Titanium in Marine Applications
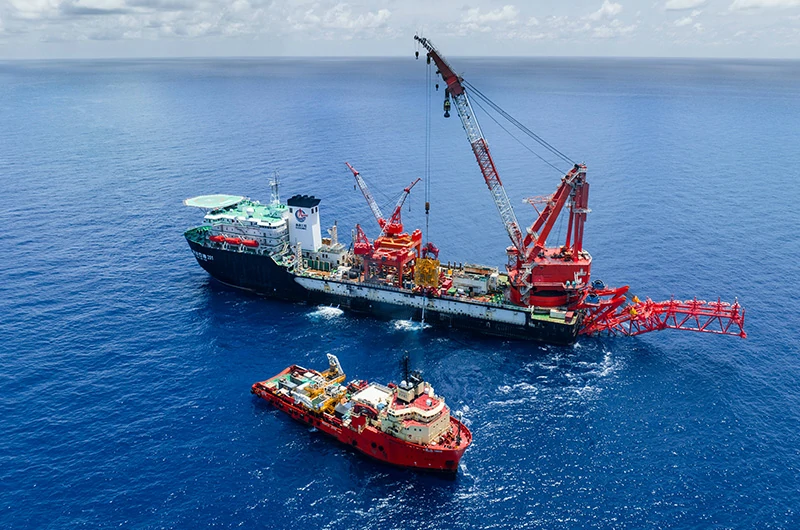
Marine engineering continuously faces harsh challenges of high salinity, high pressure, and severe corrosion. Traditional materials like steel and copper alloys suffer from short service lives, high maintenance costs, and rapid performance degradation in seawater—steel pipelines can fail from corrosion within 5 years, and copper-nickel alloy heat exchangers last less than 8 years in high-temperature seawater, leading to over $50 billion in annual global losses. With its zero corrosion loss, over 30 years of service life, and breakthrough lightweight high-strength performance, titanium is the ideal choice to meet these challenges.
Titanium's irreplaceability stems from three core features:
- Corrosion Resistance: The passivation film on titanium in seawater can withstand up to 100,000 ppm chloride ions, 100 ppm hydrogen sulfide, and 80℃ high-temperature seawater, with a corrosion rate of <0.001 mm/year.
- Lightweight: Its density is only 57% of steel, and with a strength-to-weight ratio of 22, structural weight can be reduced by 30%-40%.
- Life Cycle Economy: Although the initial cost is 3-5 times that of stainless steel, its 30-year maintenance-free design reduces overall costs by 45%.
From deep-sea oil and gas fields to offshore wind platforms, from polar research equipment to military deep-diving vehicles, titanium is reshaping the material system of marine engineering through technological innovation and upgraded standards. These breakthroughs not only impact economic efficiency but also underpin national marine strategic capabilities.
The segmented applications of titanium in the marine field include:
- Sea Water Cooling Systems
- Sea Water Desalination Devices
- Deep-Sea Oil and Gas Development
- Shipbuilding
- Nuclear Submarines
- Marine Scientific Research and Detection Equipment
- Marine Wind Power Generation
- Marine Electronic and Acoustic Equipment
Sea Water Cooling Systems
Sea water cooling systems are widely used in ships, offshore platforms, and nuclear power plants. They maintain equipment operating temperatures by exchanging heat between seawater and the coolant.
Due to seawater's high corrosion, salinity, and microbial pollution, these systems demand materials with excellent corrosion resistance, high strength, and long-term stability. The core advantages of titanium include:
- Corrosion Resistance: With abundant chloride ions in seawater, materials must exhibit exceptional anti-corrosion capabilities.
- Strength and Stability: Systems must withstand high pressure, requiring high strength and long-term stability.
- Cost and Maintenance: Although titanium has a higher initial cost, its lower long-term maintenance and replacement expenses make it the ideal choice.
Thanks to its outstanding resistance to seawater corrosion, high strength-to-weight ratio, and long service life, titanium is the optimal material for sea water cooling systems.
Chalco Product Categories
Standard:ASTM B338,ASTM B861,ASTM B862,ASTM B367,ASTM B265,ASTM B462,ASTM B363,ASTM B381,ASTM B363,ASTM B462,ASTM B381,ASTM F467,ASTM F468
-
Seamless Titanium Tube
Alloy: Gr2, Gr5, Gr12
Commonly used in high-pressure heat exchanger pipelines, seawater cooling pipelines, and nuclear power plant condenser cooling tubes.
-
Welded Titanium Tube
Alloy: Gr7 (Ti-0.2Pd)
Commonly used in low-pressure seawater circulation pipelines, offshore platform fire systems, and open-circuit cooling systems for ships.
-
Titanium Tube Plate
Alloy: Gr2, Gr16(Ti-0.05Pd)
Secures titanium tubes in heat exchangers, forming tube bundle assemblies. Commonly used in multi-effect distillation (MED) tube bundle support plates.
-
Titanium Flange
Alloy: Gr5
Connects pipelines and links equipment and pipes, commonly applied in directional connections for cooling pipelines.
-
Titanium Tube Fittings
Alloy: Alloy: Gr2, Gr5
Includes titanium elbows, tees, flanges, etc., responsible for pipeline connections and fluid guidance.
