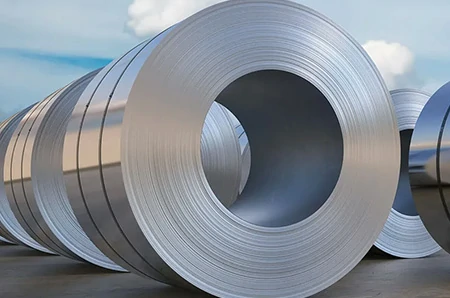
Titanium Foil
Titanium foil refers to titanium plates, strips, rolls, or sheets with a thickness of less than or equal to 0.1mm. It has a silvery-white metallic luster and is characterized by light weight, high strength, and good corrosion resistance.
Typical Titanium Foil Alloys
CP4 grade 1 titanium foil
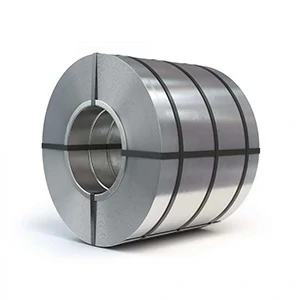
Grade 1 titanium foil, with its excellent ductility and good corrosion resistance, is widely used in the medical, chemical, and food industries. It is usually thin in size and suitable for applications requiring high ductility and corrosion resistance.
Thickness:0.01mm ~ 0.1mm
Width:200mm ~ 1000mm
Length:Either in coil or sheet form, customizable according to requirements.
Characteristics: Softest and most ductile, with excellent corrosion resistance. Excellent workability, suitable for cold working.
This material is typically used in the following fields:
- Chemical Equipment: Storage tanks for corrosive liquids, heat exchangers.
- Medical Field: Precision medical device components.
- Battery Industry: Lithium battery electrode plate materials.
Grade 2 titanium foil
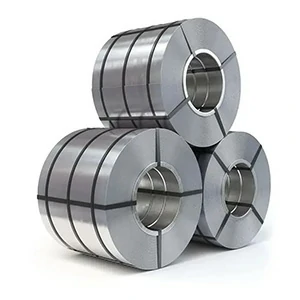
Grade 2 titanium foil is a high-purity commercially pure titanium (CP-Ti) material with excellent corrosion resistance, moderate strength, and good formability. Its lightweight, high-strength, and excellent chemical resistance make it widely used in aerospace, medical, marine engineering, and chemical industries.
Thickness:0.015mm ~ 0.1mm
Width:200mm ~ 1200mm
Length:Supplied mostly as long coils, but can also be cut into sheets.
Characteristics: Higher strength than Grade 1, with equally excellent corrosion resistance. Good weldability and cold workability.
Common applications:
- Chemical industry: Pipeline linings, inner walls of pressure vessels.
- Construction industry: Decorative titanium foil for building facades.
- Aerospace: Inner linings for structural components or corrosion-resistant parts.
Grade 4 titanium foil
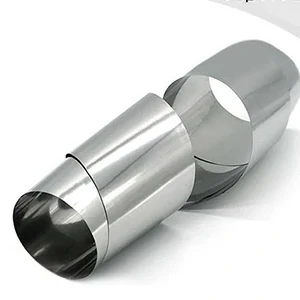
Grade 4 titanium foil is the highest strength grade in the commercially pure titanium (CP-Ti) series. It has excellent corrosion resistance and good biocompatibility while maintaining good ductility and weldability.
Thickness: 0.02mm ~ 0.1mm
Width: 200mm ~ 800mm
Length: Available in coils or custom-cut sheets.
Characteristics: Highest strength of pure titanium, while still maintaining good corrosion resistance. Performs excellently in strongly corrosive or high-strength environments.
Common Applications:
- Medical Field: Thin sheet material for surgical implants.
- Marine Industry: Used as a protective layer for ship components.
- Military Industry: Lining material for armored vehicles or submarines.
Grade 5(Ti-6Al-4V)titanium foil
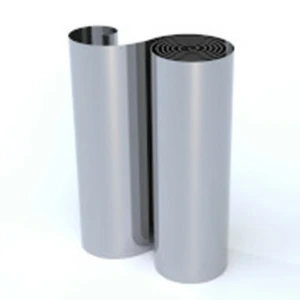
Ti-6Al-4V titanium foil is a high-performance α-β titanium alloy combining high strength, excellent corrosion resistance, and good biocompatibility. Its exceptional strength-to-weight ratio and high-temperature performance make it widely used in aerospace, medical implants, high-end manufacturing, and chemical equipment, particularly for demanding precision parts.
