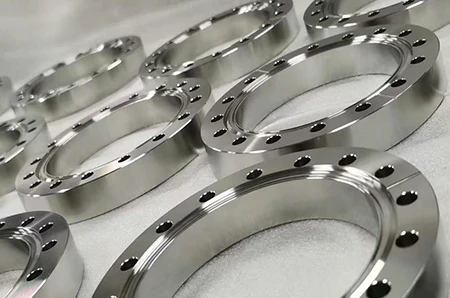
Titanium and Titanium Alloy Forging Supplier
Titanium forgings, with their high strength, light weight, high-temperature resistance, and excellent corrosion resistance, are an ideal choice for industries such as aerospace, medical equipment, and industrial manufacturing.
Whether it's forged rings, forged discs, forged bars, forged pipes, forged blocks, step shafts, or custom-forged shapes, we can meet your needs.
Focused on customized titanium forging solutions
- We offer a full range of titanium forgings based on customer requirements, including both custom single products and long-term bulk orders.
- We provide large-sized forgings as well as small forgings weighing only a few kilograms, flexibly meeting diverse needs.
- Quick response to order requirements, with some forgings delivered within one or two weeks.
- Years of titanium alloy processing experience ensure product quality and production efficiency.
- Focused on high-demand industries like aerospace, producing forged parts that meet strict flight standards.
Our professional team will provide you with the best solutions to help shorten development time, improve product performance, and reduce overall costs.
Popular forged titanium alloys
We provide customized titanium alloy services, adjusting composition, performance, and shape to meet the precise needs of various applications.
-
Commercially Pure Titanium (CP, Grades 1-4)
With excellent corrosion resistance, a balance of strength and toughness, and low density.
AMS 4921 ASTM B381 GB/T 16598 -
Ti-6Al-4V (Grade 5)
High strength-to-weight ratio, excellent fatigue resistance, corrosion resistance, and strong formability.
AMS 4928 AMS 4931 ASTM B381 MIL-T-9047 -
Ti-6Al-4V ELI (Grade 23)
Low interstitial elements, high toughness, excellent corrosion resistance, and biocompatibility.
AMS 6931 AMS 4928 -
Ti-5Al-2.5Sn
Outstanding high-temperature performance and creep resistance, adaptable to complex stress environments, extending part lifespan.
ASTM B381 MIL-T-9047 -
Ti-6Al-2Sn-4Zr-2Mo (6-2-4-2)
Excellent high-temperature strength and creep resistance, maintaining good mechanical properties under extreme temperature conditions.
AMS 4921 AMS 4965 -
Ti-10V-2Fe-3Al
One of the highest strength titanium alloys, with excellent heat treatment properties, performance can be controlled after forging.
AMS 4983
- Ti-5Al-2.5Sn(TA7)
- Ti-3Al-2.5V Grade 9
- Ti-10V-2Fe-3Al
- 5Al-2Sn
- Ti-0.2Pd Grade 7
- Ti-0.3Mo-0.8Ni Grade 12
Popular forged titanium products
we specialize in manufacturing custom titanium forgings, from forged rings and bars to die forgings. no matter the shape or alloy type, we can provide professional titanium forging solutions for you.Quick Quote
Titanium forged rings
The seamless rolling forging process reduces material defects, provides a smooth surface, and lowers subsequent processing costs.
Our forged rings have excellent mechanical properties, able to withstand harsh working conditions with high torque, high pressure, and high fatigue loads.
Diameter: 6 inches - 110 inches
Thickness: Up to 30 inches
Weight: Up to 55,000 pounds
Contact us now
Titanium forged discs (forged cakes)
The upset forging process is used to evenly compress the short discs, refining the central grain structure and significantly improving impact resistance and fatigue performance.
Further processing on a ring mill can be done as needed to achieve a smooth surface and precise angles.
Diameter: 3 inches - 124 inches
Thickness: 2 inches - 20 inches
Weight: Up to 60,000 pounds
Contact us now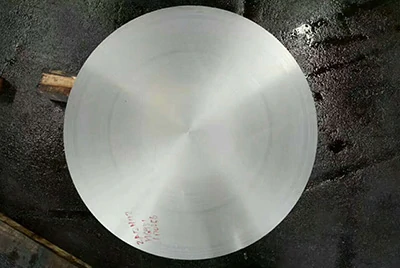
Titanium forged tubes (forged hollow tubes)
We can produce hollow components with special geometries and structures according to customer requirements, such as square or asymmetrical outer diameter forged tubes with holes.
