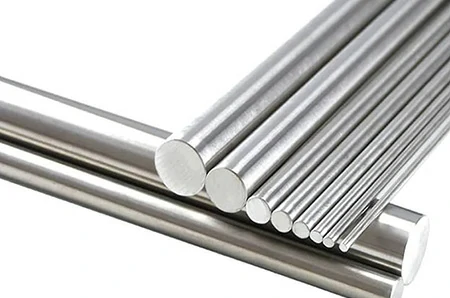
Grade 2 (UNS R50400) Titanium Bar
Grade 2 titanium bar is a type of bar made from pure titanium (Grade 2), known for its excellent corrosion resistance, good strength, and lightweight advantages. It is widely used in industries such as aerospace, medical, chemical, and marine engineering.
As an important base material in industrial fields, Grade 2 titanium bar has become the first choice for many high-demand applications due to its high cost-performance ratio and outstanding performance.
The stock sizes of Chalco gr2 titanium bar
Product | Diameter(inch) | Diameter(mm) | Length(inch) | Length(m) |
---|---|---|---|---|
Grade 2 Titanium Bar | 0.1" | 3mm | 118.1" | 3m |
Grade 2 Titanium Bar | 0.2" | 4mm | 118.1" | 3m |
Grade 2 Titanium Bar | 0.2" | 5mm | 118.1" | 3m |
Grade 2 Titanium Bar | 0.2" | 6mm | 118.1" | 3m |
Grade 2 Titanium Bar | 0.3" | 7mm | 118.1" | 3m |
Grade 2 Titanium Bar | 0.3" | 8mm | 118.1" | 3m |
Grade 2 Titanium Bar | 0.4" | 9mm | 118.1" | 3m |
Grade 2 Titanium Bar | 0.4" | 10mm | 118.1" | 3m |
Grade 2 Titanium Bar | 0.4" | 11mm | 118.1" | 3m |
Grade 2 Titanium Bar | 0.5" | 12mm | 118.1" | 3m |
Grade 2 Titanium Bar | 0.5" | 13mm | 118.1" | 3m |
Grade 2 Titanium Bar | 0.6" | 14mm | 118.1" | 3m |
Grade 2 Titanium Bar | 0.6" | 15mm | 118.1" | 3m |
Grade 2 Titanium Bar | 0.6" | 16mm | 118.1" | 3m |
Grade 2 Titanium Bar | 0.7" | 17mm | 118.1" | 3m |
Grade 2 Titanium Bar | 0.7" | 18mm | 118.1" | 3m |
Grade 2 Titanium Bar | 0.7" | 19mm | 118.1" | 3m |
Grade 2 Titanium Bar | 0.8" | 20mm | 118.1" | 3m |
Grade 2 Titanium Bar | 0.8" | 21mm | 118.1" | 3m |
Grade 2 Titanium Bar | 0.9" | 22mm | 118.1" | 3m |
Grade 2 Titanium Bar | 0.9" | 23mm | 118.1" | 3m |
Grade 2 Titanium Bar | 0.9" | 24mm | 118.1" | 3m |
Grade 2 Titanium Bar | 1" | 25mm | 118.1" | 3m |
Grade 2 Titanium Bar | 1" | 26mm | 118.1" | 3m |
Grade 2 Titanium Bar | 1.1" | 27mm | 118.1" | 3m |
Grade 2 Titanium Bar | 1.1" | 28mm | 118.1" | 3m |
Grade 2 Titanium Bar | 1.1" | 29mm | 118.1" | 3m |
Grade 2 Titanium Bar | 1.2" | 30mm | 118.1" | 3m |
Grade 2 Titanium Bar | 1.2" | 31mm | 118.1" | 3m |
Grade 2 Titanium Bar | 1.3" | 32mm | 118.1" | 3m |
Grade 2 Titanium Bar | 1.3" | 33mm | 118.1" | 3m |
Grade 2 Titanium Bar | 1.3" | 34mm | 118.1" | 3m |
Grade 2 Titanium Bar | 1.4" | 35mm | 118.1" | 3m |
Grade 2 Titanium Bar | 1.4" | 36mm | 118.1" | 3m |
Grade 2 Titanium Bar | 1.5" | 37mm | 118.1" | 3m |
Grade 2 Titanium Bar | 1.5" | 38mm | 118.1" | 3m |
Grade 2 Titanium Bar | 1.5" | 39mm | 118.1" | 3m |