Thickness: 0.02mm ~ 0.1mm
Width: 200mm ~ 1000mm
Length: Long coils or short sheets, customizable as needed.
Characteristics: High strength, light weight, excellent corrosion and oxidation resistance. Good high-temperature performance, usable below 400°C.
Common applications:
- Aerospace: Protective film for aircraft skin and engine parts.
- High-end automobiles: Surface protection material for racing car parts.
Ti-3Al-2.5V (Grade 9) titanium foil
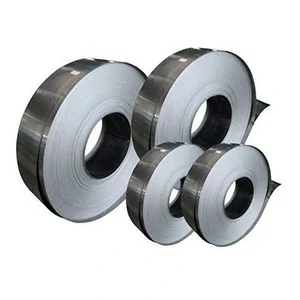
Ti-3Al-2.5V (grade 9) titanium foil is a high-strength, easily formable, and corrosion-resistant titanium alloy material. It is often referred to as "half 6-4 titanium" and has good cold working and welding properties. Due to its excellent performance, grade 9 titanium foil is widely used in aerospace, medical, chemical, and automotive industries.
Thickness: 0.02mm ~ 0.1mm
Width: 200mm ~ 600mm
Length: Available in sheet or coil form.
Features: Medium strength, good cold workability, and corrosion resistance. Lightweight, suitable for lightweight structural requirements.
Common applications:
- Aerospace: Thin protective films for lightweight components.
- Industrial: Heat exchanger sheets and pipeline lining materials.
- Medical: Thin film materials for surgical implants.
Grade 23(Ti-6Al-4V ELI)titanium foil
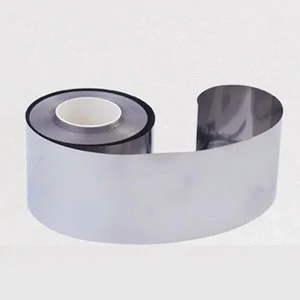
Grade 23 titanium foil, also known as Ti-6Al-4V ELI, is an ultra-low interstitial variant of Ti-6Al-4V. It features excellent biocompatibility, high strength, ductility, and corrosion resistance, making it ideal for surgical implants, orthopedic instruments, and dental restorations.
Thickness: 0.02mm ~ 0.05mm
Width: 200mm ~ 800mm
Length: Available in coil or cut sheet form.
Features: Ultra-low interstitial (ELI) for enhanced biocompatibility. High fatigue resistance and corrosion resistance.
Common applications:
- Medical: Surface material for implants and surgical instruments.
- Aerospace: Corrosion-resistant coating for high-strength components.
- Defense: Protective film for specialized equipment.
Chalco specialty titanium foil products
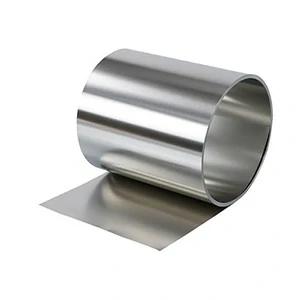
Anodized titanium foil is a material that forms a titanium oxide film on the surface through electrolysis. This film enhances corrosion resistance, wear resistance, and hardness while allowing for various colors. It is widely used in medical devices, electronic components, aerospace, and decorative applications.
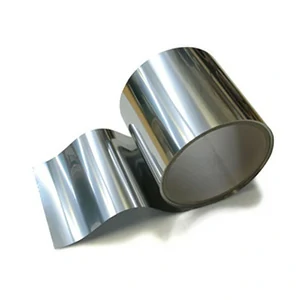
Polished titanium foil undergoes mechanical or chemical polishing for a smooth, mirror-like surface. It is commonly used in decorative applications, electronics, and industries requiring high surface quality, such as high-end decor, medical devices, and precision equipment.