-
Titanium Fasteners
Alloy: Gr5, Titanium-Copper Composite
Used to secure cooling system components, commonly applied in hull connections and deep-sea equipment assemblies.
Sea Water Cooling Systems: How Do Titanium Tubes Solve High Salt Corrosion and Cost Challenges?
In 80℃ high-temperature seawater, copper-nickel alloy heat exchangers last less than 8 years, whereas titanium tubes—with zero corrosion loss and a 30-year maintenance-free design—have become the top upgrade choice for ship and nuclear power cooling systems.
Titanium vs. Copper-Nickel Alloy Performance Comparison
Performance Indicator | Copper-Nickel Alloy | Titanium Alloy (Gr2) | Advantage Improvement |
---|---|---|---|
Corrosion Rate | 0.05 mm/year | 0.001 mm/year | Decrease 98% |
Service Life | 5-8 years | 25-30 years | Increase 300% |
Total 30-Year Cost | 120million RMB | 650,000 RMB | Save 46% |
How to Choose Titanium Tubes for Sea Water Cooling Systems? (By Scenario)
- Low-Pressure Circulation Systems: Gr2 Welded Titanium Tube (ASTM B862) offers low cost with adequate corrosion resistance.
- Nuclear Power Plant Condensers: Gr5 Seamless Titanium Tube (ASTM B338) with a pressure rating ≥20 MPa.
- Sulfur-Containing Environments: Gr7 Titanium Tube (containing 0.2% Pd) is resistant to H₂S concentrations >100 ppm.
Specific Application Case of Sea Water Cooling Systems
Saudi Jubail Sea Water Desalination Plant: Utilizes Gr2 Titanium Tube (ASTM B338) operating at 110℃, with a service life of 30 years, and achieves maintenance costs 60% lower than those of copper alloys.
Seawater Desalination Equipment
Titanium is widely used in Seawater Desalination Equipment due to its excellent resistance to High Temperature and Corrosion. Its applications include Structural Components, Heat Exchanger Housing, Baffles, Membrane Modules, Multi-Stage Flash (MSF) Heat Exchanger Tube Bundles, and Low-Temperature Multi-Effect Distillation (MED) Evaporator Tube Bundles.
Electrolytic Anti-Fouling and Laser Welding technologies further enhance the equipment's heat exchange efficiency and durability. Although the initial cost is relatively high, a service life exceeding 25 Years significantly reduces maintenance frequency, achieving a Full Lifecycle Cost Advantage.
Titanium Products from Chalco
-
Titanium Plates
Gr1, Gr2, Gr12
Structural components, heat exchanger shells, baffles, membrane modules.
ASTM B265 -
Seamless Titanium Tubes
Gr2, Gr7
Wall Thickness: 0.5-3mm, used in MSF evaporator heat exchanger tube bundles.
ASTM B338 ASTM B861 -
Welded Titanium Tubes
Gr1, Gr16
Applications: MED evaporator tube bundles.
ASTM B338 ASTM B861 -
Titanium Tube Sheets
Gr5
Application: Heat exchanger tube fixing structures, thickness 50-100mm, ensuring strong tube bundle support.
ASTM B367 ASTM B265 -
Titanium Pipe Fittings
Gr1, Gr2, Gr12
Titanium pipe connections for high-temperature seawater pipelines (Sch40-Sch160).
ASTM B363 ASTM B462 ASTM B381
How to Choose Titanium Tubes for Seawater Desalination Equipment (By Application)
- Multi-Effect Distillation (MED): Use Gr16 Titanium Welded Tube (ASTM B862), which resists chloride ion concentrations up to 40,000 ppm.
- Multi-Stage Flash (MSF): Use Gr2 Seamless Titanium Tube (ASTM B338) with a 1.2mm wall thickness and pressure resistance of ≥2.5MPa.
- Sulfur-Containing Environment: Use Gr7 Titanium Tube (containing 0.2% Palladium), capable of withstanding H₂S concentrations >100ppm.
Application Cases
Saudi Jubail Seawater Desalination Plant: Utilizes Gr2 Titanium Tubes (ASTM B338) with a tube diameter of 25mm × 1.2mm wall thickness, operating at 110°C and a design lifespan of 30 years.
Tianjin, China Seawater Desalination Project: Employs domestic Gr16 Titanium Welded Tubes (GB/T 26057), with a daily capacity of 100,000 tons and resistance to chloride ions up to 40,000ppm.
Deep Sea Oil and Gas Development
Deep Sea Oil and Gas Development on Offshore Platforms, Subsea Pipelines, and Underwater Production Systems requires equipment materials to withstand extreme conditions such as high pressure, low temperatures, high salinity, and strong ocean currents. Therefore, the materials must possess outstanding corrosion resistance, fatigue resistance, and high strength.
Titanium is widely used because it effectively prevents crevice corrosion and galvanic corrosion induced by pressures above 30MPa, while offering a lightweight advantage with twice the specific strength of steel. In addition, it exhibits excellent performance against sulfide stress corrosion cracking, thereby significantly enhancing the long-term reliability and safety of deep sea equipment.
Titanium Products Provided by Chalco
-
Titanium-Steel Transition Fittings Gr29
Commonly used in deep-sea drilling tools for oil and gas exploration.