Diameter: Up to 50 inches (1,270 mm)
Thickness: Up to 30 inches (762 mm)
Weight: Up to 55,000 pounds (24,947 kg)
Contact us now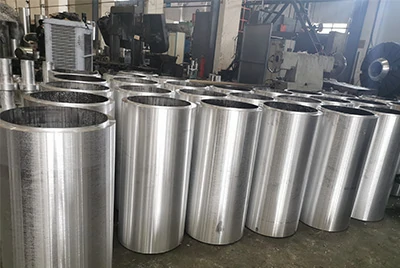
Titanium forged bars
We can provide titanium forged bars in almost any specific size and length.
Diameter: 1/2 inch to 45 inches
Custom Lengths: Up to 430 inches
Weight: Up to 77,000 pounds
Contact us now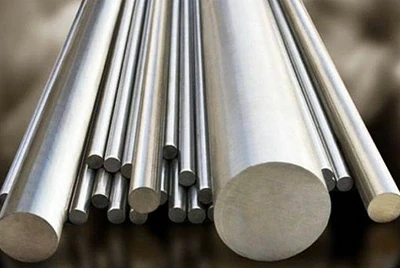
Titanium forged plates
We offer various surface treatment options, including forged surfaces, rough machining, and grinding, ensuring the structural integrity and high quality of the forged plates with a compression area ratio of at least 3:1.
Thickness: Up to 20 inches
Width: Up to 36 inches
Length: Up to 240 inches
Maximum Weight: 20,000 pounds
Contact us now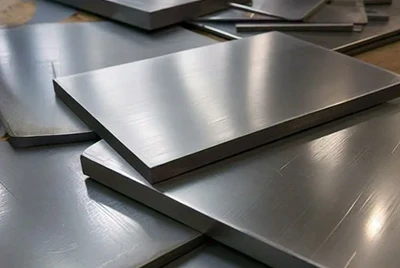
Titanium forged blocks
All forged blocks undergo ultrasonic testing to ensure strong internal structure.
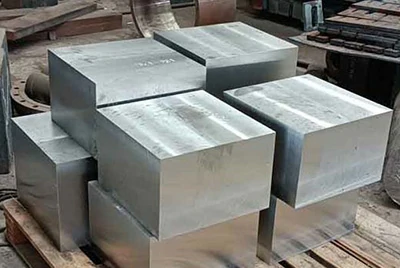
Large monolithic forgings
Our unique titanium alloy large monolithic forging technology transforms traditional multi-piece assemblies into integrated structural components, enhancing the forging’s structural efficiency and safety reliability.
We specialize in large monolithic forgings, ensuring precision and performance through advanced processes, with flexible transportation for large dimensions.
Contact us now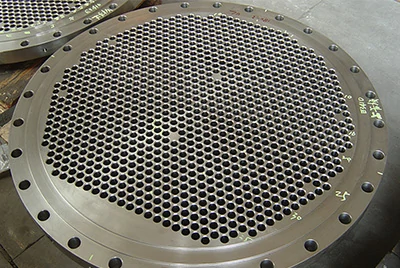
- BT22 alloy large forgings are used in the fuselage and landing gear of aircraft such as the Su-27 (SU27), Il-76 (IL76), Il-86 (IL86), Il-96 (IL96), An-124 (A124), and Tu-204 (TU204).
- Ti1023 alloy large forgings, up to 7 meters in length, are used for the main landing gear of the Airbus A380.
- The landing gear of the Boeing 777, using T1023 alloy large forgings, results in a structural weight reduction of approximately 270 kg.
- The Ti6Al4V alloy monolithic frame forging for the F-22 fighter jet, measuring 3.8 meters in length, 1.7 meters in width, and weighing 1590 kg.
Precision forging parts
Precision forging reduces the need for subsequent machining, improving production efficiency and reducing costs.
Precision forging is typically used to produce parts with very strict dimensional requirements.