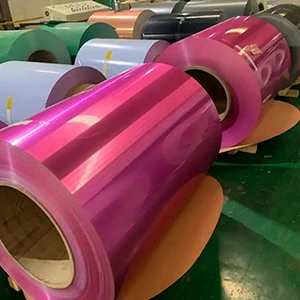
Color-coated titanium foil is produced by applying a uniform layer of colored coating to the surface, creating various visual effects. It enhances corrosion resistance, wear resistance, and surface protection. Common applications include architectural decoration, electronic device casings, and high-end appliances.
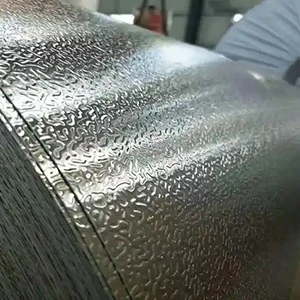
Embossed titanium foil is processed to create specific patterns or textures on the surface. It is widely used in decorative applications such as high-end appliances, architectural decoration, and automotive interiors.
Anodized titanium foil is a material that forms a titanium oxide film on the surface through electrolysis. This film enhances corrosion resistance, wear resistance, and hardness while allowing for various colors. It is widely used in medical devices, electronic components, aerospace, and decorative applications.
Industry solutions for titanium foil
Aerospace: Titanium foil is primarily used in engine components, fuel tanks, and insulation layers, requiring high strength, heat resistance, and oxidation resistance. Recommended alloys include grade 5 (Ti-6Al-4V) for its high strength and heat resistance, and grade 2 pure titanium for its excellent corrosion resistance, making it ideal for sealing layers.
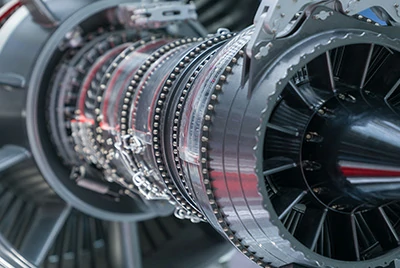
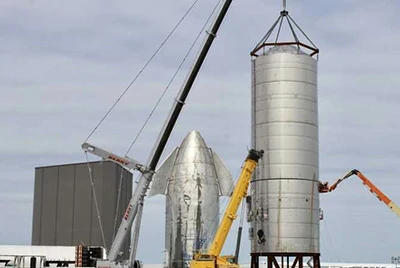
Medical: Titanium foil is ideal for medical devices and implants due to its high biocompatibility and corrosion resistance. Common alloys include grade 23 (Ti-6Al-4V ELI) for its excellent biocompatibility, making it suitable for implants, while grade 1/2 pure titanium is often used for medical device casings.
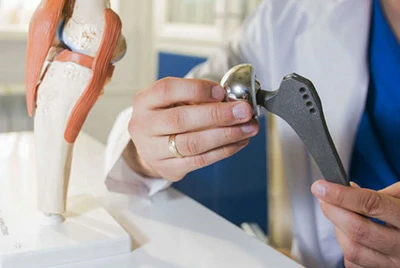
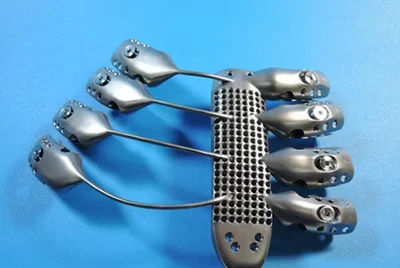
Electronics: Used in battery casings, heat sinks, and shielding materials. Grade 1 offers excellent ductility and thermal conductivity for complex shapes, while grade 5 provides higher strength for electronic components.

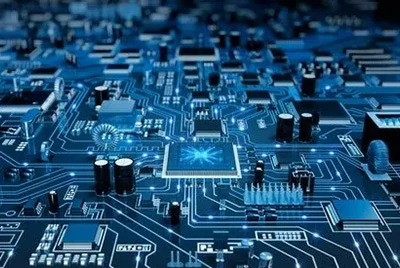
Automotive: Used in exhaust systems, engine components, and decorative parts. Grade 9 offers strength and corrosion resistance for exhaust systems, while grade 5 is ideal for high-strength components.