ASTM B898 ASTM B861 -
Titanium-Steel Explosive Composite Tube Gr5+ X65 Steel
Offers 1.5 times the pressure resistance of conventional tubes.
-
Seamless Titanium Tubes Gr5, Gr9, Gr12
The seamless design reduces maintenance and leakage risks.
ASTM B338 ASTM B861 -
Titanium Plates Gr5, Gr12
Used in pressure vessels such as separators, storage tanks, and reactors.
ASTM B265 -
Titanium Fasteners Gr5
Includes bolts, nuts, and gaskets for high-pressure, high-load connections.
ASTM F467 ASTM F468 -
Titanium Alloy Valves Gr12
Used in oil and gas transport, injection, and control systems.
ASTM B367 ASTM B348
Titanium vs. Steel Comparison
Performance Indicator | X65 Steel | Gr5 Titanium Alloy | Advantage Improvement |
---|---|---|---|
Specific Strength (Strength/Density) | 18 | 22 | Increase 22% |
Chloride (Cl) Corrosion Rate | 0.5 mm/year | 0.001 mm/year | Decrease 99.8% |
Maximum Operating Depth | 1500 meters | 3000 meters | Expand 100% |
Scenario-Based Material Selection for Deep Sea Oil and Gas Development
- Drill Pipe Joints: Use Gr29 Titanium Alloy (with 0.1% Ruthenium) to boost crevice corrosion resistance by 50%.
- Composite Risers: Employ Titanium-Steel Explosive Composite Tubes (ASTM B898) with an interfacial shear strength of ≥210MPa.
- Valve Systems: Utilize Gr12 Titanium Alloy (Ti-0.3Mo-0.8Ni), which has passed the NACE TM0177 Hydrogen Sulfide Test.
Application Case
In a deep-sea oil well project in the Gulf of Mexico, the use of titanium-steel explosive composite risers extended the service life to 25 years (compared to 8 years for conventional steel risers).
Importance of Shipbuilding Materials
Ships constantly exposed to seawater require corrosion-resistant, strong, and lightweight materials. Titanium, with twice the specific strength of steel and superior fatigue resistance, extends component lifespan, cuts maintenance costs, and reduces ship weight, enhancing speed and payload. Its self-lubricating, high-torque resistance ensures stable propulsion, while its corrosion resistance prevents galvanic reactions, boosting long-term reliability.
Titanium Products Available from Chalco
Standard:ASTM B265, ASTM B338, ASTM B861, ASTM B338, ASTM B861, ASTM B338, ASTM B861, ASTM B338, ASTM B861
-
Titanium PlatesGr5, Gr7
Used in hull outer plates, decks, bulkheads, superstructures, helicopter platforms
-
Titanium TubesGr2, Gr4, Gr9
Applied in seawater piping systems (cooling, ballast, firefighting), hydraulic systems, exhaust pipes
-
Titanium ProfilesGr5, Gr9
Used in hull structural beams, ribs, stringers for weight reduction.
-
Titanium CastingsGr5, Gr7, Gr9
Applied in propellers, pump bodies, valve bodies, rudder blades
-
Titanium FastenersGr5, Gr5 + Copper Coating
Used for hull structure connections, equipment mounting, and piping connections
Titanium vs. 316 Stainless Steel
Property | 316 Stainless Steel | Gr5 Titanium Alloy | Advantage |
---|---|---|---|
Density (g/cm3) | 8 | 4.5 | 44% Reduction |
Salt Spray Test Lifespan | 3 Years | 30 Years | 900% Longer Lifespan |
Maintenance Frequency | Annually | None Required | 100% Cost Reduction |
Application-Specific Material Selection in Shipbuilding
- Hull Structure: Gr5 Titanium Plates (GB/T 3621), 10-50mm thickness
- Propulsion System: Gr9 Titanium Forgings (ASTM B381), torsional strength ≥ 620MPa
- Piping Connections: Titanium-Copper Composite Bolts (ASTM F467) for galvanic corrosion resistance
Nuclear Submarines
Nuclear Submarines are powered by nuclear reactors and possess extended underwater endurance, high stealth, and formidable strike capabilities. Operating in extreme marine environments, they face challenges such as high deep-sea pressure, seawater corrosion, nuclear radiation, and high temperature and humidity. Their design and material selection require exceptional strength, corrosion resistance, and fatigue resistance, ensuring long-term stable operation under stringent safety, longevity, and reliability requirements.
Titanium is a core material in nuclear submarines, primarily used in pressure hulls, propulsion systems, piping systems, and acoustic devices. Its advantages include:
- Lightweight: Titanium has a density only 57% that of steel, substantially reducing submarine weight and enhancing speed and maneuverability (e.g., Russia's Alpha-class Nuclear Submarine achieves up to 42 knots underwater).
- Deep Dive Capability: Titanium alloy pressure hulls can withstand deep-sea pressures exceeding 900 meters (Russia's M-class Nuclear Submarine has a dive depth of up to 1250 meters).
- Non-Magnetic: Eliminates detection by magnetic sensors, enhancing stealth.
- Corrosion Resistance: Resistant to seawater, chloride ions, and microbial corrosion, with a service life over 30 years—five times longer than copper alloy piping.