Contact us now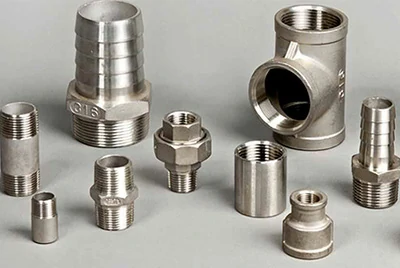
- The molds used in precision forging are usually finer, allowing for parts that are close to their final shape, significantly reducing the need for further processing.
- Precision forged parts typically have better surface quality and higher mechanical performance.
Forged titanium flanges
The function of a forged flange is to connect pipelines or equipment and ensure good sealing performance, withstanding pressure and physical stress in pipeline systems.
Size: Sch40 - Sch80
Type: SORF, BLIND, RFWN, etc.
Pressure: CL150, CL300, CL600, CL1500
Standard: ASME B16.5
Contact us now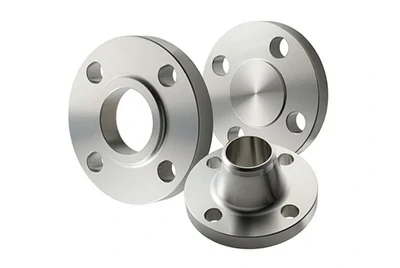
Forged step shafts
We offer rough-machined or fully machined step shafts to meet your specifications, along with value-added services such as heat treatment and machining, ensuring the product quality meets the highest standards.
Outer Diameter Range: 7 inches - 50 inches
Weight Range: Up to 77,000 pounds
Maximum Length: 205 inches
Contact us now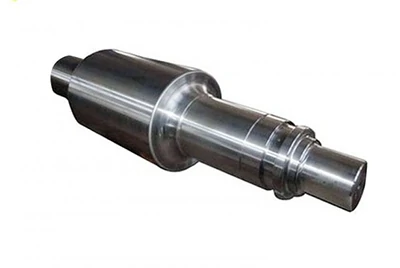
Titanium Die Forgings
Our die forgings are made using specialized tools to ensure compliance with customer drawings and technical requirements.
Whether standard parts or custom-made, we provide high-quality products.
Contact us now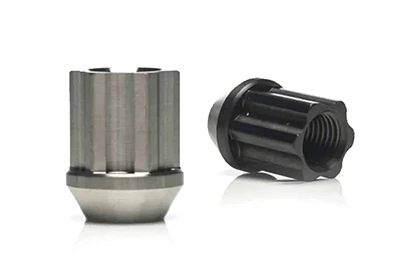
- The die forging process offers higher material density, stronger mechanical properties, and better precision.
- Die forgings can produce parts with complex shapes, ranging from simple circular or square forms to intricate geometries, all shaped using molds.
- Using near-net forming processes reduces subsequent machining requirements, improving product dimensional accuracy and consistency.
- The die forging process significantly enhances the strength, toughness, and fatigue resistance of the forgings by optimizing grain flow and microstructure, making it suitable for high-demand applications.
- Near-net forming greatly saves material, reduces machining time, and lowers production costs.
In addition to the products mentioned above, we also offer:
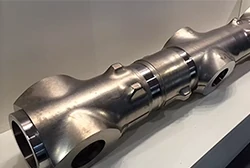
Forged Landing Gear
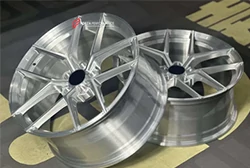
Forged Wheel Hubs

Forged Aircraft Blades
Titanium forging applications
Medical implants
Titanium alloys have excellent biocompatibility, allowing them to integrate well with human tissue and reduce immune rejection.
Contact us now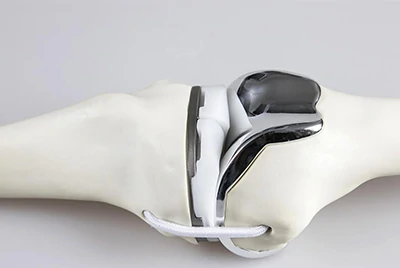
- Alloy Grades: Ti-6Al-4V, Ti-6Al-2Sn-4Zr-2Mo
- Applications: Bone screws, dental implants, hip joints
Aerospace components
Titanium forgings make up about 30% of the airframe weight and 40% of the engine weight, with many being critical parts.