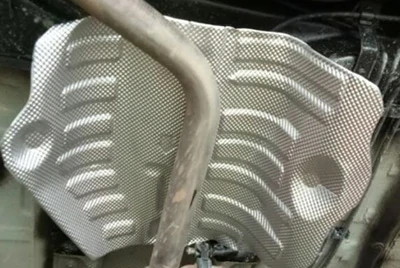
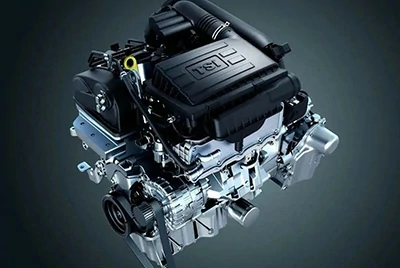
Industrial: Used in chemical equipment, heat exchangers, and desalination systems for its corrosion resistance and durability. Grade 2 is ideal for chemical pipelines and tanks, while grade 7 suits highly corrosive environments like chemical processing and marine equipment.

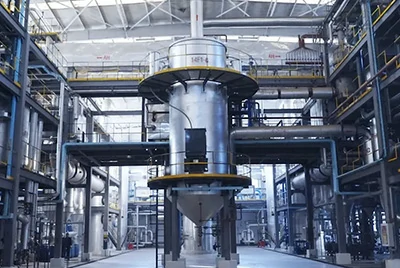
Decorative: Used in architecture, appliances, and jewelry for its aesthetics and durability. Grade 1 is ideal for embossing, polishing, and coating, while grade 9 offers lightweight strength for complex designs.
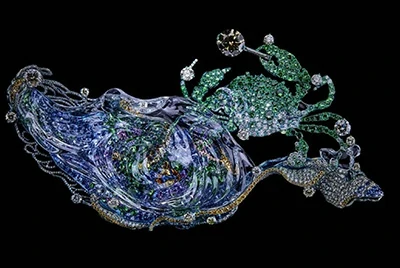
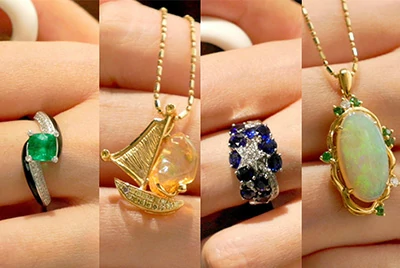
Energy: Used in fuel cells, solar equipment, and nuclear power plants for heat resistance and stability. Grade 2 is ideal for heat exchangers and electrodes, while grade 12 enhances corrosion resistance in nuclear applications.
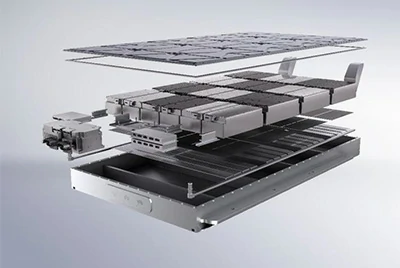
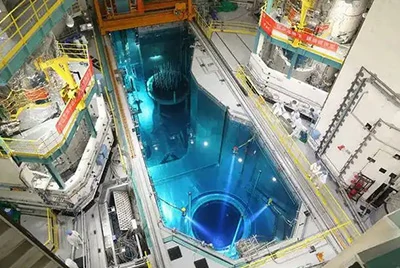
Chalco titanium foil: quality and application value
Chalco's titanium foil has a uniformly glossy, clean, and smooth surface
Chalco’s titanium foil undergoes precision rolling and rigorous cleaning to ensure a uniformly glossy, smooth, and defect-free surface. Advanced surface treatment technology eliminates visible roll marks, pitting, pinholes, and other imperfections.
Application value:
Medical industry: The smooth surface prevents bacterial adhesion, reducing infection risks. In implants like heart valves and artificial joints, it enhances long-term biocompatibility and stability, improving implantation outcomes.
Aerospace industry: Surface quality is crucial for performance. Defect-free titanium foil ensures higher strength and durability, making it ideal for engine components, fuel tanks, and insulation layers. A high-quality surface reduces airflow resistance and enhances overall part efficiency.
Chalco's titanium foil is free from creases, streaks, bright lines, and other rolling defects
Chalco strictly controls the titanium foil production process, ensuring that each piece undergoes thorough inspection to eliminate creases, stains, or bright lines. The surface consistency and perfection are achieved through advanced technology and equipment, meeting high-quality standards.
