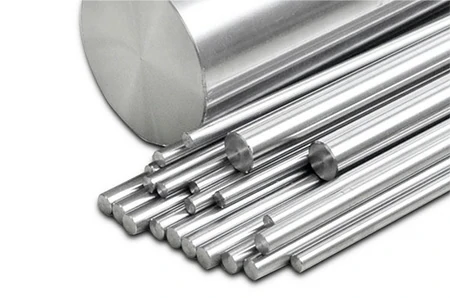
Titanium Bar
Titanium rod is a rod-shaped metal material made of titanium or titanium alloy as the main component through a specific process. Due to the high strength, low density, excellent corrosion resistance and good biocompatibility of titanium, titanium rod is widely used in industry, medical treatment, aerospace, chemical industry and other fields.
Chalco can provide various types of titanium bars, including round bars, square bars, hexagonal bars, flat bars, etc., while meeting specifications such as ASTM B348, ASME SB-348, AMS 2631, etc.
Common titanium bar types
Titanium round bar
Solid rod with a round cross section, the most widely used titanium rod.
Diameter: 3 - 305 mm (0.125" - 12")
Popular alloyss: Gr1, Gr2, Gr3, Gr4, Gr5(Ti-6Al-4V), Gr6(Ti-5Al-2.5Sn), Gr7(Ti-0.15Pd), Gr9(Ti-3Al-2.5V), Gr23(Ti-6Al-4V ELI)
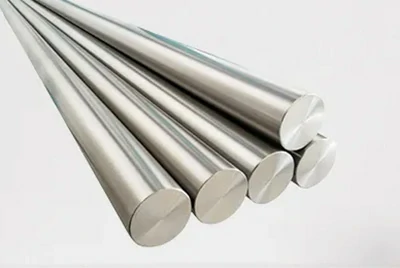
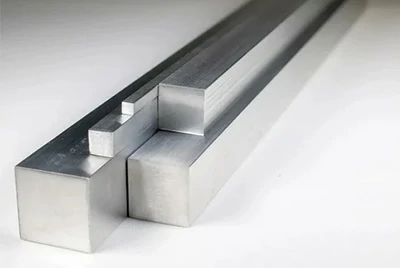
Titanium square rod bar
Titanium square bar rod is a solid rod of titanium or titanium alloy with a square cross section, widely used in aviation, chemical and medical fields.
Size: 5-200 mm (0.2 inches-8 inches)
Popular alloys: Gr1, Gr2, Gr3, Gr5, Gr7, Gr9, Gr12, Gr23
Titanium flat/rectangular bar
Titanium flat bar is a kind of titanium bar, there are two types: pure titanium flat bar and titanium alloy flat bar, mainly used for aircraft parts.
Size: 5*10mm-100*200mm (0.2"*0.4"-4"*8")
Popular alloys: Grade 2, Grade 5 (Ti-6Al-4V), Grade 9, Grade 23 (Ti-6Al-4V ELI), Grade 7, and Grade 12
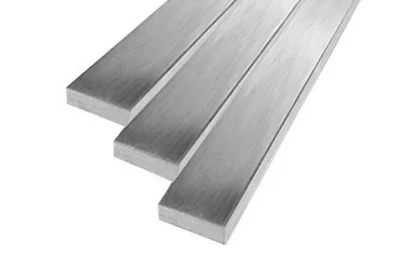
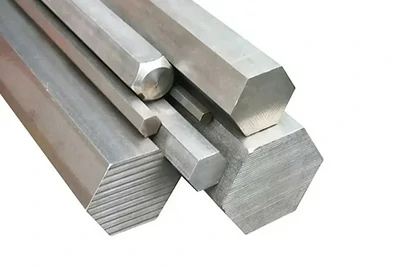
Titanium Hexagonal Bars
Titanium bars with hexagonal cross-section are mainly used for high-strength bolts and various mechanical parts.