Titanium alloy forged blades account for half of aerospace engine blades, favored for their high strength, crack resistance, and long lifespan.
Ti-6Al-4V alloy is used for precision forged blades in the Trent900 engine.
Titanium forgings offer a high strength-to-weight ratio, meeting the high-strength and low-weight requirements for aircraft landing gear and engine parts.
Contact us now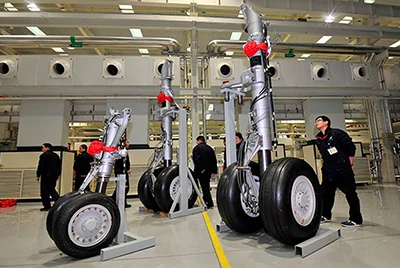
- Alloy Grades: Ti-6Al-4V (Grade 5), Ti-6Al-2Sn-4Zr-2Mo (6-2-4-2), Ti-5Al-2.5Sn
- Applications: Turbine discs, rear axle journals, blades, wing spars, landing gear, structural supports, high-strength nuts, bolts, and washers
Industrial machinery
In mining equipment, 12% to 24% of the structural weight comes from titanium forgings.
Titanium forgings are ideal for high-load, high-precision mechanical components, capable of withstanding wear and pressure from long-term use.
Contact us now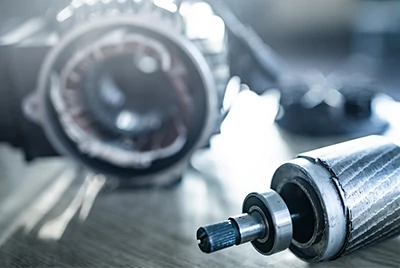
- Alloy Grades: Ti-6Al-4V, Ti-5Al-2.5Sn
- Applications: Bearings, high-strength fasteners, shafts
Sports equipment
The lightweight properties and strength of titanium alloys make them an ideal choice for high-performance sports equipment.
Contact us now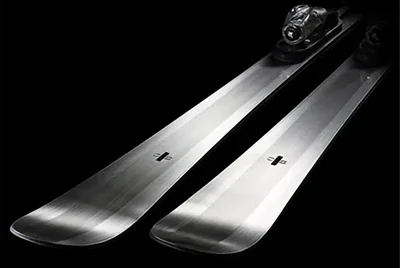
- Alloy Grade: Ti-6Al-4V
- Applications: Golf club heads, bicycle frames, ski poles
Marine hardware
The corrosion resistance of titanium alloys makes them excellent in marine environments, especially for marine hardware components that require resistance to seawater corrosion.
Contact us now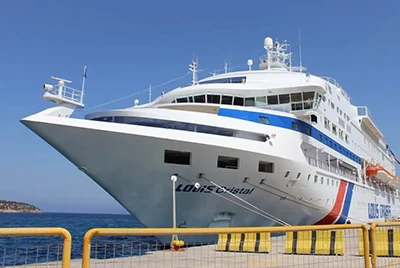
- Alloy Grades: Ti-6Al-4V, Ti-5Al-2.5Sn (TA7)
- Applications: Valves, propeller shafts, and accessories
Automotive components
Titanium forgings account for 17% to 19% of the structural weight in cars, with key components such as crankshafts, connecting rods, front beams, steering knuckles, half shafts, and transmission gears.
Titanium alloys' high-temperature and corrosion resistance make them ideal for automotive engines, exhaust systems, and other demanding components.
Contact us now
- Alloy Grades: Ti-6Al-4V, Ti-6Al-2Sn-4Zr-2Mo (6-2-4-2)
- Applications: Wheel hubs, turbocharger components, valves, exhaust systems
Chemical and petrochemical equipment
Titanium alloys offer exceptional acid, alkali, and corrosion resistance, making them ideal for harsh chemical environments.
Contact us now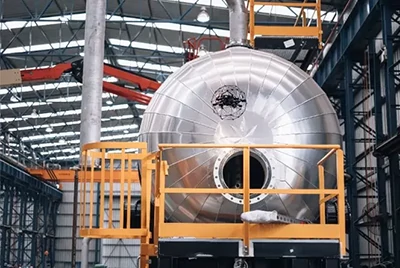
- Alloy Grades: Ti-6Al-4V, Ti-5Al-2.5Sn
- Applications: Pumps, valves, connectors, reactors, heat exchangers, piping systems
Military applications
In tanks, 60% of the structural weight comes from forgings.
