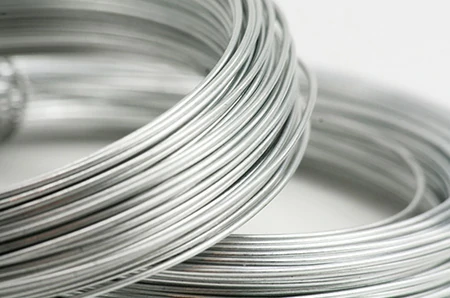
Titanium wire & Titanium Welding Wire Manufacturer
Titanium Wire, as a lightweight and high-strength metal wire, is gradually being widely used across various industries due to its excellent corrosion resistance, biocompatibility, high strength-to-weight ratio, and non-magnetic properties. It is gradually replacing traditional materials such as stainless steel and aluminum.
Chalco supplies products including commercially pure titanium wire, titanium alloy wire, nitinol wire, medical-grade titanium wire, titanium welding wire, and titanium welding rods, which are widely applied in industries such as aerospace, medical, automotive, and chemical fields.
Quick View:
Titanium Wire Introduction
Composition: | Pure Titanium Wire | Titanium Alloy Wire | Nitinol Wire |
Applications: | Medical Titanium Wire | Titanium Wire for Eyeglasses | Suspension Titanium Wire |
Shapes: | Titanium Round Wire | Titanium Flat Wire | Titanium Square Wire | Custom Shaped Titanium Wire |
Surface: Pickled Surface, Bright Surface
State: Hot Drawn Titanium Wire, Cold Drawn Titanium Wire, Annealed Titanium Wire
Supply: Straight Titanium Wire, Spool Titanium Wire, Coiled Titanium Wire
Standards: ASTM B863, AWS A5.16, ASTM B348, ASTM F67, ASTM F136
Production Range of Titanium Wire
Titanium Wire Sizes and Supply Types
Diameter (mm) | Diameter (inches) | Coil | Spool | Straight |
---|---|---|---|---|
0.05 - 0.78 | 0.002 - 0.031 | Yes | Yes | No |
> 0.78 - 3.25 | > 0.031 - 0.128 | Yes | Yes | Yes |
> 3.25 - 6.00 | > 0.128 - 0.236 | Yes | No | Yes |
Titanium Wire Specification Standards
ASTM B863 | AWS A5.16 | UNS | AMS |
---|---|---|---|
Gr1 | ERTi 1 | R50100 | AMS4951 |
Gr2 | ERTi 2 | R50120 | AMS4951 |
Gr3 | ERTi 3 | R50125 | AMS4951 |
Gr4 | ERTi 4 | R50130 | AMS4951 |
Gr5 | ERTi 5 | R56400 | AMS4954 |
Gr7 | ERTi 7 | R52401 | - |
Gr9 | ERTi 9 | R56320 | - |
Gr23 | ERTi 23 | R56408 | AMS4956 |
Bare Titanium Wire
Pure Titanium Wire
Made of pure titanium, it offers excellent corrosion resistance and biocompatibility, commonly used in medical implants, aerospace components, and eyeglass frames, among others.
Contact us now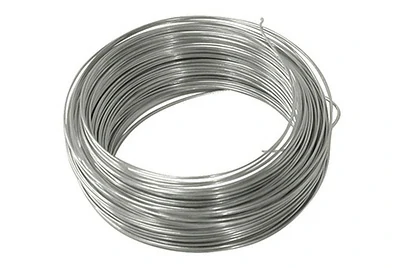
Hot Selling Products
-
Grade 1 Titanium Wire
The softest grade of pure titanium, with excellent ductility for easy cold forming and welding. Ideal for medical implants and chemical equipment.
-
Grade 2 Titanium Wire
The most commonly used grade of pure titanium, balancing strength and ductility, ideal for applications that require excellent corrosion resistance.
-
Grade 3 Titanium Wire
Stronger than Grade 1 and Grade 2, but with slightly lower ductility, it is suitable for aerospace and marine applications.
-
Grade 4 Titanium Wire
The strongest grade with low ductility, ideal for high-strength, corrosion-resistant applications in aerospace and medical fields.
Titanium Alloy Wire
Titanium alloy wire is made by adding elements like aluminum, vanadium, and molybdenum to pure titanium, improving strength, hardness, and high-temperature resistance. It is widely used in aerospace, medical, automotive, and chemical industries requiring high-performance materials.
Contact us now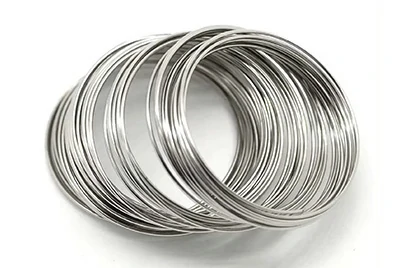
Hot Selling Products
-
Grade 5 Titanium (Ti-6Al-4V) Wire
Features: Also known as 6-4 titanium alloy, it combines high strength, excellent toughness, and fatigue resistance.
Applications: Widely used in aerospace, medical devices, and sports equipment.
UNS R56400 AMS 4928 ASTM B863 -
Grade 23 Titanium 6Al-4VEli Wire
Features: The ELI (Extra Low Interstitial) version contains extremely low levels of interstitial elements (such as oxygen, nitrogen, carbon), greatly improving ductility and fracture toughness.
Applications: Mainly used for medical implants, meeting strict requirements for material safety and reliability.
UNS R56407 ASTM B863 -
Grade 9 Titanium 3Al-2.5V Wire
Features: This alloy has excellent corrosion resistance and maintains stable performance over a wide temperature range.
Applications: Suitable for aerospace and industrial applications requiring high environmental resistance.
UNS R56322 ASTM B863 -
Titanium 6-2-4-2 Wire UNS R54620 UNS R54621
Features: Offers good high-temperature strength and creep resistance.
Applications: Commonly used in aerospace and other fields requiring stable performance in high-temperature environments.
UNS R56260 ASTM B863 -
Titanium 6-2-4-6 Wire
Features: An α+β titanium alloy, it can be further improved by heat treatment.
Applications: Considered one of the main alloys in the titanium industry, widely used in aerospace, marine engineering, and energy fields.
ASTM B863 -
Grade 12 Ti-0.3Mo-0.8Ni Titanium Wire
Features: Known for excellent corrosion resistance, especially in marine environments. Its resistance is between Ti-50A and Ti-0.2Pd alloys, with outstanding resistance to nitric and chromic acids.