Grade 2 Titanium Bar | 1.6" | 40mm | 118.1" | 3m |
Grade 2 Titanium Bar | 1.6" | 41mm | 118.1" | 3m |
Grade 2 Titanium Bar | 1.7" | 42mm | 118.1" | 3m |
Grade 2 Titanium Bar | 1.7" | 43mm | 118.1" | 3m |
Grade 2 Titanium Bar | 1.7" | 44mm | 118.1" | 3m |
Grade 2 Titanium Bar | 1.8" | 45mm | 118.1" | 3m |
Grade 2 Titanium Bar | 1.8" | 46mm | 118.1" | 3m |
Grade 2 Titanium Bar | 1.9" | 47mm | 118.1" | 3m |
Grade 2 Titanium Bar | 1.9" | 48mm | 118.1" | 3m |
Grade 2 Titanium Bar | 1.9" | 49mm | 118.1" | 3m |
Grade 2 Titanium Bar | 2" | 50mm | 118.1" | 3m |
Grade 2 Titanium Bar | 2.2" | 55mm | 118.1" | 3m |
Grade 2 Titanium Bar | 2.4" | 60mm | 118.1" | 3m |
Grade 2 Titanium Bar | 2.6" | 65mm | 118.1" | 3m |
Grade 2 Titanium Bar | 2.8" | 70mm | 118.1" | 3m |
Grade 2 Titanium Bar | 3" | 75mm | 118.1" | 3m |
Grade 2 Titanium Bar | 3.1" | 80mm | 118.1" | 3m |
Grade 2 Titanium Bar | 3.3" | 85mm | 118.1" | 3m |
Grade 2 Titanium Bar | 3.5" | 90mm | 118.1" | 3m |
Grade 2 Titanium Bar | 3.7" | 95mm | 118.1" | 3m |
Grade 2 Titanium Bar | 3.9" | 100mm | 118.1" | 3m |
Grade 2 Titanium Bar | 4.1" | 105mm | 118.1" | 3m |
Grade 2 Titanium Bar | 4.3" | 110mm | 118.1" | 3m |
Grade 2 Titanium Bar | 4.5" | 115mm | 118.1" | 3m |
Grade 2 Titanium Bar | 4.7" | 120mm | 118.1" | 3m |
Grade 2 Titanium Bar | 4.9" | 125mm | 118.1" | 3m |
Grade 2 Titanium Bar | 5.1" | 130mm | 118.1" | 3m |
Above are the stock sizes of Chalco GR2 titanium bar. Bars with the same diameter but different lengths can be cut to size. If you don’t find the ideal size you need, please contact us promptly.Quick Quote
Chalco's specialty Grade 2 titanium bar
Cold drawn Grade 2 titanium bar
Cold drawn Grade 2 titanium bar is processed through a cold drawing process at room temperature, offering higher strength, precision, and excellent surface quality. It is suitable for applications that require high performance and precision.
Contact us now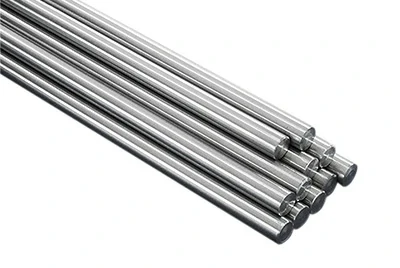
Grade 2 cold drawn titanium bar typically has the following characteristics:
- Increased strength: The strength and hardness of the titanium bar are enhanced after cold drawing, making it suitable for high-load applications.
- High surface finish: The surface is smooth with no obvious defects, ideal for applications where appearance is important.
- High precision: Small dimensional tolerances, suitable for manufacturing precision components.
- Improved fatigue performance: Enhanced fatigue resistance, adapting to long-term repeated loads.