Size: 0.5mm-350mm (0.02inch – 14inch)
Popular alloys: Grade 5 (Ti-6Al-4V), Grade 9, Grade 23 (Ti-6Al-4V ELI), Grade 12 (Ti-0.3Mo-0.8Ni)
Chalco's Special Titanium bar
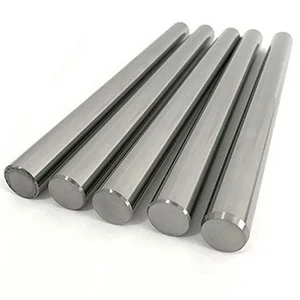
Anodized Titanium Bar
Anodized Titanium Bar is a titanium bar treated by anodizing process, which can greatly improve the corrosion resistance of titanium bar and give it a unique appearance. It is usually used in chemical equipment, jewelry, handicrafts and decorative products, medical equipment, etc.
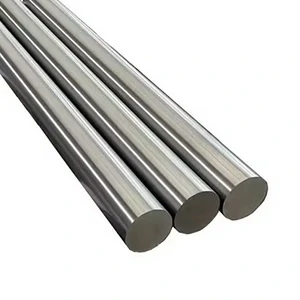
Polished titanium rod
Polished titanium rods are smooth with a mirror finish, enhancing their appearance and corrosion resistance. They are used in medical devices, jewelry, aerospace, and precision machinery due to titanium's strength and durability.
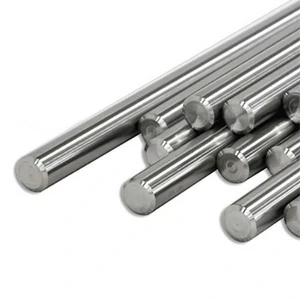
Precision ground titanium rod
Precision ground titanium rods are processed to achieve high smoothness and accuracy, ensuring excellent dimensional and surface quality. They are widely used in fields like aerospace, medical devices (such as pacemakers and electrodes), precision instruments, and high-end mechanical parts.
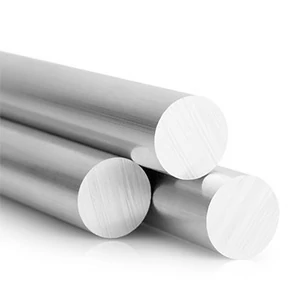
Brushed titanium rod
Brushed titanium rods have a satin finish and are used in decoration, building materials, medical devices, automotive parts, and electronics. The texture improves both appearance and wear resistance.
Popular alloy types of titanium bars
Commercially pure titanium bars
Commercially pure titanium rods, available in grades 1 to 4, are known for their excellent corrosion resistance, plasticity, and weldability. They are widely used in industries such as chemical, marine, and medical due to their durability and reliability in harsh environments.
Titanium bar gr1
The first-grade pure titanium bar is made of first-grade pure titanium with a titanium content of not less than 99.5% and has the softest texture.
Contact us now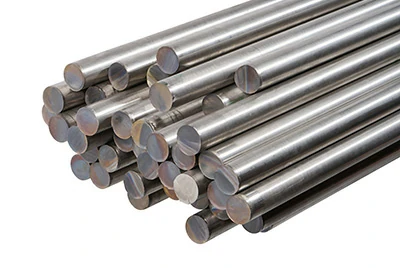
Diameter: 50-350mm
Length: 1000-6000mm
Specification: ASTM B348, ASM F67
Features: extremely high ductility, excellent corrosion resistance, low density, balanced mechanical properties and good weldability, suitable for processing into complex structures.
Applications: chemical processing equipment, medical implants/equipment, surgical instruments, aircraft engines and parts.
Grade 2 titanium bar
Grade 2 pure titanium rod is a commercially pure titanium rod with a titanium content of not less than 99.2%, which has excellent corrosion resistance and cold working properties.