Applications: Mainly used in marine engineering equipment like ships, submarines, and subsea detectors, as well as seawater desalination heat exchangers, replacing the higher-cost Ti-0.2Pd alloy.
UNS R52400 ASTM B863 -
Grade 21 Beta 21 S Titanium Wire
Features: Known for its excellent oxidation resistance.
Applications: Especially suitable for aerospace applications, meeting requirements for use in high-temperature and harsh environments.
ASTM B863 -
Titanium 15-3-3-3 Wire
Features: A metastable β titanium alloy, it offers good cold formability and heat treatability.
Applications: Commonly used in aerospace and other fields, suitable for the production of high-performance structural components.
ASTM B863 -
Titanium 0.2 Pd Wire
Features: Offers exceptional corrosion resistance, especially in chloride environments. Its corrosion resistance is better than Ti-50A alloy, making it ideal for highly corrosion-resistant applications.
Applications: Widely used in marine engineering, chemical equipment, seawater desalination equipment, and other fields.
ASTM B863 -
Ti-8Al-1Mo-1V Titanium Wire
Features: A near-α alloy designed for high-temperature applications, it has a high modulus and low density, while maintaining excellent creep strength.
Applications: Suitable for applications that require both lightweight and high-temperature stability.
ASTM B863 -
Beta C (Titanium Grade 19)
Features: As a β titanium alloy, it offers good cold formability and medium strength.
Applications: Suitable for various industrial applications, ensuring both machinability and adequate structural strength.
ASTM B863
Nitinol Wire
Nitinol is a shape memory alloy (SMA) of nickel (Ni) and titanium (Ti), known for its shape memory effect (SME) and superelasticity. It is widely used in satellite antennas, medical guidewires, eyeglass frames, and orthodontic wires.
Contact us now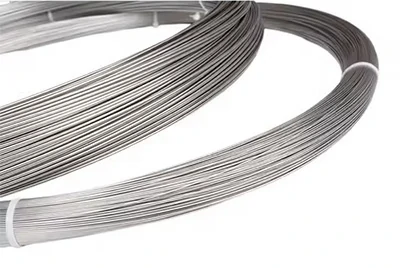
Core Features
- Shape Memory Effect: When heated to the critical temperature (austenite phase transition temperature), the material returns to its original shape.
- Superelasticity: Can withstand large deformations at room temperature and return to its original shape without permanent plastic deformation.
- Biocompatibility: Suitable for medical implants.
- Corrosion Resistance: Performs excellently in bodily fluids or harsh environments.
Hot Selling Products
-
Nitinol 55(Ni-55wt% Ti)
A near-equiatomic formula (about 55% nickel) with excellent shape memory and superelasticity. Adjustable transition temperature (-50°C to 100°C), widely used in medical and consumer fields.
-
Nitinol 60(Ni-60wt% Ti)
With higher nickel content, it enhances corrosion resistance and hardness, but has a weaker shape memory effect, ideal for high-wear applications (e.g., industrial valve seals).
-
Nitinol 70(Nitinol 70)
Contains 70% nickel, providing excellent shape memory and high strength. Used in automotive manufacturing, such as engine valve springs, shock absorbers, and transmission components.
-
Nitinol SE508(ASTM F2063)
Medical-grade compliant, with excellent biocompatibility and adjustable transition temperature (-20°C to 40°C). Commonly used for vascular stents, orthopedic devices, and dental wires.
-
Nitinol LT (Low-Temperature Type)
Low transition temperature (Af: -30°C to 0°C), ideal for low-temperature environments, like seals, cooling system valves, and polar equipment.
-
Nitinol HT(High-Temperature Type)
High transition temperature (Af: >100°C), strong heat resistance, and stability. Commonly used in aerospace engine components, high-temperature sensors, and industrial automation.
Application Fields
- Medical: Stents, guidewires, orthodontic archwires (utilizing superelasticity).
- Aerospace: Deformable wings, satellite antennas (using shape memory effect).
- Industrial: Smart valves, connectors, shock-absorbing structures.
- Consumer Electronics: Eyeglass frames, mobile phone antennas.
Medical Titanium Alloy Wire
Medical titanium alloy wire meets ASTM F67 and ASTM F136 standards, offering excellent biocompatibility and corrosion resistance. It is commonly used for medical implants, orthopedic instruments, and dental tools.
Diameter: 0.1mm - 5mm
Standards: ASTM F67, ASTM F136, ISO 5832
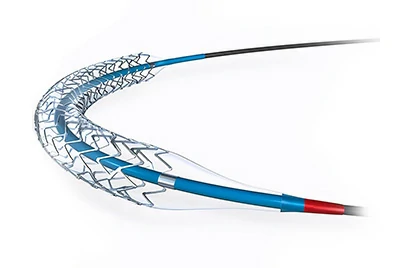
Core Features
- Biocompatibility: Non-toxic, non-sensitizing, and compatible with human tissue for long-term use.
- Corrosion Resistance: Excellent corrosion resistance in bodily fluids.
- Mechanical Properties: High strength, low density, and an elastic modulus close to human bone (reducing stress shielding effects).
- Workability: Can be drawn into different diameters to meet the needs of fine medical instruments.
Hot Selling Products
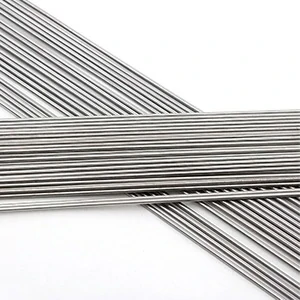
Gr1 Titanium Wire - Low Strength, High Ductility
Best corrosion resistance, used in non-load-bearing applications (e.g., sutures, dental restoration wires).
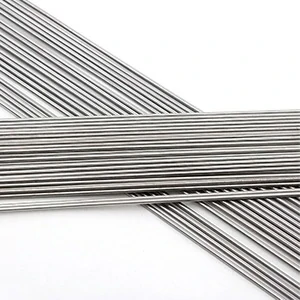
Gr4 Titanium Wire - High Strength
Tensile strength up to 550 MPa, used in small bone screws, dental implants guide wires.
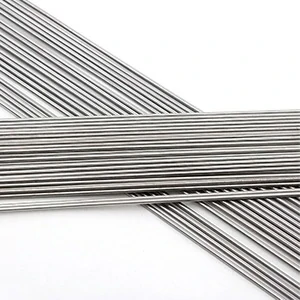
Gr23 Ti-6Al-4V ELI Titanium Wire - ASTM F136
Low elastic modulus (approx. 110 GPa), similar to human bone (10-30 GPa), reduces stress shielding. Used in orthopedic implants (e.g., spinal fixation wires, bone plates), and joint replacement parts.