- Radiation Resistance: Titanium's resistance to radiation makes it an ideal choice in nuclear submarines where the reactor produces ionizing radiation.
Titanium Products Available from Chalco
-
Titanium Plates Gr5, Gr23
Used in pressure structure materials, submarine hulls, and pressure vessels.
ASTM B265 ASTM B348 -
Titanium Tubes Gr2, Gr4, Gr5, Gr23
Utilized in nuclear propulsion system piping, seawater systems, hydraulic...
ASTM B338 ASTM B861 -
Titanium Pipe Fittings Gr2, Gr5, Gr12
Employed for fixing and connecting internal components and external structures.
ASTM B363 ASTM B462 ASTM B381 -
Titanium Bars Ti-6Al-2Nb-1Ta-0.8Mo
Titanium resists cavitation and erosion, lasting over five times longer than copper.
ASTM B348 ASTM B381 -
Titanium Fasteners Gr5
Connect and secure various submarine components, ensuring structural strength.
ASTM F467 ASTM F468
Nuclear Submarines: How Do Titanium Alloys Achieve a 900-Meter Dive Depth and Full Lifecycle Stealth?
Pressure Hull Enhancement: By employing an ultra-low interstice element (ELI) design, titanium pressure hulls extend the dive depth from 500 meters (typical for steel hulls) to 900 meters, evading magnetic sensor detection.
Deep-Sea Alloy Gr23 (Ti-6Al-4V ELI)
- Oxygen content ≤ 0.13%, with fracture toughness (KIC) ≥ 120 MPa√m;
- Yield strength ≥ 825 MPa, passing hydrostatic tests at 110 MPa;
- Non-magnetic (magnetic permeability ≤ 1.00005), enhancing stealth by 70%.
Application Cases
Russia's Alpha-Class Nuclear Submarine: Utilizes Gr23 and Gr9 Titanium Alloys, achieving a dive depth of 914 meters, a speed of 42 knots, and a service life of 40 years, with each submarine using 3000 tons of titanium alloy.
Russia's Typhoon-Class Nuclear Submarine: Employs a Ti-6Al-2Nb-1Ta-0.8Mo pressure hull and Ti-6Al-4V propellers, with a dive depth of 500 meters (maximum 1830 meters), a displacement of 33,800 tons, and 9000 tons of titanium alloy per vessel.
China's Jiaolong Manned Submersible: Uses a TC4ELI Titanium Alloy pressure hull, capable of diving to 7062 meters, with a hull thickness of 80mm and a compressive strength of 1100 MPa.
Marine Scientific Research and Exploration Equipment
Marine Scientific Research and Exploration Equipment is widely used in ocean environment monitoring, hydrological surveys, biological research, geological exploration, and other fields. It encompasses devices such as underwater sensors, hydrophones, samplers, deep-sea landers, and drifting buoys.
Exploration equipment often operates in deep-sea and extreme environments, facing severe challenges like intense seawater corrosion, high pressure, and low temperatures. In long-term underwater missions, these devices must not only combat corrosion and fouling but also maintain data accuracy and reliable transmission to ensure stable and dependable research results.
Titanium alloys, thanks to their high strength, corrosion resistance, and non-magnetic properties, play a critical role in key components, such as:
- Deep-sea Submersible Pressure Hulls: Capable of withstanding water pressures at 6000-meter depths (approximately 60 MPa), reducing weight by over 40% compared to traditional steel.
- Sensor and Electronic Equipment Casings: Titanium's low magnetism and acoustic compatibility improve data collection accuracy (e.g., reducing sonar signal interference by 30%).
- Underwater Robot (ROV/AUV) Frames: Lightweight designs extend endurance and adapt to complex seafloor operations.
Titanium Products Available from Chalco
-
Titanium Pressure Housings
Gr5, Gr7
Used for sensor and detector casings, protecting hydrophones and detectors from seawater corrosion.
ASTM B265 ASTM B348 -
Titanium Frames
Gr5, Gr9
Supports and secures components such as sensors, instruments, and samplers.
ASTM B348 -
Titanium Composite Robotic Arms
Gr9, Gr5+Steel Mechanical Arms
Primary components for deep-sea sampling robotic arms.
ASTM B265 ASTM B348 -
Titanium Fasteners
Gr5, Gr23
Bolts, nuts, gaskets, etc., used for fixing and connecting research equipment.
ASTM F467 ASTM F468
Titanium vs. Aluminum Alloy
Property | Aluminum Alloy | Gr5 Titanium Alloy | Advantage |
---|---|---|---|
Pressure Resistance | 3000 meters | 11000 meters | Increase 267% |
Biofouling Rate | 0.3 | 0.05 | Decrease 83% |
Signal Interference | High | None | Data Accuracy +80% |
Scenario-Based Material Selection for Marine Scientific Research and Exploration Equipment
- Pressure Housings: Use Gr23 Titanium Alloy (with KIC ≥ 120 MPa√m) to support full-ocean-depth exploration.
- Robotic Arms: Use Gr9 Titanium Forgings (with Fatigue Strength Δσ = 300 MPa) for a load capacity of 200 kg.
- Sensor Casings: Employ Gr2 Titanium Precision Casting (with a tolerance of ±0.1mm) for optimal accuracy.
