Titanium Surface Treatment
Updated : Mar. 17, 2025Titanium materials, known for their excellent corrosion resistance and lightweight properties, are widely used across various industries. Surface treatment technologies further enhance their performance by improving wear resistance, oxidation resistance, and appearance to meet specific industry needs.
Surface purification technology
The main purpose of surface purification is to improve the cleanliness of titanium and titanium alloy surfaces and remove unnecessary substances on the surface, such as burrs, flash, oil stains, reaction layers, etc. Common surface purification methods include:
Removing burrs and flash: mainly done by mechanical processing (such as grinding) or chemical removal.
Removing surface oil stains: removing oil stains by solvent cleaning, ultrasonic cleaning or chemical cleaning.
Removing surface reaction layer: titanium surface is prone to forming reaction layer, which affects surface quality. Sandblasting and pickling are common treatment methods.
- Sandblasting: Use white corundum for sandblasting, control the sandblasting pressure (generally less than 0.45 MPa), and the sandblasting time is within 15-30 seconds to remove the surface sintering layer and part of the oxide layer.
- Pickling: Pickling can completely remove the surface reaction layer of titanium. Commonly used pickling solutions are HF-HCl and HF-HNO3 acid solutions. Among them, HF-HNO3 pickling solution is more ideal because it absorbs less hydrogen and does not produce too much pollution.
Usually applicable to the following scenarios:
Titanium alloy castings: There are usually burrs, flash and contamination layers on the surface of titanium alloy after casting. Sandblasting or pickling is required to remove the surface reaction layer to ensure the smooth progress of subsequent processing.
Precision machining: Before precision machining of titanium alloy, it is necessary to ensure that there are no contaminants on the surface to improve machining accuracy and reduce defective product rate.
Preparation before welding: The surface of titanium material needs to be purified to remove oxide layer and oil to ensure the quality and strength of the welded joint.
Corrosion resistant surface treatment
Titanium alloy itself has strong corrosion resistance, but in some extreme environments (such as high concentration of hydrochloric acid, sulfuric acid, etc.), the titanium surface may corrode. Therefore, in response to these needs, special corrosion resistance treatment is sometimes performed on the titanium surface.
Atmospheric oxidation treatment: Titanium is placed in a high temperature atmosphere to form an oxide film to enhance the corrosion resistance of titanium. Although atmospheric oxidation treatment is simple and low cost, its corrosion resistance may gradually weaken over time, so it is not suitable for parts that operate stably for a long time.
Anodizing treatment: Electrolysis is used to generate a thick oxide film on the titanium surface, thereby improving corrosion resistance and wear resistance. Through anodizing, different colors can also be given to the titanium surface, providing a beautiful appearance for titanium alloys. H2SO4, H3PO4, etc. are commonly used electrolytes. Click to learn more about titanium anodizing.
Applicable scenarios:
Marine environment: Titanium is widely used in seawater equipment, such as components of offshore platforms and ships, where corrosion resistance is particularly important. Atmospheric oxidation or anodizing can enhance titanium's resistance to saltwater corrosion.
Chemical industry: In harsh chemical corrosion environments (such as acidic solutions, sulfuric acid, hydrochloric acid, etc.), corrosion-resistant titanium surfaces can extend the service life of equipment and reduce maintenance costs.
Oil and gas extraction: Titanium alloys face highly corrosive environments (such as oil and gas wells) in oil and gas extraction equipment. Anodic oxidation and atmospheric oxidation can significantly improve their corrosion resistance.
Anodizing products Chalco can provide:
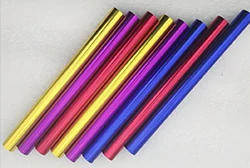
Anodized titanium tube
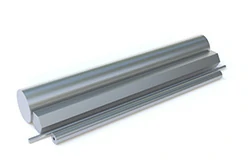
Anodized titanium bar
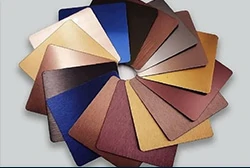
Anodized titanium plate
If you need any anodized titanium products, please contact us.Quick Quote
Wear-resistant surface treatment
Titanium has poor wear resistance, so in some applications that require higher wear resistance, it needs to be surface strengthened. Common treatment methods include:
Wet coating: Electroplating technology is used to plate materials such as chromium (Cr) or nickel phosphorus (NiP) on the titanium surface to improve wear resistance.