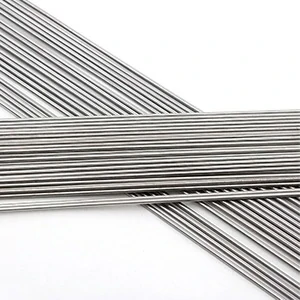
Ti-6Al-7Nb Titanium Wire
Substitutes niobium (Nb) for vanadium (V) to avoid potential toxicity concerns, providing higher biocompatibility. Strength similar to Ti-6Al-4V, used for long-term implants (e.g., cardiovascular stent wires, bone repair meshes).
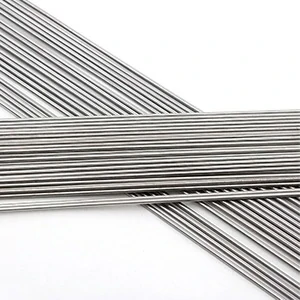
Ti-5Al-2.5Fe Titanium Wire - ASTM F2146
Iron (Fe) replaces part of vanadium (V), offering lower cost and moderate strength (tensile strength ~700 MPa). Used in non-load-bearing devices (e.g., endoscope guidewires, surgical suturing needles).
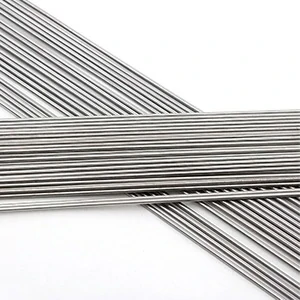
Ti-15Mo Titanium Wire
Ultra-low elastic modulus (55-80 GPa), further matching bone mechanical properties. Contains molybdenum (Mo), offering excellent fatigue resistance. Used in dynamic load applications (e.g., elastic intramedullary nails, biodegradable instrument support structures).
- Structural support
- High strength
- Low modulus
- Shape-changing functionality
- Superelasticity
- Shape memory
In general, medical titanium alloy wire is used in static or low deformation scenarios (e.g., bone plates, screws), while Nitinol wire is used in dynamic adaptive scenarios (e.g., vascular stents, orthodontic archwires).
Titanium Alloy Wire for Eyewear
Titanium alloy wire for eyewear is a lightweight, hypoallergenic, and highly corrosion-resistant material made from titanium (Ti) or titanium alloys, specifically designed for eyeglass frames.
Standards: ISO 21987, ISO 12870
Contact us now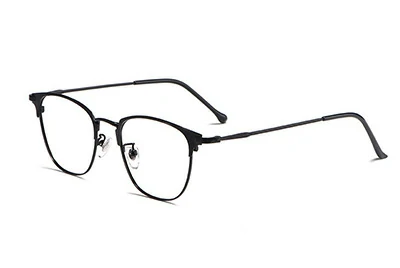
Core Advantages
- Ultra-lightweight: The density is only 60% of steel, ensuring comfortable wear.
- Corrosion-resistant: Resistant to sweat, cosmetics, and other daily corrosion, ensuring a long service life.
- Biocompatibility: Low allergenicity, suitable for sensitive skin.
- High elasticity: Can be bent without breaking, adaptable to complex frame designs.
- Surface treatment: Easy to plate, polish, and achieve various colors (e.g., IP vacuum ion plating).
Hot Selling Alloys
-
Pure Titanium Wire Gr1, Gr2
High purity, excellent ductility, balances lightweight and durability.
Full frame glasses Temples -
β Titanium Alloy Wire Ti-3Al-2.5V, Ti-4.5Al-3V-2Mo-2Fe
Low elastic modulus, high tensile strength, and bendable without deformation.
Spring hinges for temples Rimless frames -
Nitinol Alloy Wire Ni-55% Ti
Shape-memory effect: Heats and returns to preset shape (e.g., self-adjusting temple angles).
Adjustable temples Folding frames -
Titanium Composite Wire Titanium-clad steel/plastic
Coated with stainless steel or polymer; corrosion resistance and color diversity.
Fashionable frames
Material Recommendations
- Daily wear: Pure titanium (Gr2) offers high cost-effectiveness, resistant to sweat corrosion.
- Sports/Outdoors: β titanium alloy or memory titanium, impact-resistant.
- High-end customization: Pure titanium + IP coating, offering a luxurious feel (e.g., champagne gold, gunmetal grey).
Titanium Alloy Wire for Suspension
Made from titanium (Ti) or titanium alloys, designed for hanging, bearing, or fixing applications, such as laboratory suspension devices, spacecraft components, deep-sea equipment ropes, and bridge shock-absorbing cables.
Diameter: φ0.2-8.0mm
Standards: ASTM B863, ISO 5832, GB/T 3623
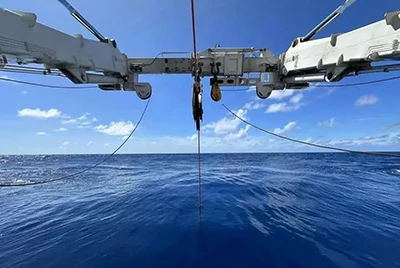
Core Features
- High strength and lightweight: Titanium's density is only 60% of steel, but its strength is comparable to or even exceeds some steel alloys, making it suitable for high-load scenarios.
- Corrosion resistance: Resistant to seawater, chemical media, and other corrosive environments, ideal for marine, chemical, and harsh environments.
- Fatigue resistance: Resistant to breakage under repeated loads, suitable for long-term dynamic suspension applications.
- Processing adaptability: Can be produced in different diameters and conditions (annealed, cold-worked), catering to diverse suspension needs.
Hot Selling Alloys
-
Grade 1 Pure Titanium Wire
Strength: Lowest (tensile strength ≥ 240MPa), great ductility and formability, easy to process into fine wire. Ideal for light-load suspension (e.g., lab devices).
-
Grade 2 Pure Titanium Wire
Moderate strength (tensile strength ≥ 345MPa), excellent corrosion resistance, suitable for medium-load marine suspension devices or chemical pipeline supports.
-
Ti-6Al-4V Titanium Alloy Wire
Alpha + Beta alloy, tensile strength ≥ 860MPa, excellent temperature resistance. Ideal for high-temperature, high-load use (e.g., spacecraft suspension, deep-sea ropes).