Application Cases
Japan's "Shinkai 6500” Manned Submersible: Utilizes a Gr23 Titanium Alloy pressure hull (80mm thickness, dive depth of 6500 meters) with a yield strength ≥825 MPa and a service life of 40 years, achieving up to 35% weight reduction compared to steel.
USA's "Orpheus” Deep-Sea Explorer: Employs a Gr5 Titanium Alloy robotic arm with a load capacity of 200 kg and pressure resistance of 100 MPa; its fatigue strength is Δσ = 300 MPa (tested over 10⁷ cycles), making it suitable for Mariana Trench exploration.
Offshore Wind Power
Offshore wind power harnesses wind energy by deploying wind turbines at sea. These wind turbines can be either fixed-bottom or floating, playing a crucial role in offshore energy development.
Due to the harsh marine environment, offshore wind platforms must withstand prolonged exposure to strong winds, waves, seawater corrosion, and salt spray, requiring high corrosion resistance, strength, lightweight properties, and fatigue resistance. Titanium materials, known for their lightweight, high strength, and superior corrosion resistance, offer key advantages in the following critical components:
- Anchors and Bases: Floating platforms endure ocean currents and dynamic loads. Titanium alloys reduce weight by over 30% and extend lifespan up to 30 years.
- Towers and Support Structures: Titanium composites (Titanium-Steel / Titanium-Carbon Fiber) enhance fatigue resistance, adapting to deep-sea high-pressure environments.
- Cooling Systems and Connectors: Titanium tubes are used in generator cooling circuits, withstanding high-temperature seawater corrosion; titanium bolts ensure salt spray-resistant fastening.
Chalco's Titanium Products for Offshore Wind Power
-
Titanium Plates
Alloy: Gr5, Gr7
Used in titanium wind turbine blades, titanium towers, and other wind power components.
-
Titanium-Steel Explosive Clad Pipess
Alloy: Gr5 (Outer) + X65 Steel (Inner)
Used in internal support structures (pipes) and floating platform transition structures.
-
Titanium Tubes
Alloy: Gr2
Applied in generator seawater cooling circuits, resisting 80°C high-temperature seawater corrosion.
-
Titanium Fastenerss
Alloy: Gr5
Used for connecting wind turbine components, including blades to hubs, nacelles to towers, and tower sections.
Marine Electronics & Acoustics
Marine electronics and acoustics are widely used in underwater communication, target detection, and environmental monitoring, covering devices such as sonar systems, navigation equipment, hydrophones, and underwater cameras. These devices must operate reliably in harsh ocean conditions, facing challenges like seawater corrosion, high pressure, low temperatures, and strong vibrations.
In deep-sea environments, ensuring accurate and stable signal transmission is critical while also preventing corrosion, fouling, and biofouling, which guarantees long-term reliability and high performance. Key advantages include:
- Non-Magnetic Properties: Eliminates electromagnetic interference, improving acoustic signal accuracy (e.g., sonar positioning error reduced by 15%).
- Superior Corrosion Resistance: Withstands seawater, chloride ions, and microbial corrosion, extending equipment lifespan to over 20 years (compared to aluminum alloys' 5–8 years).
- Low Acoustic Impedance (27×10⁶ kg/m²s): Enhances sound wave transmission efficiency and reduces signal attenuation.
Chalco's Titanium Products for Marine Electronics & Acoustics
-
Titanium Plates
Alloy:Gr2, Gr9
Used in underwater sensors, communication devices, and sonar system housings to prevent seawater corrosion and pressure damage.
ASTM B265 ASTM B348 -
Titanium Forgings
Alloy:Gr5 (Outer) + X65 Steel (Inner)
Used in sonar fairings, capable of withstanding 50MPa pressure, suitable for deep-sea synthetic aperture sonar (SAS).
ASTM B341 -
Titanium Tubes
Alloy:Gr2
Used in underwater communication equipment pipelines, ensuring signal transmission stability.
ASTM B338 ASTM B861 -
Titanium Fasteners
Alloy:Gr5
Used to secure electronic and acoustic equipment components, ensuring sealing integrity and structural strength.
ASTM F467 ASTM F468
Application Case Study
China's "Jiaolong" deep-sea manned submersible utilizes a Gr5 titanium sonar fairing, capable of withstanding 100MPa pressure, optimizing acoustic impedance by 30%, and supporting 7,000-meter deep-sea exploration.
Chalco Titanium's Featured Products in the Marine Field
Titanium Tube Sheet
Titanium Tube Sheet, a perforated plate in heat exchangers, secures tubes and separates media. Precision-rolled and CNC-drilled, it withstands high-temperature, high-pressure marine environments, serving as a core load-bearing component in heat exchangers and condensers.
Contact us now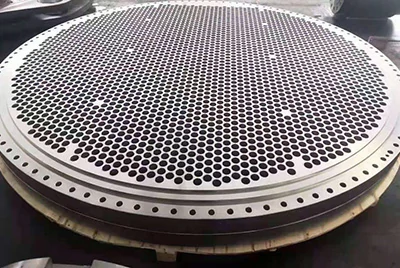
Grades: Gr2, Gr7, Gr12, Gr16
Standard: ASTM B265
Applications:
- Seawater Desalination: Multi-Stage Flash (MSF) and Multi-Effect Distillation (MED) systems
- Ocean Thermal Energy Conversion (OTEC): Plate heat exchanger pressure-support structures
Titanium-Steel Clad Plate
Titanium-Steel Clad Plate produced by Chalco Titanium uses explosive welding to bond a titanium layer (for corrosion resistance) with a steel layer (for high strength), addressing both corrosion and load-bearing challenges in marine engineering.