Titanium forgings offer high strength, lightweight properties, excellent corrosion resistance, high-temperature stability, and fatigue and impact resistance.
Contact us now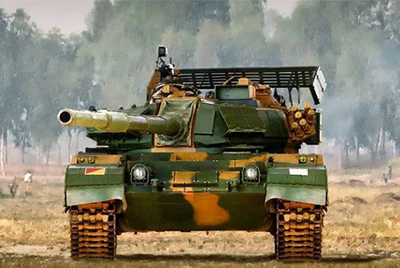
- Alloys: TA1, TA2, Ti-6Al-4V (TC4), Ti-10V-2Fe-3Al, Ti-6Al-2Sn-4Zr-2Mo, Ti-6242S
- Applications: Tank armor, turret supports, suspension systems, submarine hulls, propulsion shafts, rudder rods, missile engine casings, turbine blades, gun barrels, rails, high-strength fasteners
Advantages of titanium forgings
- Reduced Porosity: The forging process effectively reduces porosity in titanium forgings, enhancing material density and strength.
- Durability and High Strength: Titanium forgings offer exceptional strength and durability.
- High Performance: Forged titanium maintains outstanding performance even under extreme conditions.
- Enhanced Fatigue Resistance: The structural stability and strength of titanium forgings provide superior fatigue resistance and stability.
- Improved Toughness: The forging process increases the toughness of titanium, making it more resilient under impact or load.
Classification and characteristics of titanium forging processes
Titanium forging technology can be tailored to meet customer needs, and we are committed to providing customized solutions and high-quality titanium forgings to fully satisfy the diverse requirements of various industries.
Open die forging
- Suitable for the production of heavy or extra-large forgings.
- Simple process, low cost, and high flexibility.
Applications: Preparation of blanks for large mechanical parts, such as stepped rods, round or rectangular shapes.
Open mold forging
- No pre-cut contour in the mold; the movement of the workpiece is key.
- Suitable for producing large-sized or complex-shaped components, such as parts up to 80 feet in length.
- Can produce a wide range of forgings with flexible shapes.
Applications: Aircraft fuselage structures, ship parts, etc.
Closed mold forging
- The mold fully encloses the blank, and shaping occurs under pressure.
- No flash formation, suitable for high-precision forgings.
- High precision, high material utilization, and suitable for complex shapes.
Applications: Precision components, aerospace parts, etc.
Isothermal forging
- The mold and blank are kept at the same temperature to reduce flow stress.
- Suitable for high-precision and complex-shaped forgings.
- Low deformation force, high dimensional accuracy, and high material utilization.
Applications: Aircraft engine blades, aircraft structural components.
Segmental forging
- Processed in segments, with each processing cycle handling a part of the forging.
- Low equipment tonnage requirements, suitable for processing extra-large forgings.
Applications: Large monolithic forgings.
Extrusion forging
- Includes both forward and reverse extrusion methods, suitable for the production of hollow or solid components.
- High geometric accuracy and dense internal structure.
Applications: Valves, pipe fittings, and other high-precision components.
Multi-Directional forging
- The slider works alternately in both longitudinal and transverse directions, suitable for complex cylindrical parts.
- No flash formation, high material utilization, suitable for complex structures.
Applications: Cylindrical components, pressure vessels.
Superplastic forging, SPF
- Uses superplastic materials with fine grains, suitable for parts with complex shapes and large cross-sectional changes.
- High plasticity and strong shape complexity.
Applications: Complex aerospace components, medical devices, etc.
Special forging
- Uses specialized equipment, ideal for high-volume production of small parts such as screws.
- High efficiency and low production cost.
Applications: Fasteners, mechanical components, etc.
Comprehensive quality assurance for titanium forgings
We understand the critical role titanium forgings play in various high-performance scenarios. Rigorous quality inspection is our commitment to providing reliable products to our customers.
For more information or to discuss project requirements, please feel free to contact us! Quick Quote
- Dimensions and Shape: Using high-precision measurement tools such as Coordinate Measuring Machines (CMM) to ensure geometric dimensions and shapes meet drawing specifications.