-
Ti-3Al-2.5V Titanium Alloy Wire
Strength between Grade 2 and Grade 5 (tensile strength ≥ 620MPa), better cold working than TC4, ideal for thin-walled suspension (e.g., aerospace supports).
-
Ti-0.3Mo-0.8Ni Titanium Alloy Wire
Better corrosion resistance than pure titanium, resistant to crevice corrosion, ideal for chemical equipment suspension or cables in corrosive environments.
-
Ti-15Mo Titanium Alloy Wire
High elastic modulus (around 110GPa), fatigue resistance, and excellent high-temperature oxidation, ideal for dynamic suspension (e.g., bridge shock cables, robot arm wires).
Customized Titanium Wire in Various Shapes
Titanium Round Wire
We offer precision titanium round wire in a variety of alloys and surface treatments, catering to the diverse needs of different industries.
Diameter: 0.040" - 0.200" (1.016mm - 5.08mm)
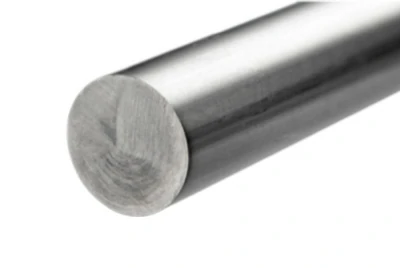
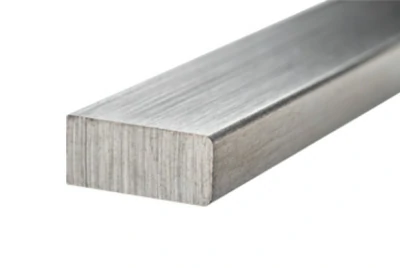
Titanium Flat Wire
Using advanced drawing technology, we can flatten round titanium wire to produce flat wire with strict tolerance requirements.
Thickness: 0.0005" - 0.250" (0.0127mm - 6.350mm)
Width: 0.001" - 1.50" (0.0254mm - 38.46mm)
Titanium Square Wire
Titanium square wire is typically made by drawing titanium round rods through molds or flattening them during the rolling process. It is widely used in industries such as aerospace, oil, and natural gas.
Size: 0.0005" - 0.250" (0.0127mm - 6.350mm)
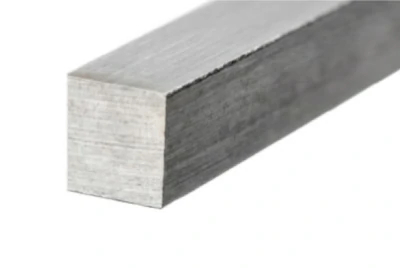
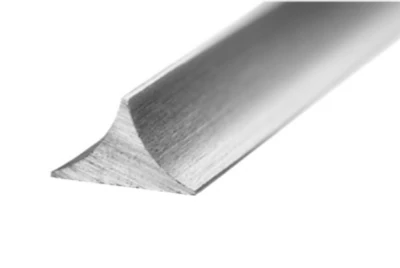
Customized Titanium Profile Wire
Equipped with advanced profile wire mills, we can produce custom-shaped wires with tight tolerances for any application.
Thickness: 0.0005" - 0.335" (0.12mm - 8.509mm)
Width: 0.035" - 1.50" (0.89mm - 38.46mm)
Profile Wire Shape Display
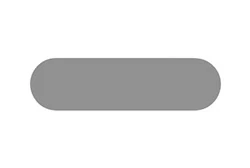
Rolled Flat Titanium Wire
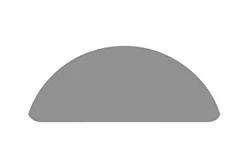
D-Wire (Half, Large, Small)
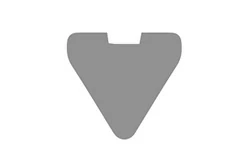
60°Keyway Triangle Titanium Wire
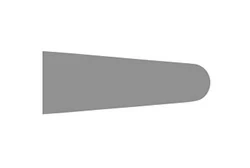
Wedge Titanium Wire
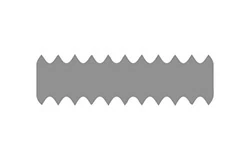
Serrated Shape Titanium Wire
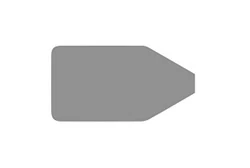
Bevel Titanium Wire
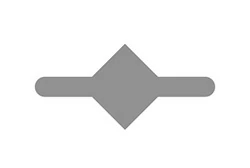
Star Titanium Wire
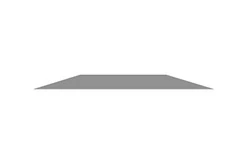
Blade Titanium Wire
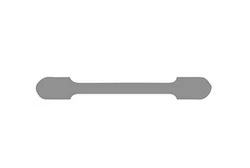
Dog Bone Titanium Wire
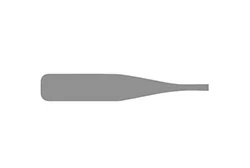
Seal Strip Titanium Wire
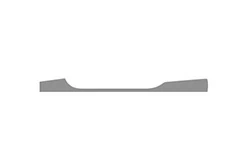
Multi-Gauge Strip Titanium Wire

Symmetric & Asymmetric Vanes Titanium Wire
We can offer customized services for a wide range of high-precision nickel-titanium alloy wires, adapting to innovative designs in fields such as medical devices, wearable technology, and precision instruments.Quick Quote
Titanium Welding Wire
Titanium welding wire (Titanium Filler Rod/Wire) is a filler material used for welding titanium and titanium alloys, typically made from pure titanium or titanium alloys, with chemical composition and mechanical properties that match the base material. It is widely used in high-precision welding processes such as inert gas shielded welding (e.g., TIG, MIG) and laser welding, ensuring weld strength, corrosion resistance, and high-temperature stability.
Types of Titanium Welding Wire
Titanium Filler Rod
Titanium filler rods are mainly used for TIG welding, with larger diameters, suitable for manual welding and thick plate welding. They are flexible in operation and produce high-quality welds.
Diameterh: 1.6mm - 4.8mm
Applications: Aerospace, chemical equipment, shipbuilding

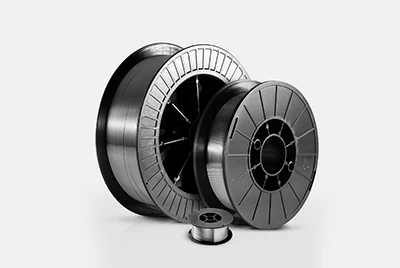
Titanium Welding Wire
Titanium welding wire is a versatile welding filler material, suitable for various welding processes such as TIG, MIG, etc.