Contact us now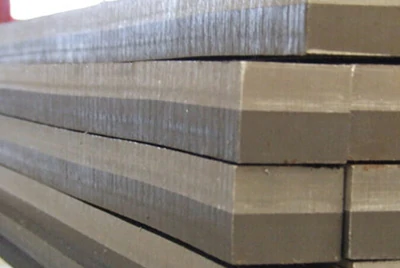
Material: Gr2 Titanium Layer + Q355 Steel Layer
Standard: ASTM B898
Applications:
- Ship Hull Splash Zone: Resists wave impact and salt spray corrosion
- Marine Platform Transition Structures: Connects titanium piping with steel platforms to prevent galvanic corrosion
Titanium-Steel Transition Joint
Developed exclusively by Chalco Titanium, the Titanium-Steel Transition Joint employs dissimilar metal welding technology to solve galvanic corrosion issues, suitable for deep-sea equipment and marine power systems.
Contact us now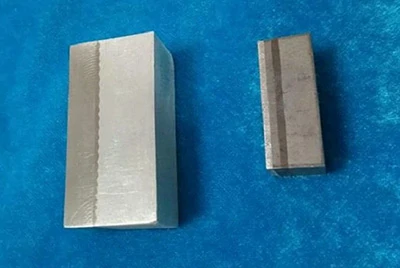
A Titanium-Steel Transition Joint is used to connect titanium and steel in a single assembly, typically achieved via explosive welding or similar methods. One side is titanium, the other steel, with a dense metallurgical bonding layer in between for a seamless transition.
Material: Gr5 + Q355 Steel
Standard: ASTM B898
Applications:
- Offshore Oil & Gas Platforms: Flange connections between titanium tubing and carbon steel risers
- Ship Propulsion Systems: Transition segments from titanium shafts to steel hulls
Titanium-Steel Explosive Clad Pipe
With a titanium inner layer (for corrosion resistance) and a steel outer layer (for pressure endurance), Titanium-Steel Explosive Clad Pipe balances performance and cost, overcoming deep-sea high-pressure pipeline barriers.
Contact us now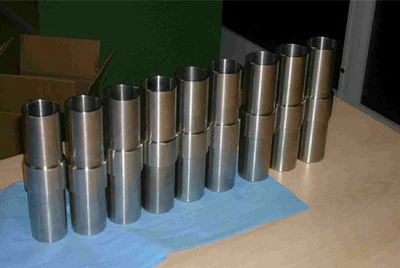
Material: Gr2 (Gr7, Gr12) Titanium Layer + X65 Steel Layer
Standard: ASTM B898
Applications:
- Seawater Desalination: High-pressure brine discharge pipelines
- Deep-Sea Oil & Gas Transportation: 3000-meter subsea pipelines
- Seawater Cooling Systems: Nuclear submarine condenser composite piping
Titanium Forgings
Using precision forging processes (open-die or die forging), Chalco Titanium produces high-strength titanium alloy components suited for deep-sea high-pressure and high-stress scenarios.
Contact us now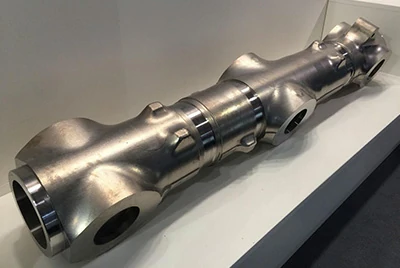
Grades: Gr5, Gr23
Standard: ASTM B381
Applications:
- Ship Propulsion Shaft: Gr5 Titanium Alloy forging with torsional strength ≥ 620 MPa
- Deep-Sea Valve Bodies: Gr23 Titanium Alloy die-forged, rated at 50 MPa
Titanium Pressure Hull
A Titanium Pressure Hull is a sealed structure made from high-strength titanium alloy to withstand significant external pressures, such as manned compartments in deep-sea submersibles, submarine hulls, and underwater pressure vessels.
Contact us now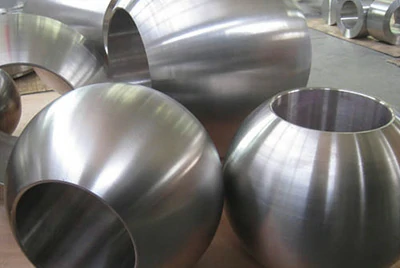
Chalco Titanium employs superplastic forming + electron beam welding to produce large-scale deep-sea pressure chambers for manned and unmanned submersibles. Titanium alloy is the ideal material for deep-sea pressure hulls due to its excellent strength-to-weight ratio and fatigue resistance.
Grades: Gr5, Gr23
Certification: ABS (American Bureau of Shipping)
Applications:
- Military Submarines: Nuclear-powered submarine pressure hull sections
- Scientific Research Submersibles: 7000-meter manned compartments (e.g., "Jiaolong”)
*The "Jiaolong” manned submersible uses TC4ELI Titanium Alloy with an 80 mm hull thickness, tested at 110 MPa hydrostatic pressure for a 7062-meter dive, reducing weight by 40% compared to steel.
