a variety of welding methods, such as TIG welding, MIG welding, plasma welding, etc.
Application advantages: Widely used in structural parts and components that require welding, such as automotive, aerospace and construction fields.
Processing challenges: The high thermal conductivity of aluminum makes it difficult to control the heat input during welding, which can easily lead to material deformation and weld cracking. Therefore, welding aluminum requires precise thermal control and appropriate welding parameters.
Titanium
Low weldability: Titanium is more difficult to weld than aluminum and requires more specialized techniques and equipment.
Welding methods: Titanium alloys are usually welded by methods such as gas tungsten arc welding (TIG), plasma arc welding and electron beam welding.
Application characteristics: Despite the difficulty of welding, titanium is still widely used in aerospace, medical implants and high-performance sports equipment because its high strength and corrosion resistance are irreplaceable.
Project | Titanium | Aluminum |
---|---|---|
Weldability | Low, requires specialized welding techniques and equipment | High, but high thermal conductivity, prone to deformation and cracking |
Welding method | TIG welding, plasma welding, electron beam welding | TIG welding, MIG welding, plasma welding |
Application area | Aircraft engine parts, medical implants, high-end sports equipment | Automotive, aerospace, construction, consumer electronics |
Cost | High, requires specialized equipment and training | Relatively low, but requires precise control of heat input |
Welding difficulty | High, requires strict control of welding environment and parameters | Medium, requires effective heat management to avoid defects |
Alloy upgrade: titanium alloy vs aluminum alloy
Aluminum alloy family
6061 aluminum alloy: good weldability, balanced comprehensive performance, suitable for general structural parts and frames, such as bicycle frames and building frames.
7075 aluminum alloy: outstanding strength, high tensile strength and good corrosion resistance, often used in high-end needs such as aerospace, racing, etc., is one of the most discussed topics of "7075 aluminum vs titanium".
Other aluminum alloys
- 2xxx series: such as 2024 aluminum alloy, with high strength and good fatigue resistance, suitable for aircraft structural parts.
- 3xxx series: such as 3003 aluminum alloy, with good formability and corrosion resistance, suitable for manufacturing pots and radiators.
- 5xxx series: such as 5052 aluminum alloy, with excellent corrosion resistance and weldability, suitable for marine and automotive applications.
- 6xxx series: such as 6061 aluminum alloy, with good weldability and processability, widely used in construction and machinery manufacturing.
- 2024 aluminum
- 7075 aluminum
- 6061 aluminum
- 6063 aluminum
- 5083 aluminum
- 5052 aluminum
Titanium alloy family
Ti-6Al-4V: The most common α+β type titanium alloy, with excellent balance of strength, toughness and corrosion resistance, is widely used in aerospace engines and medical implants.
Pure titanium (Grade 1–4): Commercially pure titanium grades vary slightly in strength, but all have excellent corrosion resistance and biocompatibility.
β-type titanium alloy: such as Ti-15V-3Cr-3Sn-3Al, has better formability but is more expensive.
Other aluminum alloys
- Grade 2
- Grade 4
- Grade 5
- Grade 6 Ti-5Al-2.5Sn
- Grade 23 Ti-6Al-4V ELI
- Ti-8Al-1Mo-1V
- Ti-6Al-2Sn-4Zr-2Mo
- Ti-6Al-6V-2Sn
- Ti-6Al-2Sn-4Zr-6Mo
Comparison Selection
High strength-low cost: high-strength aluminum alloys (such as 7075, 2024) are preferred.
High strength-high corrosion resistance: titanium alloys (such as Ti-6Al-4V) are irreplaceable.
Extreme environment applications: such as deep sea, ultra-high temperature, strong corrosion, etc., most aluminum alloys will have weak performance, and titanium alloys will perform better.
Cost difference: titanium vs aluminum cost & price
In the material selection process, cost and price are one of the important factors in deciding between titanium and aluminum. Understanding the differences in market prices, processing costs, and overall cost-effectiveness between these two metals can help you make more informed economic decisions on your projects.