Diameter: 0.8mm - 2.4mm
Types: Straight wire, coiled wire
Applications: Industrial piping, medical devices, automotive parts
Titanium TIG Wire
Titanium TIG welding wire is designed specifically for TIG welding, with a smooth surface and uniform diameter, ensuring arc stability and weld formation quality, commonly used in high-precision welding.
Applications: Precision instruments, aerospace engine components, nuclear reactor equipment
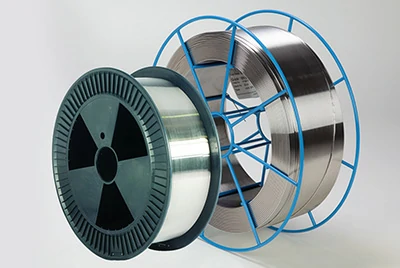
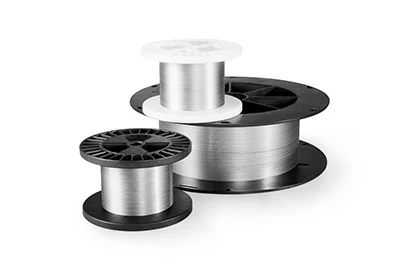
Titanium MIG Wire
Titanium MIG welding wire is suitable for automated welding, typically coiled and with smaller diameters, offering high welding efficiency, ideal for mass production.
Diameter: 0.8mm - 1.2mm
Applications: Automotive body, ship structures, industrial containers
Straight Titanium Welding Wire
Straight titanium welding wire is supplied in a fixed length (typically 1 meter), making it easy for manual operation and precise wire feeding, ideal for small batch or high-precision welding tasks.
Applications: Laboratory research, small equipment repairs, custom welding
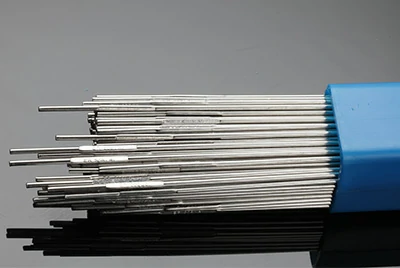
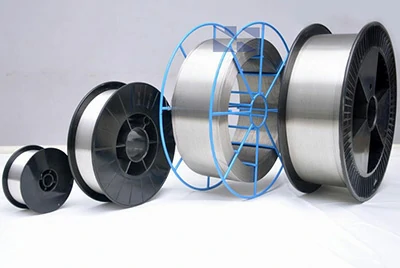
Coiled Titanium Welding Wire
Coiled titanium welding wire, often hundreds of meters long, is ideal for automated welding, reducing wire change frequency and boosting efficiency. Commonly used in large-scale manufacturing, such as automotive production lines, pressure vessels, and aerospace components.
Titanium Flux-Cored Wire
Titanium flux-cored wire contains flux inside, improving weld formation and gas porosity resistance, suitable for thick plate welding and complex environments.
Applications: Marine engineering, chemical equipment, heavy machinery
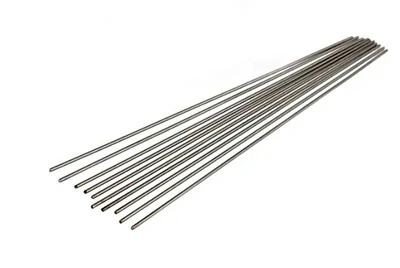
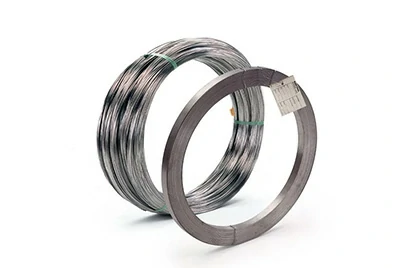
Titanium Strip Welding Wire
Titanium strip welding wire is flat and is ideal for laser welding and electron beam welding, enabling high-speed and high-precision connections, particularly for thin plate welding.
Applicationss: Electronic components, battery casings, precision instruments
Titanium Flux-Free Wire
Titanium flux-free wire has a clean surface, requiring no additional flux, ideal for high-purity welding environments such as semiconductor equipment and biomedical applications.
Applications: Ultra-high vacuum equipment, bioreactors, precision sensors
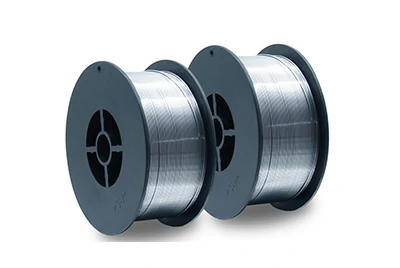
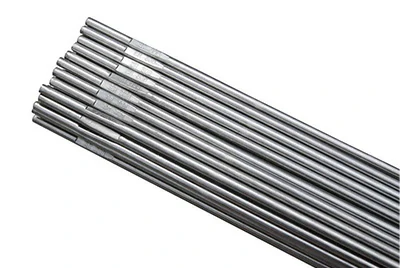
Titanium Clad Wire
Titanium clad wire consists of a titanium outer layer and a core material, combining the corrosion resistance of titanium with the special properties of the core material (such as high strength or conductivity).
Applicationss: Composite structure welding, special equipment manufacturing
Titanium Coated Wire
Titanium coated wire has a titanium coating on the base material, offering both the corrosion resistance of titanium and the mechanical properties of the base material, suitable for specialized welding needs.
Applications: Composite pipelines, special containers, high-temperature furnaces
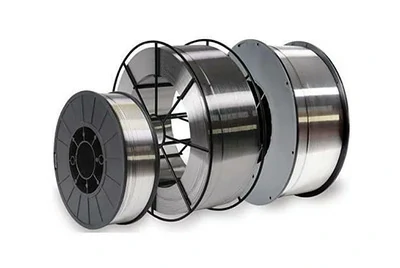
Common Titanium Welding Wire Alloys
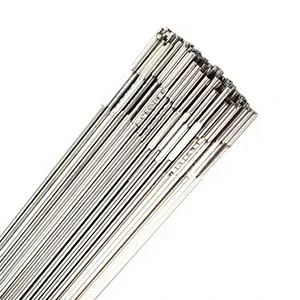
ERTi-2 Titanium Welding Wire
Features: The most widely used pure titanium welding wire in the industrial corrosion-resistant market, offering good strength, formability, and weldability.