Main applications after cold drawing:
Mainly used in medical devices (such as bone screws, joint prostheses), aerospace (such as components, fasteners), chemical equipment (such as reactors, pipelines), marine engineering (such as ship components, offshore platform equipment), and high-performance automotive parts, all of which require high precision, high strength, and corrosion resistance.
Anodized Grade 2 titanium bar
Grade 2 anodized titanium bar is processed through the anodizing process, forming a hard and corrosion-resistant titanium oxide film on the surface. It offers excellent surface protection and aesthetic appearance.
Contact us now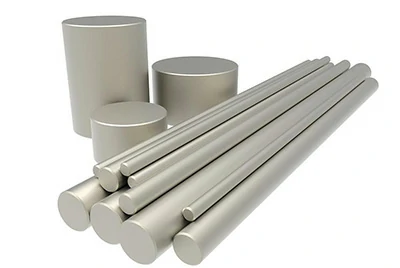
Characteristics after anodizing:
- Enhanced corrosion resistance: The oxide layer formed on the titanium surface during anodizing provides additional protection, significantly improving corrosion resistance.
- High hardness and wear resistance: The oxide layer increases surface hardness, enhancing scratch resistance and wear durability.
- Aesthetic and decorative: The anodized titanium surface presents various colors, offering excellent decorative effects.
- Good electrical insulation: The anodized layer provides excellent electrical insulation for titanium.
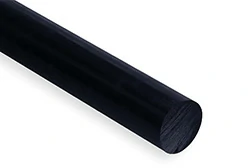
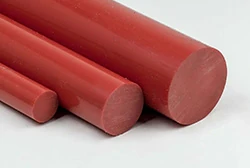
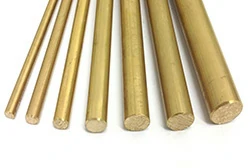
Main applications:
Mainly used in medical devices (such as implants), aerospace (such as external structural components), chemical equipment (such as reactors, pipelines), decorative applications (such as jewelry, fashion accessories), and high-end sports equipment, especially in situations where corrosion resistance, wear resistance, and aesthetic appearance are essential.
Grade 2 titanium bars of different production process types from Chalco
Grade 2 titanium billet
Grade 2 titanium billet is a raw material form made from GR2 commercial pure titanium through casting or forging processes. It typically appears as cylindrical or square blocks, which can be further processed into components and finished products via extrusion, rolling, or machining.
Diameter: 10mm - 500mm (customizable based on requirements)
Length: 100mm - 4000mm (customizable based on requirements)
Applications: Used for further processing or common components.
Grade 2 forged titanium bar
Grade 2 Forged Titanium Bar is made from high-purity titanium material (over 99.2%) processed through forging.
Diameter: From 6mm to 300mm (larger sizes available upon request)
Length: Typically between 200mm and 3000mm, with different lengths available based on actual application
Other Shapes: Square, rectangular, and other forged titanium bar shapes are available to meet special processing requirements.
Through the forging process, the internal structure of Grade 2 titanium bars is improved. Forging rearranges the metal grains, eliminates casting defects, and enhances the metal's density and mechanical properties. Forged Grade 2 titanium bars exhibit the following characteristics:
- Enhanced mechanical properties: The forging process improves the internal structure of the titanium bar, increasing its strength and toughness, making it suitable for high-load applications.
- Superior corrosion resistance: Forged Grade 2 titanium bars demonstrate excellent corrosion resistance in aggressive environments, such as seawater, strong acids, and strong alkalis.
- Improved machinability: Forging makes the titanium bars more uniform, making them easier to machine and weld, thereby improving processing efficiency and stability.
- Higher density and consistency: The forging process eliminates internal voids, ensuring uniform density and greater structural stability.
- Improved fatigue resistance: Forging enhances the titanium bar's fatigue resistance, making it suitable for applications subjected to repeated loading over extended periods.
- Improved ductility and plasticity: The forging process increases the ductility of the titanium bars, making them easier to further process, such as drawing and bending.
- High-precision surface quality: The forging process provides a smooth surface, reducing surface defects and the need for post-processing adjustments..