Market price comparison
As of this writing, the spot price of titanium is approximately $5.75 per kilogram, while aluminum is trading at approximately $2.20 per kilogram. This price difference is significant, with titanium almost 2.5 times more expensive than aluminum. However, material selection is determined not just by unit price, but also by considering the amount of material required to achieve the same performance in a specific application.
Processing cost and difficulty
In addition to the price of the material itself, processing costs are also an important factor affecting the overall cost:
Titanium
- Difficult to process: Titanium’s high hardness and strength make it more difficult to cut, weld and form, which increases tool wear and manufacturing costs.
- Professional operation requirements: Grinding, bending and welding titanium require extremely high professional skills and equipment, further driving up processing costs.
- High manufacturing waste costs: Scrap generated during titanium processing is more expensive, so manufacturers often use aluminum for initial prototyping before switching to titanium for final production.
Aluminum
- Easy to process: Aluminum is softer, so cutting tools wear more slowly, extending tool life and reducing processing costs.
- High-efficiency production: Aluminum’s easy processing makes it suitable for mass production and can quickly manufacture high-quality parts, improving production efficiency and cost-effectiveness.
- Low manufacturing waste costs: Aluminum has a low processing waste cost, which is suitable for cost-effective production processes.
Cost-benefit analysis
Titanium: Titanium has high material and processing costs, but its excellent performance can provide longer service life and reduce maintenance and replacement costs in applications that require high strength, corrosion resistance and high temperature resistance. In high-end applications such as aerospace and medical implants, titanium's high return on investment (ROI) makes it a worthwhile choice.
Aluminum: Aluminum has low material and processing costs, suitable for large-scale, cost-effective production needs. In applications that require lightweight and good thermal conductivity, aluminum provides a cost-effective solution.
Comparison dimensions | Titanium | Aluminum |
---|---|---|
Material unit price | High (about $5.75/kg) | Low (about $2.2/kg) |
Processing difficulty | High (cutting, welding, forming require specialized skills) | Low (easy to cut and weld, suitable for mass production) |
Manufacturing cost | High (tool wears quickly, special processing equipment) | Low (slow tool wear, high processing efficiency) |
Manufacturing waste cost | High (high scrap value) | Low (low scrap cost) |
Life cycle maintenance cost | Low (corrosion resistance, long service life) | Medium (highly corrosive environment requires more maintenance or surface treatment) |
Total cost | High (high initial cost, but low long-term maintenance) | Low (low initial cost, but may require more frequent maintenance) |
Comprehensive cost-effectiveness
Titanium: If the project has extremely high requirements for strength, corrosion resistance and high temperature performance, and the budget is sufficient, titanium is very suitable. High initial investment may have a higher ROI (return on investment) in long-term use.
Aluminum: If the demand focuses more on "aluminum vs titanium cost" and large-scale production, aluminum is often a more economical choice. Suitable for large-scale, low-cost production needs.
Summary and material selection recommendations
Through the in-depth discussion of this article, you have fully understood the performance of titanium and aluminum in key performance indicators such as weight, strength and hardness, corrosion resistance, thermal conductivity and heat resistance, machinability and formability, weldability, and cost and price. Understanding their best use in different application scenarios will help you make more informed decisions in project material selection.
- High strength requirements: Choose titanium, such as aircraft engine components and medical implants.
- Efficient heat dissipation: Choose aluminum, such as consumer electronic devices and radiators.
- Economical and efficient production: Choose aluminum, suitable for large-scale industrial production.
- High corrosion resistance: Choose titanium, suitable for marine engineering and chemical equipment.
Whether you are an engineer, a purchaser, or a DIY enthusiast, titanium and aluminum can provide you with the best material solutions. Read now to optimize your material selection strategy and achieve the perfect balance between performance and cost!
Contact us for more support
If you are evaluating the applicability of titanium and aluminum in your project, or need more detailed material selection and performance comparison data, please [Contact us]. Our team of experts will provide you with professional material selection support and solutions to help your project succeed.