Base Materials: Gr1, Gr2, Gr2, Gr4
Applications: Petrochemical pipelines, ship structures, cryogenic vessels
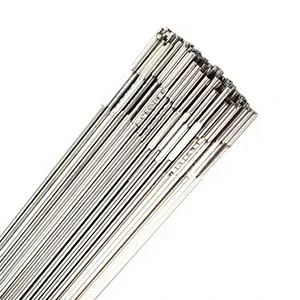
ERTi-5 Titanium Welding Wire
Features: The most commonly used and versatile titanium alloy welding wire, offering excellent overall performance.
Base Materials: Gr5
Applications: Aerospace engine components, orthopedic instruments
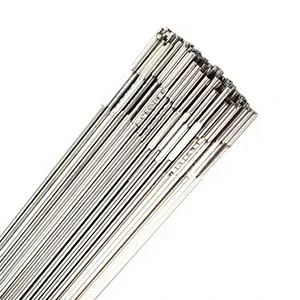
ERTi-1 Titanium Welding Wire
Features: The lowest strength pure titanium welding wire, with excellent ductility and strong corrosion resistance.
Base Materials: Gr1, Gr2, Gr2, Gr4
Applications: Chemical equipment, seawater heat exchangers
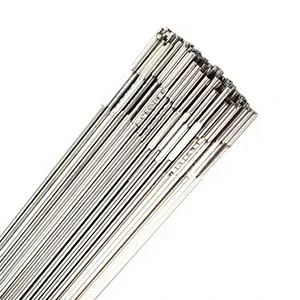
ERTi-4 Titanium Welding Wire
Features: The highest strength pure titanium welding wire, with outstanding corrosion resistance.
Base Materials: Gr1, Gr2, Gr2, Gr4
Applications: High-temperature valves, aerospace fasteners
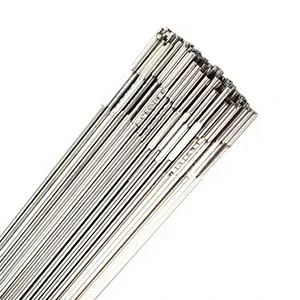
ERTi-7 Titanium Welding Wire
Features: Similar performance to ERTi-2, with the addition of 0.18% palladium (Pd), enhancing resistance to crevice corrosion.
Base Materials: Gr2, Gr16, Gr26
Applications: Chemical equipment, marine platform pipelines
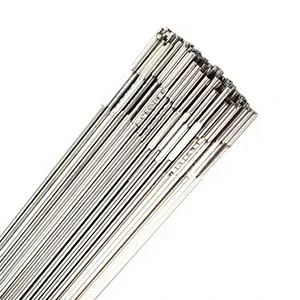
ERTi-12 Titanium Welding Wire
Features:Medium strength, with nickel (Ni) and molybdenum (Mo), excellent high-temperature saltwater corrosion resistance, and lower cost than ERTi-7.
Base Materials: Gr12, Gr16, Gr26
Applications:Deep-sea drilling, geothermal plant pipelines, nuclear plant heat exchangers.
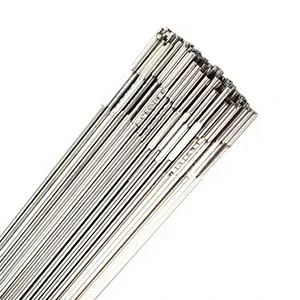
ERTi-9 Titanium Welding Wire
Features: "Half 6-4" titanium alloy, with half the aluminum and vanadium of ERTi-5, balancing strength and plasticity. Offers good cold formability, ideal for welding complex shapes.
Base Materials: Gr9
Applications: Hydraulic pipelines, bicycle frames, ship propellers
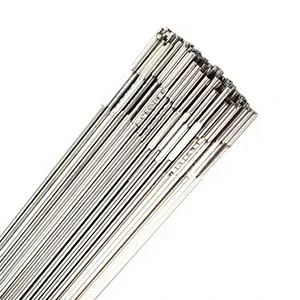
ERTi-23 Titanium Welding Wire
Features: Similar chemical composition to ERTi-5, but with ultra-low gap (ELI) gas content, offering higher fracture toughness.
Base Materials: Gr23
Applications: Artificial joints, cryogenic pressure vessels, aerospace cryogenic fuel tanks
Characteristics of Titanium Welding Wire
- Exceptional Corrosion Resistance: Titanium welding wire offers strong resistance to corrosion from seawater, acidic solutions, chloride ions, and other corrosive media, making it ideal for marine engineering, chemical equipment, and other harsh environments.
- High Strength-to-Weight Ratio: With a density only 60% of that of steel, titanium maintains comparable or even superior strength, making it particularly suitable for aerospace, automotive, and other weight-sensitive applications.
- Outstanding High-Temperature Performance: Some titanium alloy welding wires, such as ERTi-5, remain stable at temperatures above 600°C, making them suitable for jet engine components, high-temperature reactors, and similar applications.
- Biocompatibility: Medical-grade titanium welding wires, such as ERTi-5, can be used for welding orthopedic implants and dental instruments, avoiding adverse reactions in the human body.
- Welding Challenges: Titanium is highly susceptible to contamination from hydrogen, oxygen, and nitrogen, requiring strict control over the purity of protective gases (argon ≥ 99.99%) and the welding environment to prevent defects like porosity and embrittlement.
Applications of Titanium Welding Wire
Aerospace
Lightweight design improves fuel efficiency, while high-temperature resistance ensures reliability under extreme conditions.
Turbine Blades
Aircraft Frame
Satellite Structures
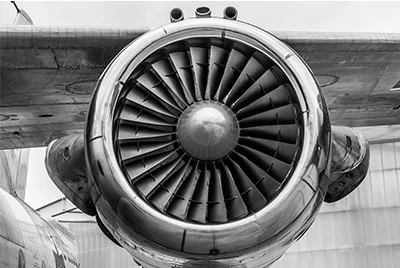

Chemical & Energy
Resistant to chloride ion corrosion, suitable for strong corrosive media such as sulfuric acid and hydrochloric acid.
Chemical Reactors
Nuclear Power Station Heat Exchangers
Oil & Gas Pipelines
Shipbuilding & Marine Engineering
Titanium-welded hulls resist salt mist corrosion, extending service life by over 30%.