Application value:
High-end manufacturing: In aerospace, automotive, and marine industries, flawless titanium foil enhances both performance and aesthetics. For high-strength components like engine parts and exhaust systems, a defect-free surface helps maintain structural stability and prevents fatigue failure.
Electronics industry: Chalco’s titanium foil is crucial for precision electronics, especially in battery casings and heat sinks. A surface free from creases, stains, and bright lines ensures superior appearance and functionality of components.
The surface of the titanium foil has no color variation
Chalco focuses on the consistency of titanium foil surfaces, utilizing advanced surface treatment and quality control technologies to ensure uniform color across every piece, completely eliminating color variation. The flawless surface guarantees high quality and a refined appearance.
Application value:
Decoration industry: In architectural decoration and home appliances, Chalco's titanium foil with no color variation is an ideal material. Its uniform surface enhances visual appeal, ensuring consistency in high-end decorative products such as building facades, appliance casings, jewelry, and watches.
Electronics industry: In electronic products, especially for display casings, sensors, or precision components, titanium foil without color variation enhances aesthetic consistency, brand value, and consumer recognition.
The surface of titanium foil is free from oil contamination
Chalco strictly controls oil contamination and stains during titanium foil production, ensuring that each sheet is free from oil residue, odor, or visible stains. Through multiple cleaning processes and precise surface treatment, the foil meets the highest cleanliness standards, preventing any negative impact on subsequent processing and final product performance.
Application value:
Medical industry: The cleanliness of titanium foil is crucial for medical devices and implants, directly affecting biocompatibility and safety. Chalco’s clean surface prevents potential contamination, ensuring compliance with strict medical standards and enhancing implant safety.
Chemical industry: In applications such as heat exchangers and storage tanks, oil contamination can compromise corrosion resistance and chemical stability. Chalco’s clean titanium foil ensures superior corrosion resistance, making it ideal for long-term use in highly acidic or alkaline environments.
What thicknesses of titanium foil can Chalco produce?
Ultra-thin titanium foil
Thickness: ≤ 0.02mm
Applications: Ultra-thin titanium foil is commonly used in electronic components, sensors, aerospace, and high-end decorative applications. Due to its extremely thin characteristics, it is suitable for lightweight designs, precision equipment, and specialized high-tech products.
Tin titanium foil
Tickness: 0.02mm - 0.05mm
Applications: titanium foil within this thickness range is used in medical devices (such as dental implants and surgical instruments), electronic products, decorative items, and chemical equipment. it offers excellent ductility, corrosion resistance, and workability, making it suitable for applications requiring thin yet high-performance materials.
Medium-thin titanium foil
Thickness: 0.05mm - 0.1mm
Applications: medium-thin titanium foil is suitable for applications requiring higher structural strength, such as aerospace components, automotive parts, heat exchangers, and marine equipment. this thickness combines strength and lightweight properties, making it widely used in industrial, transportation, and energy sectors.
Titanium foil production process
Melting and consolidation
The production of titanium alloy sheets begins with the smelting of titanium ore, where high-temperature processing converts the ore into sponge titanium. The sponge titanium is then compacted and undergoes vacuum arc remelting or electron beam melting to form ingots.
Hot rolling
The ingots are further processed into thinner sheets with thicknesses ranging from 1 mm to 10 mm. This stage involves multiple rolling passes and intermediate annealing to ensure uniformity and ductility.
Cold rolling
After cooling the hot-rolled sheets to room temperature, cold rolling is performed to gradually reduce the sheet thickness to the required foil specifications (typically less than 0.1 mm). Multiple intermediate annealing processes may be required during cold rolling to reduce work hardening and improve ductility.
Precision rolling
Building upon cold rolling, high-precision rolling mills further process the titanium foil to ensure thickness accuracy and surface quality, with thickness control reaching the micron level.
Surface treatment
Treating the surface of titanium foil to enhance quality includes:
- Pickling: removes surface oxides and impurities.
- Polishing: improves surface smoothness to meet decorative or high-quality surface requirements.
- Anodizing: forms a protective oxide layer to enhance corrosion resistance and aesthetics.
Slitting and finishing
- Cutting the titanium foil to specified dimensions based on customer requirements.