Contact us now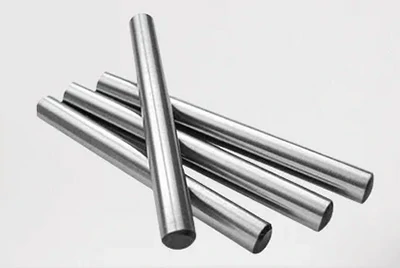
Diameter: 6mm-200mm
Length: 6000mm (max)
Specifications: ASTM-B348, ASTM-F67
Features: Grade 2 pure titanium rods have excellent corrosion resistance, superior strength to Grade 1, adequate cold workability, good weldability, biocompatibility and low thermal conductivity.
Applications: Grade 2 pure titanium rods are widely used in chemical facilities, offshore drilling, aerospace, medical equipment, power generation equipment, building structures, high-performance vehicle components and sports equipment.
Grade 3 titanium bar
Unalloyed titanium that offers increased strength, moderate ductility, good weldability, and excellent corrosion resistance in highly oxidizing and mildly reducing environments.
Contact us now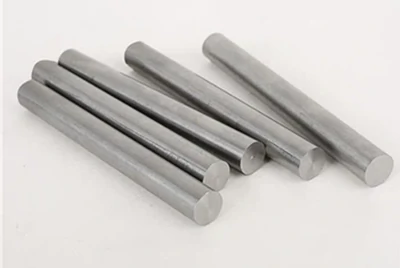
Diameter: 101.6mm - 254mm
Length: 6m
Specifications: ASME SB 348, ASTM B348, ASTM B367, ASTM B381
Features: Grade 3 aluminum bars have better strength properties than Grade 1 and Grade 2, while still having good corrosion resistance and formability. The increase in strength is attributed to the higher oxygen content than the previous two grades. Can be cast or forged
Applications: Grade 3 titanium bars are widely used in chemical processing systems, aviation parts, medical equipment, power generation equipment and high-performance vehicle parts, etc., where high strength and corrosion resistance are required.
Grade 4 titanium bar
Grade 4 titanium bar is the strongest grade of all commercially pure titanium, with excellent corrosion resistance and can adapt to various environments.
Contact us now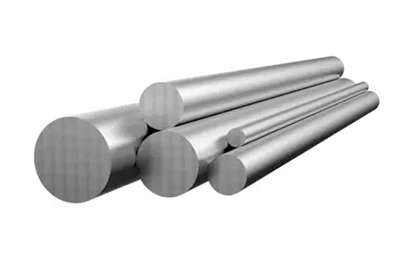
Specifications: ASTM B348, AMS 4921, ASTM F67, UNS R50700, Mil-T-9047
Features: Grade 4 titanium rod has the highest oxygen content and strength, reliable corrosion resistance, moderate ductility, good formability and weldability, and is a high-performance material among commercial pure titanium.
Application: Grade 4 titanium rod is widely used in engineering fields such as aviation engines, high-performance vehicles, chemical processing equipment, building structures, automobile and ship parts.
Alpha and near-alpha titanium alloy bar
-
Ti-5Al-2.5Sn bar gr6
Good high temperature stability, strength, oxidation resistance and creep resistance.
Application: Gas turbine engine components
-
Ti-5Al-2.5Sn bar gr6
Good weldability and cold working properties in mildly reducing to mildly oxidizing media.
Application: Aircraft piping, hydraulics, sports equipment
-
Ti-0.3Mo-0.8Ni(Grade 12) bar
Highly weldable and machinable, used in sulfur-containing environments.
Application: Chemical equipment, drilling platforms
-
Ti-6-2-4-2-S bar
Weldable, excellent strength, stability, and creep resistance up to 550°C.
Application: Airframe and automotive components, gas turbine engine
-
Ti-5Al-2.5Sn ELI Bar
Excellent combination of toughness and strength in low temperature environments.
Application: Spacecraft/structures, missile components
-
Ti-8Al-1Mo-1V Bar
High-strength with excellent creep resistance, lowest density, and highest elastic modulus.