Titanium-Copper Composite Fasteners
Titanium-Copper Composite Fasteners combine the benefits of titanium alloy and copper, often seen as bimetallic bolts or studs. The titanium base + copper plating design ensures both conductivity and corrosion resistance, solving grounding and anti-corrosion needs for marine electronics.
Contact us now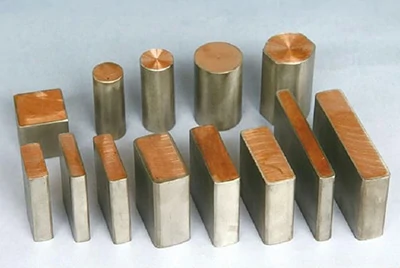
Material: Gr5 Titanium + T2 Copper Coating
Standard: ASTM F467
Applications:
- Sonar Systems: Towed array sonar grounding bolts
- Floating Platforms: Sensor bracket lightning protection connectors
- Oil Platforms: Anti-corrosion grounding systems
Titanium Alloy Propeller
A Titanium Alloy Propeller is a marine propeller made from high-strength, corrosion-resistant titanium alloy. Compared to traditional bronze or stainless steel propellers, titanium propellers feature higher strength, lighter weight, and superior resistance to corrosion and cavitation.
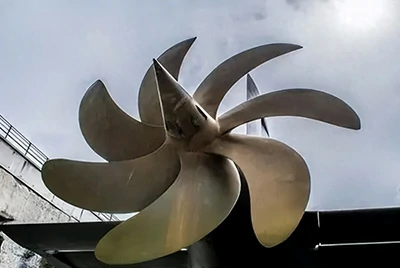
Titanium Anode
A Titanium Anode usually refers to a titanium-based anode coated with a catalytic active layer for cathodic protection or electrolytic oxygen/chlorine generation in marine environments. The base uses pure titanium plates, tubes, or meshes. Even under anodic polarization, titanium forms a stable oxide film, providing excellent corrosion resistance.
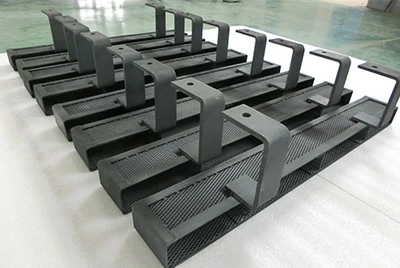
- Cathodic Protection Anode: Titanium-Based Mixed Metal Oxide (MMO) Anode for ship and platform anti-corrosion
- Electrolytic Anti-Fouling System: Titanium Anode generates sodium hypochlorite from seawater to inhibit biofouling
Titanium Heat Exchanger Tube
Used in equipment like seawater condensers and evaporators, generally made of pure titanium with excellent resistance to seawater corrosion and scaling.
Grades: Gr1, Gr2, Gr12
Standard: ASTM B338
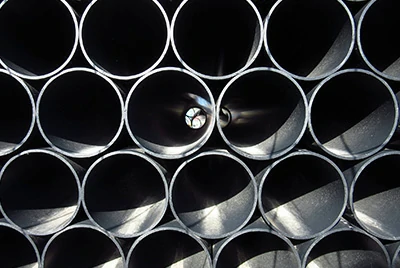
Titanium Sonar Fairing
A precision-cast titanium alloy sonar fairing reduces turbulence noise and improves the signal-to-noise ratio of sonar systems.
Grade: Gr5
Applications: Military Submarines, Marine Research Vessels
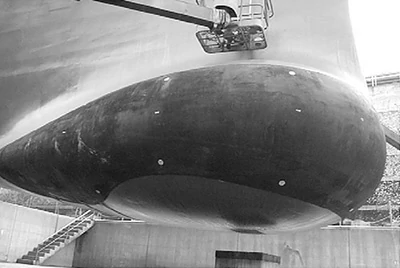
Titanium Wire Woven Anti-Fouling Net
(φ0.5 mm) woven mesh inhibit barnacle and other marine organism attachment, replacing copper-based anti-fouling paints.
Applications: Aquaculture Net Cages, Ship Inlet Filters
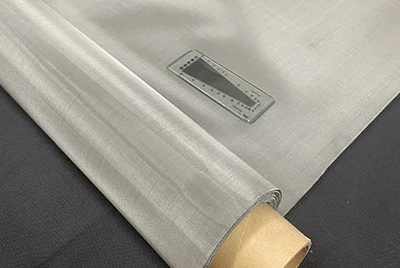
Why Choose Chalco Titanium as Your Supplier?
Robust Production Capability, Ensuring High-Quality Supply
- Complete Supply Chain: From melting to forming, the entire process is self-controlled to guarantee material purity and stability.
- High-Purity Titanium: Advanced melting technology is used, achieving an oxygen content ≤0.15%, which meets the deep-sea pressure resistance requirements.
- Large-Scale Manufacturing: With a maximum single titanium ingot weight of 15 tons, it can meet the demands for large structural components in ships and offshore platforms. We supply Titanium Plates with widths over 3 meters (thickness 5-100mm) and extruded large-diameter titanium tubes (outer diameter ≤600mm) suitable for seawater cooling and oil/gas transportation pipelines.