Uses of forged titanium bars:
- Aerospace: Used for lightweight, high-strength structural components in aircraft, satellites, and other aerospace applications.
- High-strength industrial parts: Such as power generation equipment, heavy machinery components, fasteners, etc.
- Military industry: Used to manufacture high-strength weapons, tanks, ships, and other military applications.
- Chemical equipment: Used in reactors, pressure vessels, and other equipment that must withstand higher mechanical pressures.


Grade 2 rolled titanium bar
Grade 2 rolled titanium bars belong to the commercially pure titanium series, known for their excellent corrosion resistance, moderate strength, good machinability, and lightweight properties. They offer a high cost-performance ratio and are widely used in various industrial and civilian fields.
Diameter: 6mm - 200mm
Length: 1000mm - 6000mm (customizable based on requirements)
Typical applications of rolled titanium bars include:
- Chemical equipment: Used in the manufacturing of corrosion-resistant pipes, storage tanks, heat exchangers, etc.
- Marine engineering: Suitable for ship components, seawater desalination equipment, etc.
- Medical: Used in medical devices such as orthopedic implants, dental equipment, etc.
- Sports equipment: Such as high-end bicycle frames, sporting gear, etc.


How to choose between rolled titanium bars and forged titanium bars?
Comparison Dimension | Rolled Titanium Bars | Forged Titanium Bars |
---|---|---|
Strength & Hardness | Moderate strength, suitable for medium to low-load applications. | Higher strength and hardness, suitable for high-strength, high-load environments. |
Ductility & Toughness | Good ductility, easy to process into complex shapes, moderate toughness. | Slightly lower ductility, but higher toughness, able to withstand significant mechanical impact. |
Surface Quality | Smooth and flat surface, can be used directly without additional treatment. | Rougher surface, usually requires further processing such as polishing or coating. |
Machinability | Excellent machinability, suitable for turning, milling, and other general machining. | More difficult to machine, requires more durable tools, suitable for precision or high-strength machining. |
Corrosion Resistance | Good corrosion resistance, suitable for chemical equipment and marine engineering applications. | Also excellent corrosion resistance, but performs better in high-strength environments. |
Weight Requirements | Lighter, suitable for weight-sensitive applications. | Slightly heavier, suitable for high-load fields where weight is not the core concern. |
Cost | Lower production cost, high cost-performance ratio, suitable for routine industrial applications. | Higher production cost, suitable for professional fields requiring high strength and performance. |
Typical Applications | Chemical equipment, medical instruments, sporting goods, light industrial components. | Aerospace, military equipment, heavy machinery, high-strength industrial parts for high-load scenarios. |
Key Selection Factors | Prioritize cost, ease of processing, and surface quality requirements. | Focus on strength, toughness, and long-term performance needs, especially for critical structural components. |
The chemical composition of GR2 titanium bar
Element | Percentage |
---|---|
C | 0.1 max |
Fe | 0.3 max |
H | 0.015 max |
N | 0.03 max |
O | 0.25 max |
Ti | 99.3 min |
The physical properties of GR2 titanium bar
Property | Value |
---|---|
Density | 0.163 lb/in³ |
Ultimate Tensile Strength | 62.4 ksi |
Yield Tensile Strength | 49.3 ksi |
Shear Modulus | 5,510 ksi |
Shear Strength | 55.1 ksi |
Fatigue Strength | 40.6 ksi |
Hardness Rockwell / Brinell | B89 / 180 |
Elongation at Break | 26% |
Reduction of Area | 34% |
Modulus of Elasticity | 14,800 ksi |
Poisson's Ratio | 0.34 |
Machinability Percentage | 75% |
Melting Point | 2,930-3,020 °F |
Specific Heat | 1.3 x 10⁻¹ BTU/lb-°F |
Thermal Conductivity | 156 BTU-in/hr-ft²-°F |
Electrical Conductivity | 3.6% IACS |
Why choose Chalco?
Manufacturing Capabilities
- Vacuum Induction Furnace: Capable of processing over 5,000 tons of titanium alloy material annually, ensuring the melting of high-purity titanium alloys that meet the strict requirements of industries such as aerospace and nuclear energy.