Application: Gas turbine engine components
Alpha - beta titanium alloy bar
Ti-6Al-4V(Grade 5)bar
6AL -4V titanium bar is the most popular grade of Titanium. It has high corrosion resistance, light weight and a good strength to weight ratio.
Contact us now
Diameter: 3mm – 204mm (0.125” – 8”)
Length: 6m, custom cutting is supported.
Specifications: ASTM B348, AMS 4928, AMS 4911, UNS R56400, ASTM -F1472
Types: round bars, flat bars, cast bars, hexagonal bars, square bars
Features: high strength, toughness, ductility, good weldability and processability, applicable temperature up to 400°C.
Applications: It is commonly used for blades, disks, rings, aerospace, automotive parts, fasteners, pressure vessels, housings, hubs and forgings.
Ti-6Al-4V ELI (Grade 23) bar
Ultra-low interstitial with excellent low temperature toughness, ductility and corrosion resistance, suitable for environments as low as -255°C.
Contact us now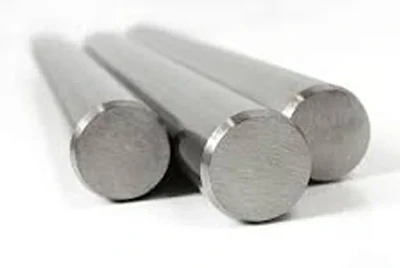
Diameter: 0.125” – 6”
Length: 6m
Specifications: ASTM-B348, AMS-4930, AMS-6932, ASTM F136
Features: Biocompatible, with medium tensile strength, improved ductility, good fatigue strength, medium fracture toughness and high resistance to seawater corrosion.
Applications: Aircraft applications, Bone fixation devices, Cryogenic and high pressure vessels, Marine applications.
-
Ti-6Al-4V-0.1Ru (Grade 29) Bar
Offer superior toughness and corrosion resistance, ideal for harsh, acidic environments.
Applications: Chemical equipment, seawater desalination plants.
-
Ti-4.5Al-3V-2Mo-2Fe bar
High-strength, heat-treatable, high-temperature, and fatigue resistance.
Applications: Airframe, gas turbine, spacecraft, and missile components.
-
Ti-6Al-7Nb bar
High-strength with good toughness and ductility, used for medical implants due to its biocompatibility.
-
Ti-6Al-6V-2Sn bar
High-strength, heat-treatable with excellent strength and hardenability, but lower toughness.
Applications: Rocket engine casings, airframe components, fasteners.
-
Ti-6Al-2Sn-4Zr-6Mo bar
High-strength titanium alloy known for its corrosion resistance, fatigue resistance, and toughness.
Applications: Turbine engine compressor stages, discs, blades.
-
Ti-4Al-4Mo-2Sn-0.5Si bar
Heat-treatable high-strength forged alloy with good strength and creep resistance.
Applications: Gas turbine engine components, aircraft fuselage.
Beta and near-beta titanium alloy bar
-
Ti-3Al-8V-6Cr-4Zr-4Mo bar
Heat-treatable alloy with high strength, toughness, and corrosion resistance.
Applications: Aircraft springs, fasteners, oil and gas piping.
-
Ti-3Al-8V-6Cr-4Zr-4Mo-0.05Pd bar Gr20
Palladium-containing Ti-38644 alloy with enhanced stress and corrosion resistance.
Applications: Naval ship components.
-
Ti-10V-2Fe-3Al bar
Heat-treatable, excellent fatigue performance, strength-toughness balance.
Applications: Airframe components, landing gear.
Titanium bars active in popular industries
Aerospace industry
Titanium's strength, low density, and heat resistance make it ideal for aircraft structures, engine parts, and precision components. Titanium bars improve fuel efficiency, performance, and reliability in aerospace applications.
Typical alloys:Grade 2, Grade 4, Ti-6AI-4V, Ti-6AI-4VELI, Ti-8AI-1Mo-1V, Ti-5AI-2.5-Sn, Ti-3AI-2.5V
Medical field
Titanium bars are used in medical implants for their biocompatibility, strength, and corrosion resistance, ensuring precision and stability.