- Surface Quality: Strict control of surface roughness, ensuring no cracks, dents, folds, or other defects, with necessary corrections made.
- Mechanical Performance Testing: Through hardness, tensile strength, yield strength, plasticity, and toughness tests, we ensure the forgings meet performance requirements.
- Non-Destructive Testing (NDT): Includes dye penetrant, ultrasonic, and radiographic testing to ensure both internal and external integrity of the product.
- Metallographic Analysis: Conducted by independent metallurgical laboratories to analyze microstructures, improving product performance and metallurgical understanding.
Processing services available for titanium forgings
We are committed to providing a full range of processing services to ensure that the forgings you receive are ready for immediate use.
- Heat Treatment: Through processes such as annealing, normalizing, and tempering, we improve the microstructure and mechanical properties of titanium forgings.
- Edge Cutting Services: Using precise cutting techniques, we ensure clean, smooth edges with no chipping on titanium alloy forgings.
- Straightening Services: We correct distortion and deformation that may occur during forging, cooling, and heat treatment processes using shape correction techniques.
- Vertical Turning: Suitable for finishing large-diameter forgings, ensuring high precision and surface quality.
- Horizontal Turning: Used for processing long shaft parts, ensuring dimensional consistency and mechanical performance.
- Milling: For processing flat surfaces or complex geometries, suitable for high-demand parts such as molds and fittings.
- Drilling & Deep Drilling: Providing hole machining for forgings, including deep drilling, ensuring products are suitable for specific applications.
- Boring: Enhances the dimensional accuracy and surface quality of holes.
- Surface Treatment: Offering sandblasting, polishing, anodizing, and other services to enhance the corrosion resistance and aesthetic quality of titanium forgings.
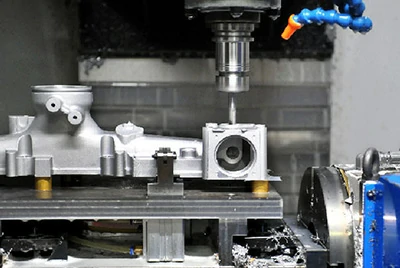
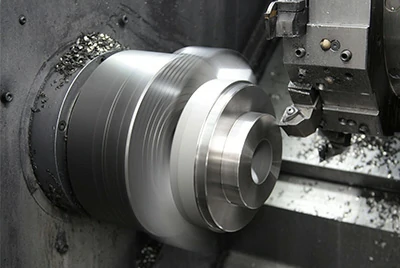
Titanium alloy forging technology drives quality leap
In the field of titanium alloy forging, we are always at the forefront of technology. Our research and development and production focus include:
- Precision Forging Technology for Complex Ultra-Thin Parts: Meets the demands for high-precision and highly complex components, significantly reducing the amount of subsequent machining.
- Near-Net Shape Forging Technology for Large Monolithic Parts: Reduces the need for component connections through monolithic forging, enhancing structural integrity and reliability.
- High-Reliability Forging Technology for Low-Cost Parts: Optimizes the process flow to provide solutions that balance performance and cost-effectiveness.
- New Material Forging Technology: Develops innovative alloy materials to meet customer requirements for extreme environments.
- Forging-Based Hybrid Manufacturing Technology: Combines multiple processing methods to achieve integrated complex shapes and functions.
- Intelligent Forging Technology: Achieves precise manufacturing and efficient production through numerical simulation, forging knowledge systems, and automated production lines.
Professional titanium forging equipment
With world-leading equipment and professional forging technology, we provide high-performance, high-precision titanium forgings and other forged products to our customers.
- We have advanced forging equipment, including air hammers, hydraulic presses, quick forging machines, and precision forging machines, capable of meeting the diverse production requirements for both small and large-sized forgings.
- Presses: We have presses ranging from 2,000 tons to 65,000 tons, suitable for processing various materials such as bars, die forgings, and powder parts.
- Hammers: Equipped with multiple hammering devices ranging from 2,000 to 4,000 pounds, enabling rapid response to high-strength parts forging needs.
- Ring Rolling Mill: Supports seamless ring rolling production with diameters up to 120 inches, meeting the processing needs for large-sized products.