- Inspecting the foil's thickness, surface quality, and physical properties to ensure compliance with specifications.
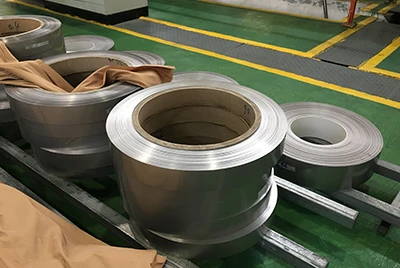
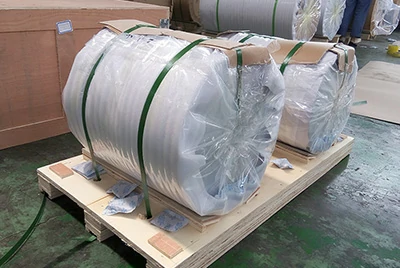
Packaging and shipping
Using moisture-proof and anti-corrosion packaging materials to ensure the titanium foil remains undamaged during transportation and storage.
Including test reports or certifications as per customer requirements.
How to choose the right titanium foil?
When purchasing titanium foil, selecting the appropriate type depends on specific application requirements. Refer to the following guidelines:
- For harsh corrosive environments, choose pure titanium (Grade 1, Grade 2).
- For high strength, high-temperature resistance, and fatigue performance, opt for titanium alloys like Grade 5 (Ti-6Al-4V).
- In the medical field, Grade 23 (Ti-6Al-4V ELI) is typically the best choice, especially for implantable devices and instruments.
- For enhanced aesthetics and corrosion resistance, select anodized or titanium-coated treatments.
- For reduced reflectivity and concealment, choose a matte finish.
- For high gloss and refined appearance, opt for a polished finish.
What factors affect the price of titanium foil?
Titanium alloy type: The composition ratio of different titanium alloys affects the cost. For example, grade 5 (Ti-6Al-4V) is more expensive than grade 2 pure titanium.
Thickness and size: Thinner or custom-sized titanium foil is usually more expensive. For instance, ultra-thin titanium foil with a thickness below 0.01mm costs more than the standard 0.05mm foil.
Surface treatment: Complex surface treatments increase costs. For example, embossed or polished titanium foil is more expensive than a standard matte finish.
Production process: High-precision manufacturing requires advanced equipment and technology. For example, high-precision titanium foil for aerospace applications is more costly than standard industrial-grade foil.
Order quantity and delivery time: Large-volume orders help reduce production costs. For example, ordering 1,000 kg of titanium foil at once has a lower unit price than ordering just 10 kg.
Market supply and demand: When demand is high and supply is tight, titanium foil prices rise. For instance, during peak periods in the aerospace industry, increased demand for titanium foil drives up prices.
What services can Chalco provide for you?
Customized production services
Provide titanium foil products of different specifications, thicknesses, and alloy types according to customer requirements, such as ultra-thin titanium foil (thickness less than 0.01mm) or specific alloys (e.g., Grade 5 or Grade 9).
Surface treatment services
Support various surface treatments, including polishing, sandblasting, oxidation, or embossing, to meet the aesthetic and functional needs of different industries.
Processing services
Offer precision processing services such as cutting, stamping, and welding to meet customers' specific requirements for titanium foil shape and size.
Technical support services
Provide titanium foil selection and application guidance, recommending the most suitable products based on customer usage scenarios, such as Grade 2 titanium foil for highly corrosive environments in the chemical industry.
Quality inspection services
Ensure that each batch of titanium foil undergoes rigorous quality testing, including thickness accuracy, surface flatness, and mechanical performance tests, to meet industry standards.
Environmental certification services
Provide products that comply with environmental and regulatory requirements, such as titanium foil certified under RoHS and REACH, meeting export and specific industry needs.
After-sales services
Offer comprehensive after-sales support, including product usage guidance, technical problem resolution, and complaint handling, ensuring customer satisfaction.
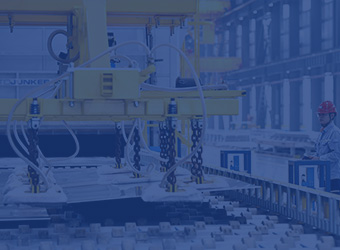