- Large Forging Press: Produces 2,000 to 3,000 tons of titanium alloy forgings annually, ensuring high strength and toughness in large batches of titanium bars, suitable for aerospace, automotive, and high-pressure applications.
- Fully Automated Titanium Hot Rolling Mill: Processes over 5,000 tons of titanium material annually, producing titanium bars of various specifications through efficient automation technology, ensuring fast delivery and high consistency.
- CNC Precision Machining Equipment: Can precisely process over 2,000 tons of titanium bars annually, supporting small-batch customization and the machining of complex shapes to meet the precision requirements of various industries.
- Electron Beam Furnace: Processes hundreds of tons of titanium alloys annually, providing high-purity, high-performance titanium alloys widely used in aerospace, nuclear energy, and medical fields.
- Laser Cutting and Precision Welding Equipment: Conducts thousands of precise cutting and welding operations annually, ensuring excellent performance in high-precision and complex shape machining of titanium bars.
- Titanium Anodizing Equipment: Processes thousands of tons of titanium material annually for surface treatment, offering high corrosion resistance and various oxidation effects, widely used in high-end industries such as medical and aerospace.
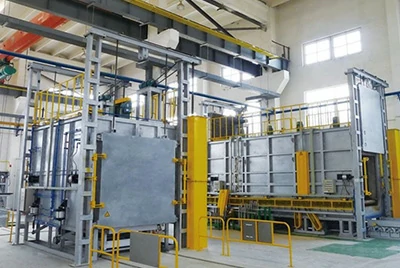
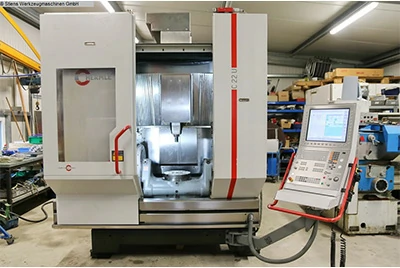
Quality Services
- Free Samples: Chalco provides free samples to help customers evaluate the quality, size, and performance of titanium bars. Customers can assess whether the titanium bars meet their application needs to make more informed purchasing decisions.
- Wide Range of Stock: Chalco holds a large inventory of titanium bars in warehouses around the world, covering various specifications, sizes, and materials. Whether standard or custom titanium bars, customers can quickly obtain the products they need from existing stock.
- Customization Services: Chalco offers personalized customization services based on customer requirements, ensuring that the specifications, sizes, and materials of the titanium bars meet the customer’s unique needs. Whether for small-batch production or large orders, Chalco can adjust production plans flexibly to meet various customization demands.
- Comprehensive Technical Support: Chalco’s technical team provides full technical support to customers, from material selection to processing and performance testing, ensuring that products meet industry standards. Whether it’s technical consulting or process optimization, Chalco can offer professional and timely solutions to improve production efficiency.
- Fast Delivery: With efficient production lines and strong manufacturing capacity, Chalco ensures on-time delivery to meet urgent customer needs. Whether small or large orders, Chalco guarantees timely delivery through precise production planning.
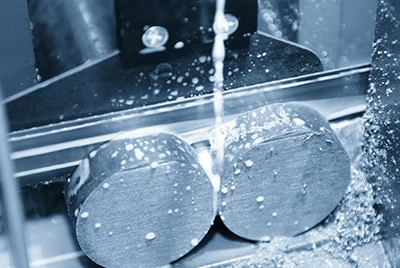
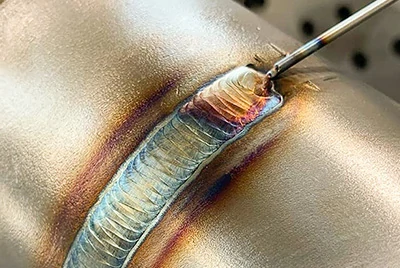
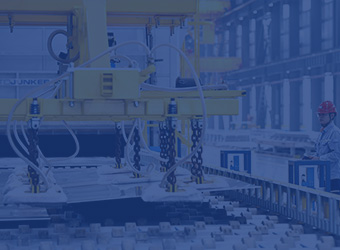