Chalco produces medical-grade titanium, including Ti-6Al-4V and Ti-6Al-7Nb, meeting ASTM F136 and ASTM F67 standards.
Chemical industry
Titanium bars are used in the chemical industry for reactors, pipelines, pumps, and heat exchangers due to their corrosion resistance, strength, and heat resistance. They enhance equipment lifespan, reduce maintenance costs, and improve efficiency and safety.
Typical alloys: Grade 1, 3, Grade 7 Ti-0.15Pd, Ti-0.3Mo-0.8Ni.
Marine industry
Titanium bars are used in the marine industry for military equipment like ships and submarines, offering excellent corrosion resistance, strength, and lightweight properties.
Typical alloys: Gr1, Gr2, Ti-6Al-4V, Ti-6Al-4V ELI, Ti-3Al-2.5V.


Titanium bars with different manufacturing processes
Titanium billet
Titanium billet is a semi-finished titanium product, typically made through casting or continuous casting and rolling. It comes in shapes like cylindrical, square, or rectangular and serves as the raw material for producing high-performance titanium components.
Diameter range: 4.5” – 20” (114.3 mm - 508.00 mm)
Titanium or titanium alloy: Grade 2 CP 3, Grade 4 CP 1, 6Al-4V Grade 5, 6Al-2SN-4ZR-6MO, 7Al-4Mo
Specifications: ASTM B348, ASTM B381, ASTM F67, AMS 4921, AMS 4928, AMS 4967
As a preliminary processed titanium metal product, it usually has the following characteristics::
- Titanium billets have fewer processing steps and relatively low costs.
- Universal geometry can meet a variety of processing needs.
- Easy to store and distribute, suitable for large-scale inventory.
- Titanium billets require secondary processing and cannot be used directly.
- Dimensional tolerances and surface quality are low and do not meet terminal requirements.
- Performance is not optimized and requires subsequent heat treatment or surface treatment to improve performance.
The following table shows the common sizes of titanium billets:
Diameter (inches) | Diameter (mm) | Diameter (inches) | Diameter (mm) |
---|---|---|---|
6.5" | 165.1mm | 10" | 254mm |
7" | 177.8mm | 11" | 279.4mm |
7.5" | 190.5mm | 12" | 304.8mm |
8" | 203.2mm | 13" | 330.2mm |
8.5" | 215.9mm | 14" | 355.6mm |
9" | 228.6mm | 15" | 381mm |
Forged titanium bar
Forged titanium bars are made by applying pressure to titanium billets, shaping them into bars. The process improves the internal structure, removes defects like pores and inclusions, making the bars denser and enhancing their strength, toughness, and fatigue resistance.
Diameter: 8mm - 200mm
Length: 1000mm - 6000mm or as per customer's requirement
Common alloys: Ti-6Al-4V (Grade 5), Ti-6Al-4V ELI, Ti-3Al-2.5V, Ti-5Al-2.5Sn
Specifications: ASTM B348, AMS 6931, ASTM B381, ASME SB-381
Forged titanium bars usually have the following characteristics:
- Improved grain structure: Forged titanium rods make the grains finer through plastic deformation, which improves its strength and fatigue resistance.
- Enhanced resistance to stress corrosion cracking: The forging process optimizes the internal structure, reduces stress concentration, and improves resistance to stress corrosion cracking.
- Excellent superplasticity: Forged titanium rods can show superplasticity at high temperatures and are suitable for manufacturing parts with complex shapes.
- Lower oxidation rate: The surface structure of forged titanium rods is dense, which can effectively reduce high-temperature oxidation and maintain its corrosion resistance.
Extruded titanium bar
Extruded titanium bars are made by heating titanium alloy billets to the proper temperature and then shaping them into bars through a mold. These bars have a uniform internal structure, good mechanical properties, and surface quality.