Titanium forgings: long-term value for high-performance investment
Components of titanium forging pricing
- Material Costs: Raw materials such as titanium sponge are expensive, and their production process is complex and energy-intensive, which is key to ensuring material performance.
- Processing Costs: The production of titanium forgings requires high-temperature, high-precision equipment and specialized technical teams. The complex processes ensure the product meets the highest industry standards.
- Forging Energy Consumption: The energy cost per pound of titanium alloy forging ranges from $0.10 to $0.50, with high-temperature forging requiring a constant heating environment.
- Vacuum Arc Remelting (VAR) Costs: Vacuum remelting furnaces are expensive and technologically complex.
Long-term value of titanium forging
- High Performance and Durability: Titanium forgings, with their high strength, corrosion resistance, and high-temperature durability, can be used for extended periods in extreme environments.
- Cost-Effectiveness: While the initial cost is high, the outstanding performance of titanium forgings makes them ideal for demanding applications in critical fields, offering greater value returns to customers.
Flexible pricing support for customers
- Bulk Discounts: Discounted prices based on order volume, helping customers reduce per-piece costs.
- Staged Delivery: Flexible production arrangements to reduce customers' one-time purchasing pressure.
- Material Optimization Suggestions: Recommending the most economical and suitable alloys based on actual needs, helping customers control costs while ensuring performance.
Are You Looking for a Titanium Supplier?
If you need a professional titanium supplier to provide you with high-quality, cost-effective titanium, we will be your best choice.
Titanium forging packaging and shipping: ensuring quality and delivery
- Reinforced Frame Packaging Design: Large and irregularly shaped forgings are packaged with reinforced structures to prevent deformation during transportation.
- Modular Packaging Solutions: For particularly large forgings, we offer split packaging, allowing the parts to be assembled upon arrival at the destination.
- Strict Pre-shipping Inspection: Prior to shipping, we conduct a thorough inspection to ensure secure packaging, clear labeling, and purchase full transport insurance to reduce customer risk.
- Flexible Delivery Options: From door-to-door (DAP) to customer pickup (EXW), we cater to the diverse needs of customers in different regions.
From individual forgings to full container shipments, we provide competitive pricing for global transportation, covering major markets including North America, South America, Europe, and Asia.Quick Quote
Comparison of titanium forgings with other titanium products
Titanium forgings
- Extremely High Strength: The forging process enhances the structural strength of titanium, making it suitable for high-load, high-performance applications.
- High Temperature and Corrosion Resistance: Especially suitable for high-temperature and corrosive environments, widely used in aerospace, energy, automotive, and other industries.
- Customizable Sizes and Shapes: Titanium forgings can be tailored to customer specifications in terms of size, shape, and alloy to meet various special requirements.
Titanium castings
- Suitable for Complex Shapes: Can manufacture complex and irregularly shaped parts, ideal for large-scale production.
- Low Cost: Casting is relatively inexpensive compared to other manufacturing methods, making it suitable for mass production.
- Wide Application: Suitable for large components such as flanges, pipe fittings, etc.
Titanium extrusions
- High Precision and Good Surface Quality: Ideal for parts requiring high precision and smooth surfaces, reducing the need for further processing.
- No Welding Defects: The extrusion process avoids defects that might arise from welding, ensuring stable part quality.
- Suitable for Bars, Tubes, and Sheets: Ideal for producing long bars, tubes, or sheet parts, such as shafts, frames, and pipes.
Titanium powder processed parts
- High Flexibility: Suitable for complex shapes and small-batch production, capable of producing miniature or custom-shaped parts.
- Material Savings: Powder metallurgy reduces material waste, ideal for high-precision applications.
- High Precision: Extremely high precision, suitable for industries such as medical and aerospace, where precision is critical.
Titanium forging knowledge
Titanium forging process
- Material Selection: High-quality titanium alloys, such as Ti-6Al-4V, are selected for forging due to their excellent properties.
- Billet Preparation: The initial form of titanium alloy is typically a billet. This billet is usually preheated to an appropriate temperature to enhance its ductility.
- Heating: The billet is heated to the forging temperature to increase its ductility, making it easier to process.
- Forging: The heated billet is placed in a forging press or hammer, where high pressure is applied. The applied force shapes the titanium alloy into the desired form.