Thermal diffusion method: Carburizing, nitriding and other technologies are used to form a hardened layer on the titanium surface to improve its wear resistance.
Overlay welding: Overlay welding by plasma transferred arc can improve the wear resistance of the titanium surface and is suitable for large-sized titanium workpieces.
Sputtering method: Metal materials are sprayed on the titanium surface through a high-speed plasma jet to enhance its wear resistance.
Plasma nitriding technology: A hardened nitride layer is formed on the surface of the titanium alloy through plasma nitriding, ion plating and other technologies to improve its wear resistance and corrosion resistance.
Applicable scenarios:
Mechanical parts: In mechanical parts with more sliding and friction, titanium alloys often cause surface wear due to insufficient wear resistance. Surface treatment methods such as chrome plating and nickel plating can significantly improve its wear resistance and are suitable for high-friction parts such as aircraft engine parts, gears, and bearings.
High-performance sports equipment: For example, titanium alloy parts of golf heads and sports shoes have high wear resistance requirements. Ion implantation and CVD coating treatment can effectively extend their service life.
High-load parts: In situations involving high pressure and strong friction (such as oil drilling and automobile engine parts), wear-resistant treatment can significantly improve the durability of titanium parts and reduce the frequency of maintenance.
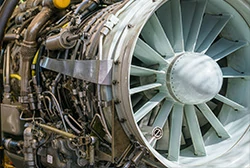
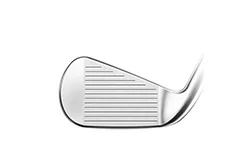
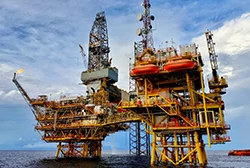
Design surface treatment
Design surface treatment is mainly to meet the aesthetics and special needs of customers. Common treatment methods include:
Surface finishing: Through grinding, annealing, shot peening and other methods, the surface is flat, smooth or has a special texture.
- Grinding: Make the surface smooth and shiny.
- Annealing and pickling: Make the surface gray and dull.
- Shot peening: Use glass beads to make the surface look like pear skin.
- Chemical etching: Etch patterns or text on the titanium surface to increase the decorative effect.
Mirror polishing: Mirror polishing of titanium is more difficult. Common methods include soft belt polishing, chemical polishing and electrolytic polishing.
- Soft belt polishing: mainly uses a polishing belt to polish the surface, suitable for simpler surfaces.
- Chemical polishing: uses chemical reactions to remove uneven parts of the titanium surface to obtain a smooth surface.
- Electrolytic polishing: uses electrochemical methods to make the titanium surface have a high gloss, suitable for more complex shapes.
Coloring: Using atmospheric oxidation, chemical coloring, and other methods to give the titanium surface different colors, enhancing its decorative appeal.
- Atmospheric oxidation method: By heating the titanium material, an oxide film is formed on its surface, thereby changing the color. This method is low-cost, but the coloring effect is not stable enough.
- Chemical coloring: A colored oxide film is formed on the titanium surface through chemical reactions.
Applicable scenarios:
- Architectural decoration: The natural silver-white color of titanium is not suitable for all decorative requirements. Anodizing can give titanium different tones, such as gold, blue, purple, etc., which are widely used in building facades, curtain walls and interior decoration.
- Jewelry and high-end consumer goods: Due to the hardness and unique appearance of titanium, anodizing and mirror treatment technology can be used to make fashion jewelry, high-end watches and luxury accessories to meet the market's demand for personalization and beauty.
- Medical devices: Titanium parts in medical devices (such as dental implants, orthopedic implants, etc.) require not only excellent mechanical properties, but also good appearance. Chemical polishing and electrolytic polishing can improve the surface finish and beauty.
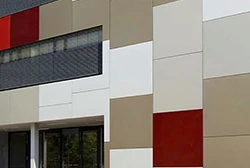
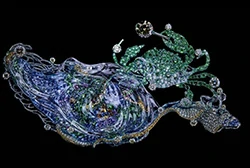
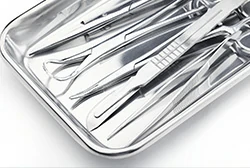
Through advanced titanium surface treatment technology, Chalco is able to provide high-quality titanium products that meet the stringent requirements of different industries for corrosion resistance, wear resistance and aesthetics. Whether it is aerospace, medical equipment or industrial applications, Chalco is always committed to providing customers with excellent titanium material solutions to ensure that each product has reliable performance and lasting quality assurance.