Diameter range: 6 mm - 300 mm
Length: 1 m - 6 m (customizable according to customer needs)
Tolerance: typically ±0.1 mm, subject to standard or custom requirements.
Popular alloys: Grade 1, Grade 2, Ti-6Al-4V, Ti-6Al-2Sn-4Zr-2Mo, Ti-3Al-2.5V.
Extruded titanium bars usually have the following characteristics:
- Good dimensional accuracy: extruded titanium rods have smaller tolerances and smooth surfaces, reducing the difficulty of subsequent processing.
- Uniform organizational structure: During the extrusion process, the grains of titanium alloy are more uniform, improving the mechanical properties.
- Good plasticity and ductility: extruded titanium rods have good plasticity and can withstand large deformation.
- Corrosion resistance: The titanium oxide film on the surface of extruded titanium rods enhances its corrosion resistance.
- Good processability: The uniformity and plasticity of extruded titanium rods make them easy for subsequent mechanical processing.
The popular sizes of extruded titanium bars are shown in the table below:
Diameter (inch) | Diameter (mm) | Diameter (inch) | Diameter (mm) |
---|---|---|---|
0.25" | 6.35 mm | 3.5" | 88.9 mm |
0.375" | 9.525 mm | 4.0" | 101.6 mm |
0.5" | 12.7 mm | 5.0" | 127.0 mm |
0.75" | 19.05 mm | 6.0" | 152.4 mm |
1.0" | 25.4 mm | 7.0" | 177.8 mm |
1.25" | 31.75 mm | 8.0" | 203.2 mm |
1.5" | 38.1 mm | 9.0" | 228.6 mm |
2.0" | 50.8 mm | 10.0" | 254.0 mm |
2.5" | 63.5 mm | 11.0" | 279.4 mm |
3.0" | 76.2 mm | 11.81" | 300.0 mm |
Cold drawn titanium bar
Cold drawn titanium rods are made by further cold working and stretching extruded titanium rods. They are titanium rods with high dimensional accuracy, smooth surface and excellent mechanical properties.
Size range: The diameter range of cold drawn titanium rods is usually 3mm-100mm, and the length can be customized according to needs.
Popular alloys: including Grade 1, Grade 2, Grade 5 (6AL-4V), Grade 7, Grade 9 and other titanium alloys.
Cold drawn titanium rods have the following characteristics:
- High precision: Cold drawing improves dimensional accuracy, meeting strict tolerances.
- Smooth surface: It enhances surface finish for high-quality applications.
- Better mechanical properties: Strength and hardness are increased, improving performance.
- Improved toughness: Cold drawing enhances toughness, ensuring performance under stress.
- Wide adaptability: Suitable for aerospace, medical, and precision industries, meeting high standards.
Typical applications: Used in aerospace, medical devices, precision machinery, chemical equipment, marine engineering, and sports equipment, mainly for components requiring high strength, corrosion resistance, and precise dimensions.
Cold drawn titanium bars popular sizes chart:
Diameter (in.) | Diameter (mm) | Diameter (in.) | Diameter (mm) |
---|---|---|---|
0.125" | 3.18mm | 1" | 25.4mm |
0.188" | 4.78mm | 1.25" | 31.75mm |
0.25" | 6.35mm | 1.5" | 38.1mm |
0.3125" | 7.94mm | 2" | 50.8mm |
0.375" | 9.53mm | 2.5" | 63.5mm |
0.4375" | 11.11mm | 3" | 76.2mm |
0.5" | 12.7mm | 3.5" | 88.9mm |
0.625" | 15.88mm | 4" | 101.6mm |
0.75" | 19.05mm | 4.5" | 114.3mm |
Tolerance of titanium bars
The table below shows the diameter tolerances of titanium bars for different lengths, following international engineering standards. The diameter range depends on the production method, and all sizes and tolerances are agreed upon before ordering.