- Cooling: After the forging process, the titanium alloy part is typically gradually cooled to room temperature.
- Heat Treatment: Depending on the application, the forged titanium part may undergo additional heat treatment processes to optimize its strength, hardness, and durability.
- Finishing: The forged titanium part may undergo additional machining, surface treatment, or quality control processes to ensure it meets the required specifications.
Protective coatings in titanium forging process
During the forging heating process, it is essential to protect titanium and titanium alloys from contamination by oxygen, nitrogen, hydrogen, and carbon.
- Liquid Glass Coating: The most commonly used coating. It forms a sticky surface while providing lubrication, promoting metal flow.
- Molybdenum Disulfide Coating: Reduces adhesion on forging dies, decreases friction, and extends the die life.
- Graphite Coating: Minimizes friction, prevents oxidation during the forging process, and improves forging efficiency.
- Boron Nitride Coating: Provides high-temperature lubrication, prevents material from adhering to the die, and enhances processing quality.
- Zirconium Coating: Increases die life with excellent oxidation resistance, suitable for high-temperature forging.
- Ceramic Coating: Improves tool durability with outstanding oxidation resistance properties.
- Titanium Dioxide Coating: Helps reduce friction and provides some level of oxidation protection.
Key factors affecting the microstructure and properties of titanium forgings
The microstructure and mechanical properties of titanium and titanium alloy forgings are primarily determined by process parameters such as deformation temperature, deformation degree, deformation speed, post-forging cooling rate, and heat treatment.
Deformation temperature
The temperature directly affects the flowability and plasticity of the metal during the forging process.
- Too low temperature: Poor plasticity, prone to cracking.
- Too high temperature: Causes overburning of the material or grain coarsening, affecting mechanical properties.
- Die temperature: Must match the temperature of the raw material. Excessive temperature differences can lead to thermal stress and defects.
Deformation degree
Refers to the amount of plastic deformation occurring during the forging process.
- Insufficient deformation: Unable to break down the cast structure in the material, making it difficult to achieve a uniform grain structure.
- Excessive deformation: May cause internal cracks or stress concentrations in the material.
Deformation speed
The deformation speed determines the flowability of the metal in its plastic state.
- Too fast: Prone to internal cracks or surface defects.
- Too slow: May cause localized cooling, leading to uneven deformation and degraded performance.
Cooling speed
Cooling rate affects the microstructure and residual stress of the forging.
- Fast cooling: Can increase internal stresses, making the material prone to cracks or distortion.
- Slow cooling: Helps relieve stress but may lead to grain coarsening or performance degradation.
Heat treatment
The effect of heat treatment on titanium and titanium alloys is limited, typically used for relieving residual stress and fine-tuning mechanical properties.
- Annealing: Improves toughness and eliminates internal stresses.
- Aging: Enhances the material's strength and fatigue resistance.
Comprehensive control of process parameters
During the forging process, forging temperature, die temperature, degree of deformation, and deformation speed must be coordinated to ensure the material has a uniform grain structure and stable properties.
Cracking issues in titanium alloy forging
End-face cracking is a common type of crack that occurs on the end face of the billet during titanium alloy forging. These cracks are usually large and severe, which can prevent the forging process from continuing normally.
Main Causes of Cracking:
- Incompletely removed shrinkage cavities or cold shuts at the head or tail of the ingot, leading to cracks during processing.
- Excessive heat absorption during the upsetting process when the billet's end face contacts the hammer or die, causing the end face temperature to drop too quickly.
- Rapid cooling of the billet's end face during elongation, which leads to material hardening and increased susceptibility to cracking.
- Uneven compression on the end face in different directions, causing stress concentration and crack formation.
- High deformation resistance and poor flowability of certain billets, leading to concave deformation in the center of the end face, which forms the source of the crack.
By strictly controlling materials, ensuring uniform heating, using scientific deformation speeds, and optimizing the process, end-face cracking can be effectively prevented, improving the quality of the forgings and production efficiency.
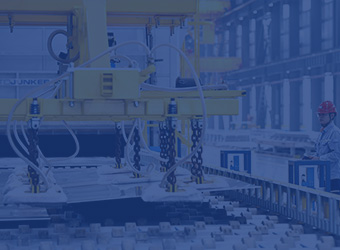