Precision Processing to Meet Complex Requirements
- Surface Treatment: We offer acid washing, sandblasting, and micro-arc oxidation, among other surface strengthening processes to reduce seawater erosion and biofouling. Additionally, anti-fouling coatings or mixed metal oxide (MMO) coatings can be applied as needed.
- High-Precision Cutting: Utilizing waterjet, laser, and other precision cutting technologies, we accurately process complex components.
- Welding Technology: Electron beam welding, TIG welding, and other methods ensure high-strength, durable weld joints.
- Forming Processes: Techniques such as superplastic forming and spinning are employed to manufacture high-precision structural components.
Compliance with International Standards, Adapting to the Global Market
- International Standards: Our products comply with ASTM, GB, ABS, NACE, and other standards, meeting the stringent requirements of marine engineering.
- Classification Society Certification: Products are certified by multiple authoritative classification societies to ensure project compliance and reduce customer certification costs.
- Testing Methods: We strictly control material and component quality by combining non-destructive tests such as UT (Ultrasonic Testing), RT (Radiographic Testing), PT (Penetrant Testing), along with salt spray and pressure simulation tests to ensure long-term reliability in deep-sea or high-salinity environments.
Stable Supply Chain and Efficient Delivery
- Full Range Titanium Supply: We offer a complete range from titanium ingots and Titanium Plates to titanium tubes, and we support custom specifications to reduce supply chain complexity.
- Efficient Delivery: Streamlined production management significantly shortens delivery cycles to meet urgent project deadlines.
- Professional Technical Support: We provide expertise in material selection and process optimization to help drive projects forward efficiently.
Customer Support and After-Sales Guarantee
- Technical Consultation and Design Solutions: Professional advice on material selection, structural design, and welding processes is provided for various marine applications to ensure project efficiency.
- Remote Assistance: Remote technical support can be arranged for installation, welding, or inspection, helping customers reduce trial-and-error costs.
- Rapid Response and Spare Parts: Our customer service channels respond quickly to any product quality or process issues. We stock common titanium materials and accessories to support ongoing maintenance or upgrades.
FAQ
Why Is the Initial Cost of Titanium Higher Than Stainless Steel? Will It Really Save Money Long Term?
Although titanium's unit price is approximately 3–5 times higher than stainless steel, its 30-year maintenance-free service life can save about 45% in overall costs. For example, replacing copper-nickel alloy with titanium tubes on an offshore platform saved over USD 2 million in maintenance costs over 30 years. Despite the higher upfront investment, considering the entire lifecycle, titanium often proves more economical.
How to Choose the Appropriate Titanium Alloy Grade?
Selection is based on factors such as operating environment, temperature, pressure, and corrosive medium:
- For shallow-water corrosion protection, Gr2 (Industrial Pure Titanium) is sufficient.
- For deep-sea high-pressure applications, Gr23 (Ti-6Al-4V ELI), with excellent toughness, is ideal for depths exceeding 6000 meters.
- For sulfur-containing environments, Gr7 (Ti-0.2Pd) effectively resists hydrogen sulfide corrosion.
- For specific load, temperature, or fatigue requirements, please consult our technical team for precise recommendations.
How to Prevent Galvanic Corrosion When Connecting Titanium with Carbon Steel or Stainless Steel?
It is recommended to use insulating gaskets (such as PTFE) or employ Titanium-Steel Explosive Clad Transition Joints to control the contact area within a relatively stable region. Additionally, limiting the current density to ≤0.1 mA/cm² (referencing AMPP guidelines) can effectively slow the occurrence of galvanic corrosion.
Will Titanium Corrode Under Deep-Sea High-Pressure Conditions?
Tests show that in environments with 100,000 ppm chloride ions and 30 MPa pressure, titanium's corrosion rate is below 0.001 mm/year (refer to ASTM G1). For even harsher deep-sea crevice corrosion, grades such as Gr29 (with ruthenium) can be selected to further enhance corrosion resistance.
What Kind of Testing and Quality Control Is Required for Titanium in Deep-Sea Applications?
For deep-sea applications, more rigorous non-destructive tests (UT, RT, PT), salt spray tests, and high-pressure simulation tests are conducted to ensure the material's safety and stability under extreme conditions.
Is Titanium Welding Complex? What Standards Should Be Followed?
Titanium welding requires stricter environmental and operational controls compared to carbon steel or stainless steel. It is recommended to use laser welding (which can reduce the heat-affected zone by 50%) or argon arc welding (AWS D10.6M standard), ensuring weld strength is ≥90% of the base material (GB/T 3620). For thick or critical components, inert gas backing protection is necessary to further improve welding quality.
How to Ensure Safety for Equipment Operating Long-Term in High-Salinity, Impact-Heavy Marine Environments?
Apart from selecting higher corrosion-resistant alloy grades, additional surface treatments (such as micro-arc oxidation or anti-fouling coatings) are recommended. Non-destructive tests (UT, RT) and high-pressure simulation tests should be performed as required. Regular inspections and anti-corrosion assessments on an annual or predetermined cycle can effectively extend the material's service life.