Alloy(s) | Spec. Diameter (in.) | Diameter Tolerance |
---|---|---|
Grade 2, 6AL-4V | Up to 0.25 | +/- 0.005" |
Grade 2, 6AL-4V, 6AL-4V (ELI) | 0.25 to 0.3125, incl. | +/- 0.005" |
Grade 2, 6AL-4V, 6AL-4V (ELI) | Over 0.3125 to 0.4375, incl. | +/- 0.006" |
Grade 2, 6AL-4V, 6AL-4V (ELI) | Over 0.4375 to 0.625, incl. | +/- 0.007" |
Grade 2, 6AL-4V, 6AL-4V (ELI) | Over 0.625 to 0.875, incl. | +/- 0.008" |
Grade 2, 6AL-4V, 6AL-4V (ELI) | Over 0.875 to 1, incl. | +/- 0.009" |
Grade 2, 6AL-4V, 6AL-4V (ELI) | Over 1 to 1.125, incl. | +/- 0.010" |
Grade 2, 6AL-4V, 6AL-4V (ELI) | Over 1.125 to 1.25, incl. | +/- 0.011" |
Grade 2, 6AL-4V, 6AL-4V (ELI) | Over 1.25 to 1.375, incl. | +/- 0.012" |
Grade 2, 6AL-4V, 6AL-4V (ELI) | Over 1.375 to 1.5, incl. | +/- 0.014" |
Grade 2, 6AL-4V, 6AL-4V (ELI) | Over 1.5 to 2, incl. | +/- 1/64" |
Grade 2, 6AL-4V | Over 2 to 2.5, incl. | + 1/32" |
Grade 2, 6AL-4V | Over 2.5 to 3.5, incl. | + 3/64" |
Grade 2, 6AL-4V | Over 3.5 to 4.5, incl. | + 1/16" |
What services can Chalco provide?
Customization services
- Size customization: Titanium bars with different diameters and lengths can be provided according to customer requirements.
- Alloy customization: Different titanium alloys, such as pure titanium, Ti-6Al-4V, Ti-5Al-2.5Sn, etc., can be supplied based on customer needs.
- Shape customization: In addition to standard round titanium bars, custom shapes (such as square, oval, etc.) can be provided according to customer specifications.
- Length customization: Titanium bars of various lengths can be supplied to meet specific application needs.
- Precision customization: High precision dimensions are available to ensure the titanium bars meet strict technical standards.
- Surface finish customization: Different surface finishes, such as mirror, smooth, or rough surfaces, can be offered as required.
- Cutting customization: Titanium bars can be precisely cut to the required sizes based on customer needs.
Surface treatment services
- Pickling: Removes surface oxide layers and impurities, improving surface smoothness and enhancing corrosion resistance.
- Sandblasting: Uses high-pressure abrasive blasting to clean the surface, increasing roughness and improving coating adhesion.
- Mechanical polishing: Uses abrasives to mechanically smooth the surface, achieving a high-gloss, flat finish.
- Chemical polishing: Uses chemical solutions to polish the surface, removing microscopic unevenness and enhancing brightness.
- Anodizing: An electrochemical process that creates a stable oxide film on the surface, enhancing corrosion resistance and providing color decoration.
- Coating: Applies a protective or functional coating through spraying or electroplating to improve wear resistance or provide special properties.
Customer service
- Free sample shipping: Provide free sample shipping for customers to test before placing an order.
- Size customization: Customize products in various specifications and sizes based on customer needs to meet specific application requirements.
- Discounts: Offer pricing discounts for long-term customers and bulk orders to ensure competitive titanium bar prices.
- Solution provision: Offer professional material selection and application solutions to ensure optimal performance based on customer needs.
- Worry-free after-sales: Provide comprehensive after-sales services to promptly address any issues customers encounter during use.
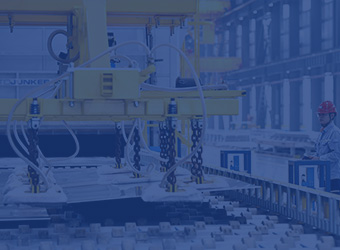