Submarine Pressure Hulls
Offshore Platform Pipelinese
Propeller Shafts
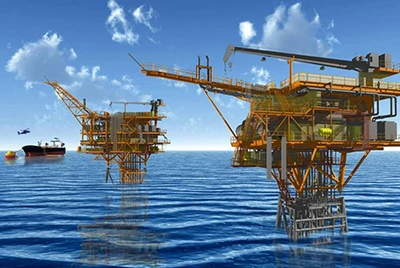
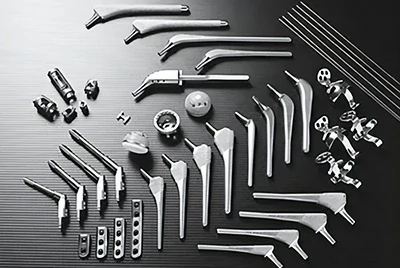
Medical Equipment
Excellent biocompatibility and corrosion resistance, meeting medical-grade standards like ASTM F136.
Artificial Joints
Cardiovascular Stents
Bone Fixation Devices
Surgical Instruments
Other Titanium Wires
Titanium Wire for Anodizing
High-purity titanium wire (Gr.1/2), easily oxidized to form a colored coating, used for surface treatment of jewelry, ornaments, and electronic components.
Advantages: High color stability, non-toxic, complies with body contact standards.
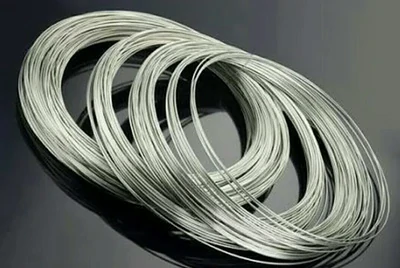
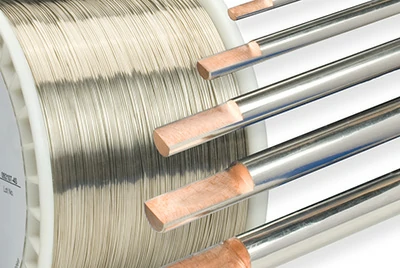
Titanium Clad Copper Wire
Copper core with a titanium cladding, combining titanium's corrosion resistance and copper's high conductivity, used in marine communication cables and chemical equipment grounding wires.
Advantages: Lower cost than pure titanium cables, conductivity exceeds 95% of copper.
Braided Titanium Wire
Multiple strands of titanium wire braided into a flexible mesh structure, resistant to high temperatures and wear, used as high-temperature sealing fillers or electromagnetic shielding materials.
Applications: Aerospace engine seals, nuclear reactor shielding.
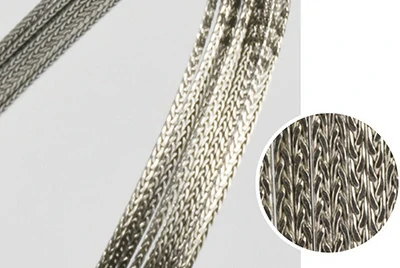
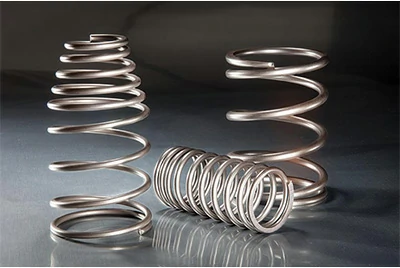
Titanium Spring Wire
High-elasticity titanium alloy wire (e.g., Ti-3Al-2.5V), highly fatigue-resistant, suitable for spring components in high-temperature or corrosive environments.
Applications: Automotive engine valve springs, aerospace shock absorbers.
Titanium Jewelry Wire
Titanium wire that can be anodized for coloring, lightweight, hypoallergenic, used for handmade crafts, earrings, and necklaces. Advantages: Multiple colors (blue, purple, gold, etc.), hardness higher than silver jewelry.
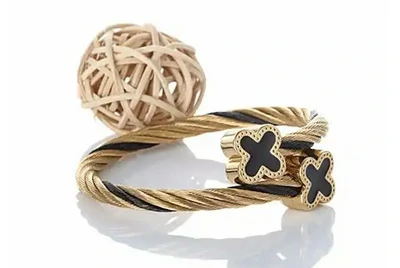
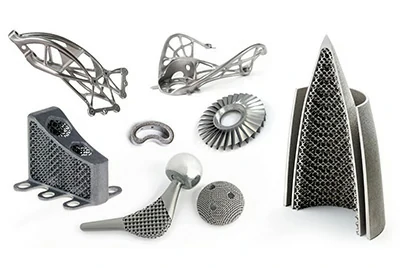
Titanium Wire for 3D Printing
High-precision titanium wire used for metal additive manufacturing, supporting laser cladding (DED) processes.
Diameter: 1.2mm±0.05mm
Applications: Customized aerospace parts, complex medical implants.
Titanium Wire Mesh
Titanium wire woven into a mesh structure, resistant to acid and alkali corrosion, used for chemical filtration and seawater aquaculture nets.
Applications: Electrolytic cell electrodes, lithium battery separator support layers.
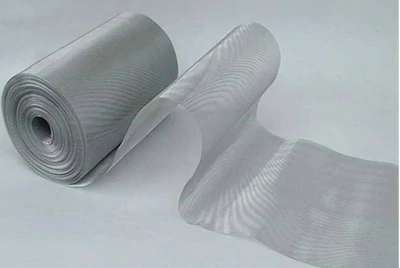
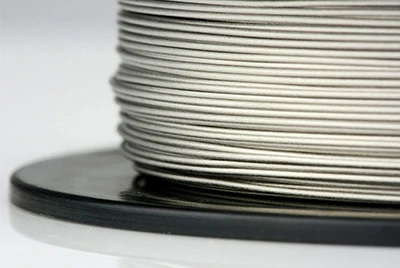
Titanium Cables
Titanium wire twisted into cables, resistant to seawater corrosion, high tensile strength, used for deep-sea exploration equipment and marine platform ropes.
Advantages: Lightweight (only 60% of steel cable's density), longevity of over 30 years.
Cases: Deep-sea exploration titanium cables used in the Jiaolong submersible.
Titanium Resistance Wire
High-resistance titanium alloy wire (e.g., Ti-6Al-4V), resistant to high-temperature oxidation, used for electric heating elements and high-temperature sensors.
Applications: Vacuum furnace heating elements, automotive exhaust gas detection probes.
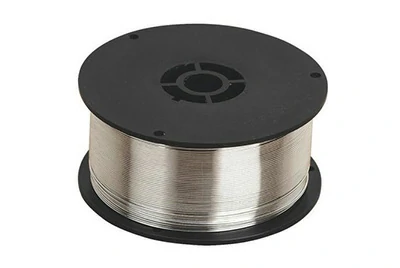
Titanium Wire Customization
In the field of titanium wire products, we understand the diversity and individuality of customer needs. Therefore, we offer comprehensive customization services to meet the special requirements of different industries and application scenarios.
1. Custom Alloy Composition
The performance of titanium wire largely depends on the alloy composition. We can customize titanium wire with different alloy compositions according to your specific application needs.
- Element Ratio Optimization: By adjusting the content of elements such as Aluminum (Al), Vanadium (V), and Molybdenum (Mo), we can tailor the titanium wire's strength, high-temperature resistance (e.g., Ti-6Al-4V can serve at up to 400°C for long periods), or biocompatibility (e.g., medical-grade Ti-12Ta-9Nb-3V).
- Technical Assurance: Equipped with vacuum arc remelting (VAR) and chemical composition spectrometers, we ensure that the composition deviation is ≤ 0.05%.
2. Specific Size and Tolerance Control
We offer titanium wire in various diameters and lengths, with strict tolerance control to meet your dimensional precision requirements. Whether you need ultra-fine wire for medical implants or thicker wire for industrial applications, we can meet your needs.
- Diameter Range: From 0.01mm (for electronic bonding wire) to 20mm (for structural reinforcement), we also support custom non-standard profiles (e.g., flat wire, hexagonal wire).
- Tolerance Precision: Utilizing multi-pass cold drawing and online laser diameter measurement technology, we provide a conventional product tolerance of ±0.001mm, with ultra-precision wires reaching ±0.0005mm (e.g., for semiconductor packaging wire).
- Strict Dimension Control: We use advanced measuring equipment for both online and offline inspections, ensuring that each batch meets customer requirements.
- Precision Drawings and Test Reports: We provide accurate dimension drawings and test reports based on different processing or application environments, meeting the requirements of high-standard fields such as aerospace, medical devices, and chemical equipment.
3. Surface Treatment
The surface quality of titanium wire directly affects its weldability, appearance, and corrosion resistance. Some application scenarios may require surface cleaning, polishing, anodizing, coating, or other special treatments to improve its processing performance or extend service life.
- Multiple Surface Treatment Options: We offer various surface treatment options such as mechanical polishing, chemical cleaning, anodizing, coating, etc., based on customer-specific process requirements.
- Strict Process Control: The surface treatment process is strictly controlled and tested to ensure uniform and stable treatment effects, improving product corrosion resistance and aesthetics.
- Custom Surface Treatment Solutions: For special environmental requirements, we can develop personalized surface treatment plans to optimize welding, connection, and subsequent processing, reducing issues caused by surface defects.
4. Packaging Methods
Titanium wire products are susceptible to environmental contamination and mechanical damage during transportation and storage. Proper packaging not only ensures product integrity but also meets customer needs in different logistics environments.
- Various Packaging Options: We provide different packaging methods such as spools, straight lines, coils, etc., based on your needs.
- Custom Packaging Choices: We offer multiple packaging options, including moisture-proof packaging, anti-static packaging, vacuum packaging, or custom external packaging boxes.
- Protection During Packaging: We focus on the protective performance during the packaging process to ensure the product avoids scratches, oxidation, or other physical damage during transportation.
- Custom Labels and Documentation: Based on customer sales and logistics channels, we can also customize labels, quality manuals, and other information, making the product packaging not only secure and practical but also aligned with brand promotion and marketing needs.
Chalco Titanium Wire Production Capacity: Leading Technology and Full Industrial Chain Advantage
Standard Certifications: Industry Benchmark, International Recognition
We strictly follow the national standard GB/T 3623-2022 for "Titanium and Titanium Alloy Wire" and meet international standards such as ASTM B863 (USA), JIS H4650 (Japan), etc. Our products are certified under the ISO 9001 Quality Management System, ensuring product quality and consistency. Additionally, we have obtained the AS9100 aerospace quality management system certification, meeting the stringent requirements of the aerospace industry.
Product Range: Full Category Coverage, Customization Services
Material Diversity: We offer pure titanium (Gr1, Gr2, Gr3, Gr4), titanium alloys (Gr5, Gr9, Gr23, etc.), special alloy wires (e.g., medical titanium wire, ophthalmic titanium wire), and titanium welding wire (ERTi2, ERTi5, ERTi9, etc.).
Forms and Functions: We provide acid-pickled titanium wire (hot-working state), bright titanium wire (cold-drawn annealed state), special-shaped titanium wire (flat wire, wedge-shaped), and composite coated wires (e.g., oxidation-resistant coatings), supporting applications in welding, braiding, and precision component processing.
Specifications and Sizes: High Precision and Ultra-Fine Wire Technology
Diameter Range: From 0.03mm to 6mm (cold-drawing process achieves ultra-fine wire with precision of ±0.005mm). We support large coil weights (up to 500kg per coil) to meet continuous automated production demands.
Further Processing: We provide services such as flattening, polishing, and slitting, with flat titanium strips available in thicknesses from 0.05mm to 1.2mm and flatness control within ±3%.
Quality Control: Full-Process Digital Monitoring
Process Innovation: We use vacuum arc remelting (VAR) and multi-pass rotary forging and drawing technology to ensure material purity (oxygen content ≤0.15%) and consistent mechanical properties (tensile strength fluctuation ≤5%).
Testing System: Advanced laser diameter measuring instruments and eddy current flaw detection provide real-time monitoring of the production process to ensure product size accuracy and surface quality. We also conduct 100% quality checks, including metallographic analysis and mechanical performance testing, to ensure the products meet the highest standards.
Stable Supply: Scalable Capacity and Agile Response
Production Capacity Guarantee: With an annual production capacity exceeding 2,000 tons, we are equipped with fully automated drawing machine units (drawing speed up to 20m/s) and an intelligent warehousing system, supporting large orders with delivery cycles of ≤15 days.
Inventory Strategy: We maintain stock of popular grades such as Gr2, Gr5 (diameter 0.2mm-3.0mm), covering 80% of standard demand, and provide urgent order response within ≤72 hours.
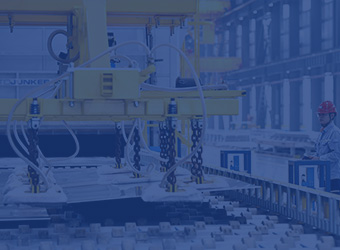